Støping av A-en

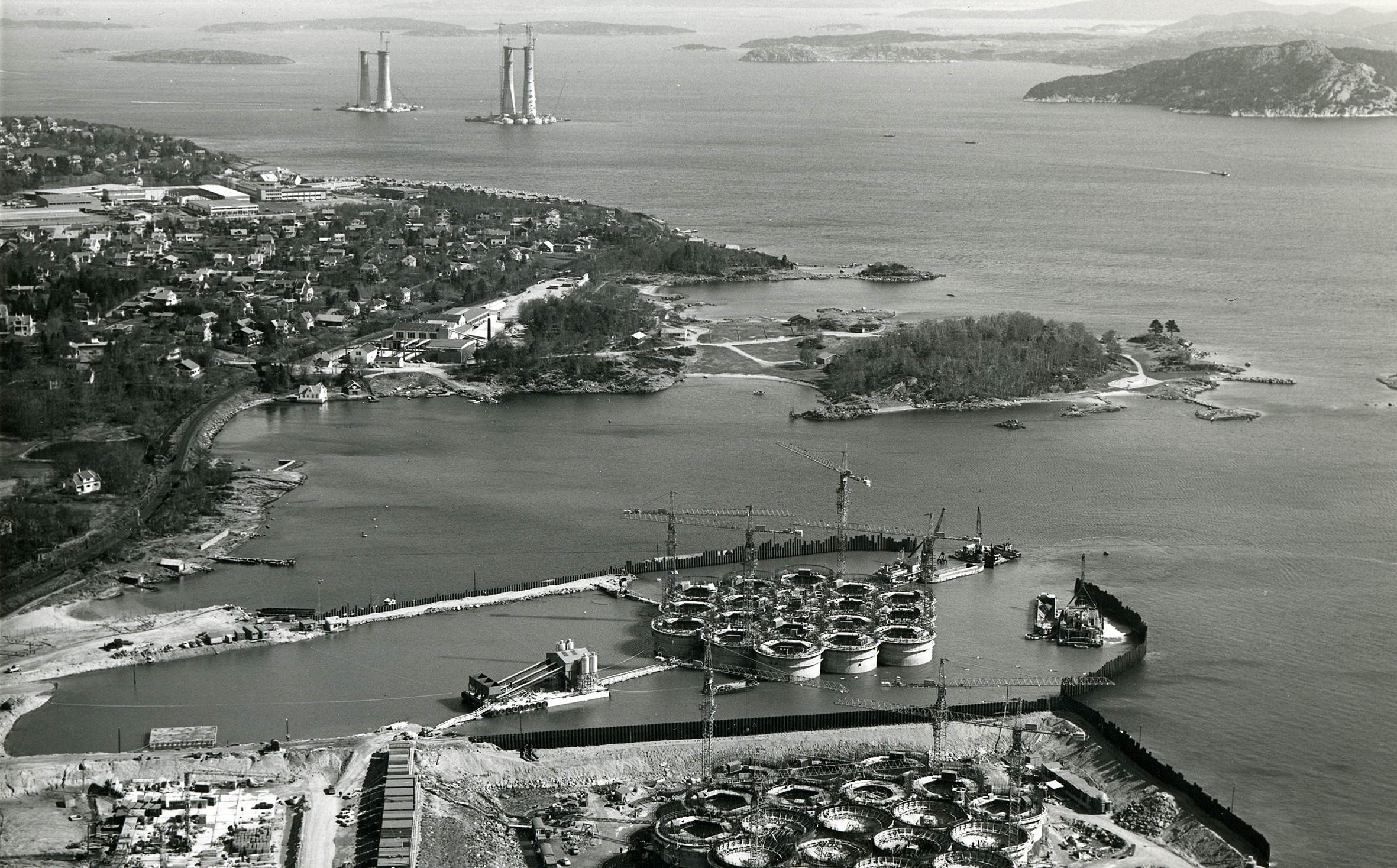
Høsten 1974 lå Mobils Beryl A og Shell/Esso sin Brent B forankret på dypt vann i fjorden og i byggedokken i Hinnavågen var arbeidet i gang med foruten Statfjord A, og Shell sin Brent D.
Alle fire var såkalte Condeeper – Concrete Deepwater Structures, eller understellskonstruksjon av betong. Dette var en av flere typer betongplattformer; andre kjente typer betongunderstell var ANDOC, utviklet og bygget av McAlpine i Ardyne Point, Sea Tank, C.G. Doris som Ekofisktanken er et eksempel på og Arup Concrete Gravity Substructure – CGS. Betongplattformer blir også kalt GBS eller Gravity Base Structure, som betyr en konstruksjon som står i ro på havbunnen av sin egen vekt.
Condeep var et norsk design utviklet av entreprenørselskapet Høyer-Ellefsen. Den 13. juli 1973 mottok selskapet sammen med entreprenørselskapet Ingeniør F. Selmer A/S og Akergruppen, som skulle stå for utrustningen, bestilling på den aller første Condeep. Bestillingen kom fra britiske Mobil North Sea Limited til bruk på Beryl-feltet.
Byggingen var en stor utfordring og Høyer-Ellefsen og Selmer gikk sammen med et tredje entreprenørselskap, Ingeniør Thor Furuholmen A/S om utførelsen.[REMOVE]Fotnote: Steen, &., & Norwegian Contractors. (1993). På dypt vann : Norwegian Contractors 1973-1993. Oslo: [Norwegian Contractors]: 16. De tre selskapene slo seg sammen til Norwegian Contractors – NC.
Før bestillingen av Beryl A hadde Mobil hentet inn anbud fra syv forskjellige selskaper som foreslo forskjellige stål- og betongløsninger for levering i 1975.
Etter nøye gjennomgang av alle anbudene valgte Mobil å satse på condeepløsning. Den kom godt ut prismessig og NC-gruppen hadde erfaring med betongarbeid gjennom byggingen av Ekofisktanken noen år tidligere. I tillegg hadde Condeep en fundamenteringsløsning som passet bunnforholdene på Berylfeltet. Disse argumentene oppveide det faktum at Condeep var en helt ny anvendelse av teknologi, det var et pionerprosjekt.[REMOVE]Fotnote: Steen, &., & Norwegian Contractors. (1993). På dypt vann : Norwegian Contractors 1973-1993. Oslo: [Norwegian Contractors]: 16.
At også Statfjord A ble en condeep skyltes i første rekke at Mobil hadde inngått en opsjon på bygging av en Condeep nummer to tenkt brukt som Beryl B. Da det ikke ble nødvendig, tilbød det britiske Mobil opsjonen til Mobil Norge og Statfjordlisensen. Mobil var da innforstått med at Statfjordfeltet skulle bygges ut snarest mulig.[REMOVE]Fotnote: Moe, J. (1980). Kostnadsanalysen norsk kontinentalsokkel : Rapport fra styringsgruppen oppnevnt ved kongelig resolusjon av 16. mars 1979 : Rapporten avgitt til Olje- og energidepartementet 29. april 1980 : 1 : Sammenfatning av utviklingen, vurderinger og anbefalinger (Vol. 1). Oslo: [Olje- og energidepartementet]: 141.
Men for alle felt, også Statfjord, er det reservoaret som i hovedsak bestemmer hva slags produksjonsinnretning en bør ha. Reservoaregenskaper, design av produksjons-/injeksjonsbrønner, trykk- og temperaturforhold og olje- og gass-kvaliteter må tas hensyn til. I tillegg må man beslutte hvordan oljen og gassen skal eksporteres fra feltet.
I 1974/75 da man tok beslutningene om hvordan Statfjord A skulle bygges, hadde man svært begrenset informasjon om disse forhold. Etterhvert som leteboringen ble utført fikk man mer informasjon om reservoaret, som igjen ga grunnlag for reservoaranalyser, analyser av produksjonsegenskaper, olje- og gass-forhold og så videre, og som igjen ble grunnlaget for design av produksjonssystemene på plattformen.
Opsjonen på Beryl B, tilgjengelig for Mobil, ga en mulighet for å komme raskt i gang. Statfjord-lisensen besluttet å benytte muligheten og var klar over at prosjektet ble startet med svært begrenset reservoarinformasjon. En måtte påregne vesentlige forandringer av design i forhold til Beryl A. De som tok beslutningen hadde i tillegg begrenset erfaring med utbygging av en så stor og kompleks plattform som Statfjord A og forutså nok ikke fullt ut hva konsekvensen av den begrensede forprosjekteringen innebar.[REMOVE]Fotnote: Intervju med Einar Jensen 2. oktober 2008, av Trude Meland Norsk Oljemuseum.
Gliden
NC hadde fått leiekontrakt av Stavanger kommune om bruk av Hinnavågen og ankerfester i Gandsfjorden. De fylte ut viken i Hinna for å lage tørrdokk, i tillegg til å tilrettelegge for lagerbygg og brakkeby på markene ovenfor.[REMOVE]Fotnote: Stangeland, P. (1977). Condeep : En arbeidsplass i Stavanger (Vol. 1/77, Rapport (Rogalandsforskning : trykt utg.)). Stavanger: Rogalandsforskning: 157.
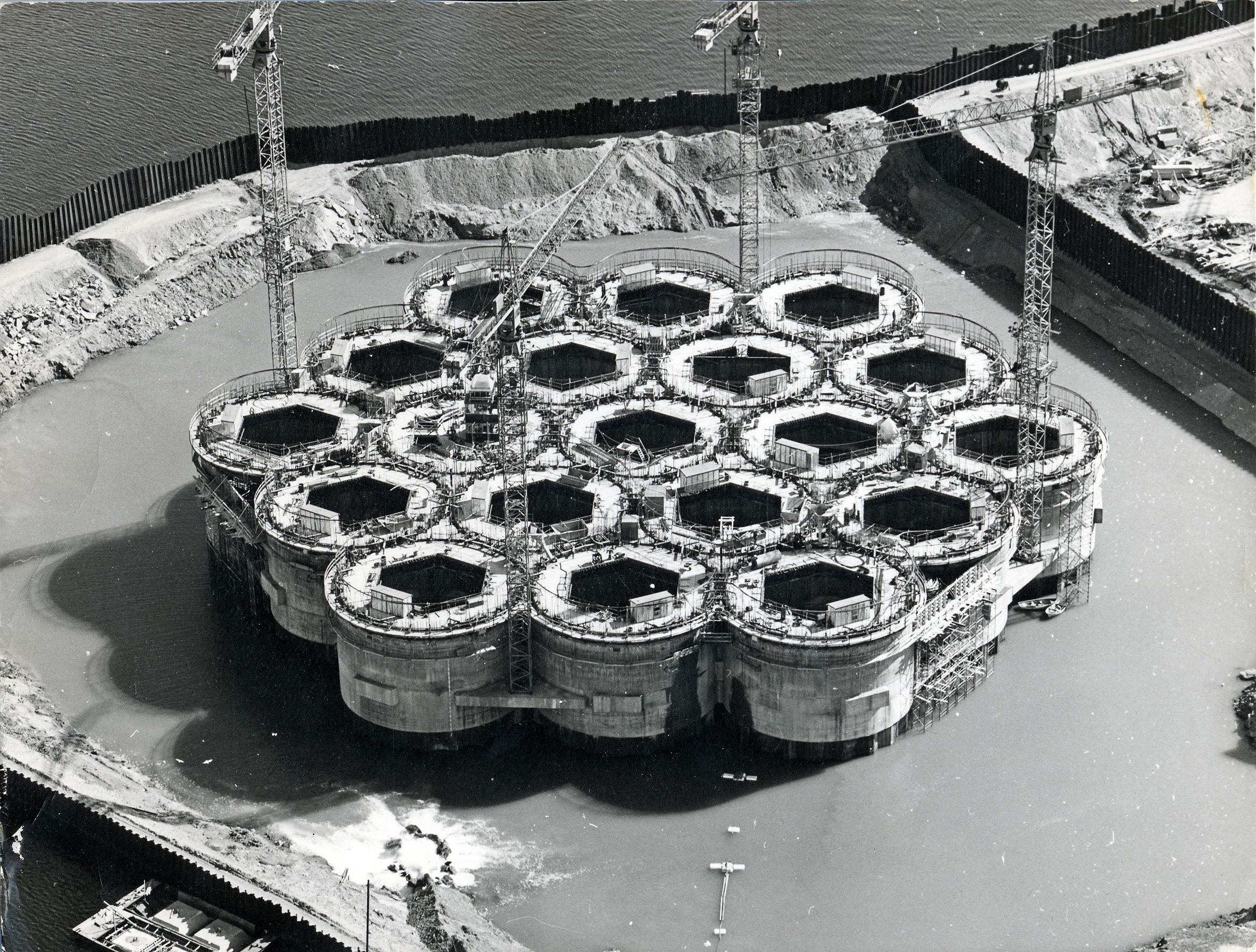
Første del av konstruksjonen ble støpt i denne tørrdokken. Men før selve støpingen av betongen kunne starte, måtte det monteres et såkalt «stålskjørt» under hver celle. Stålskjørtet skulle grave seg ned i havbunnen og sikre plattformens stabilitet.[REMOVE]Fotnote: Norsk Oljerevy. (1977) Nr. 3. 17-18. Statfjord “A” – den første i sitt slag etter nytt regelverk
Oppå skjørtet ble det støpt 19 betongceller opp til 14 meters høyde. Da dette arbeidet var ferdig, ble dokken fylt med vann slik at konstruksjonen fløt. Den ble tauet ut og ankret opp i fjorden omlag en kilometer fra land. Fra da av måtte alt utstyr og alt mannskap fraktes ut og inn med båt.
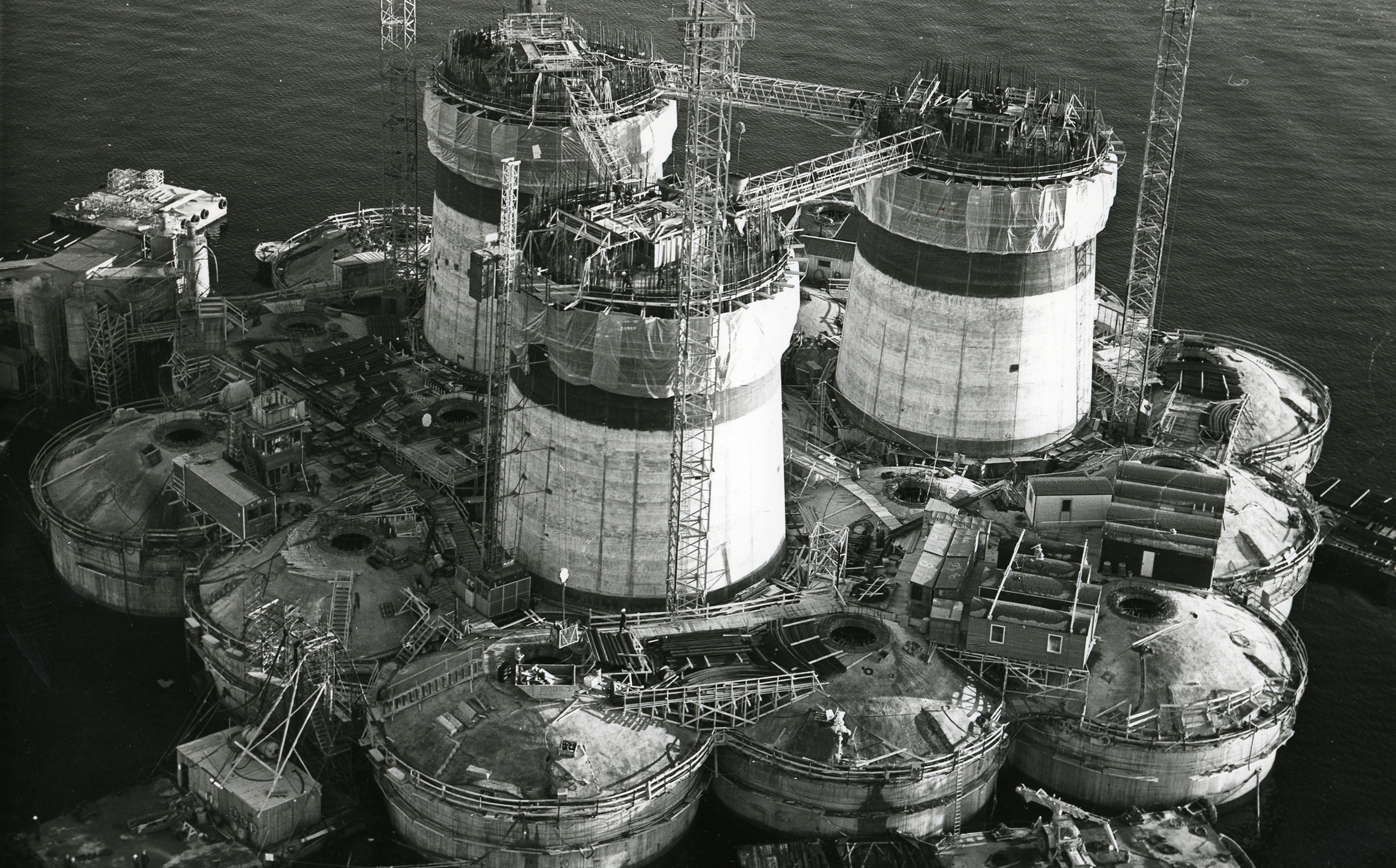
15 celler var planlagt som lagringstanker for råolje og en av cellene var lagringstank for diesel til drift av maskineriet på plattformen. De tre siste cellene skulle fortsette oppover som skaft som dekket skulle hvile på toppen av. Støpingen av cellene i Hinnavågen gikk uten problemer eller forsinkelser og i mai 1975 ble den slept ut i Gandsfjorden for videre glidestøping.
Glideforskaling er en bevegelig forskaling som glir oppover i takt med at betongsøylene vokser. Forskalingen ble skjøvet oppover av en løftemekanisme.[REMOVE]Fotnote: Stavanger Aftenblad (19759 8. februar. Gliden på CONDEEP.
Først ble de 19 cellene støpt i full høyde til 70 meter. Konstruksjonen ble senket ned i sjøen etter hvert som veggene ble ferdigstøpt. Gliden vokste med 15 millimeter for hvert 7. minutt, noe som tilsa tre meter i døgnet.[REMOVE]Fotnote: Stavanger Aftenblad (1975) 8. februar. Gliden på CONDEEP. Flytende betong ble helt opp i forskalingen før betongen under hadde stivnet helt – vått i vått. For å unngå brister i betongen måtte støpningen skje kontinuerlig døgnet rundt på denne måten.
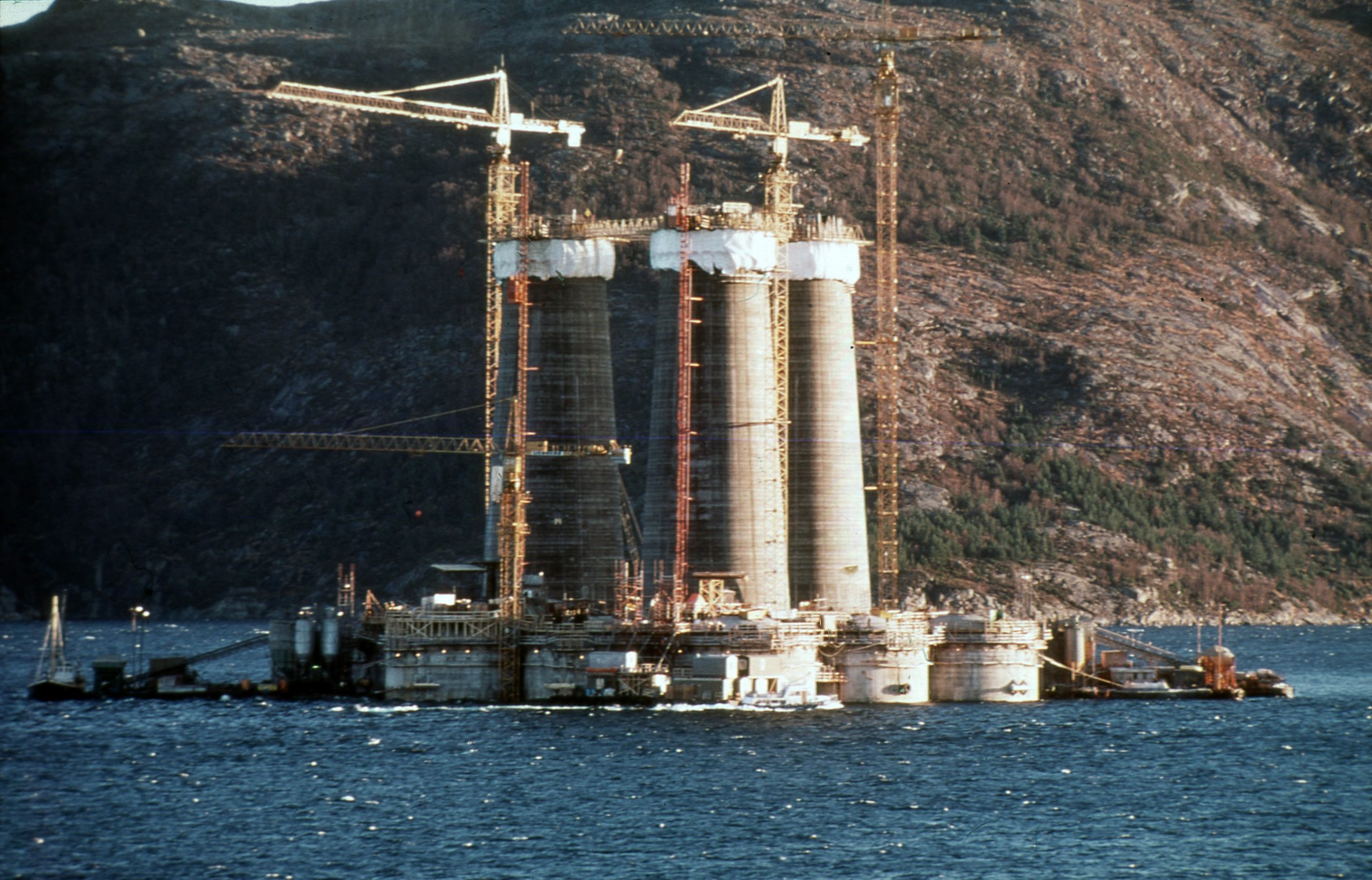
Da cellene var ferdige, fortsatte arbeidet med å støpe skaftene. Tre av cellene skulle forlenges med 100 meter.[REMOVE]Fotnote: Norsk Oljerevy. (1977) Nr. 3. februar. 17-18. Statfjord “A” – den første i sitt slag etter nytt regelverk. De tre skaftene ble støpt parallelt.
Condeep
Ved støping av cellene ble det brukt forskalingsformer som var 1,20 meter høye og mellom 60 og 80 cm brede og den flytende betongen ble hellet ned i de ferdiglagte støpeformene. Jernbinderne hadde på forhånd bundet armeringsjernet. Det gikk med rundt 40 tonn jern og 2200 tonn betong for hver meter glid. Ved støping av skaftene, tårngliden, ble det brukt stålformer som forskaling. Dette var en mer komplisert prosess siden skaftene skrådde innover. Den nederste delen av skaftene har en utvendig diameter på 20,60 meter og den øverste delen en diameter på 12,20 meter. Ved hjelp av et detaljert skruesystem ble skaftets form kontrollert. Hver fjerde cm ble skaftet målt.[REMOVE]Fotnote: Stavanger Aftenblad (1975). 8. februar. Gliden på CONDEEP.
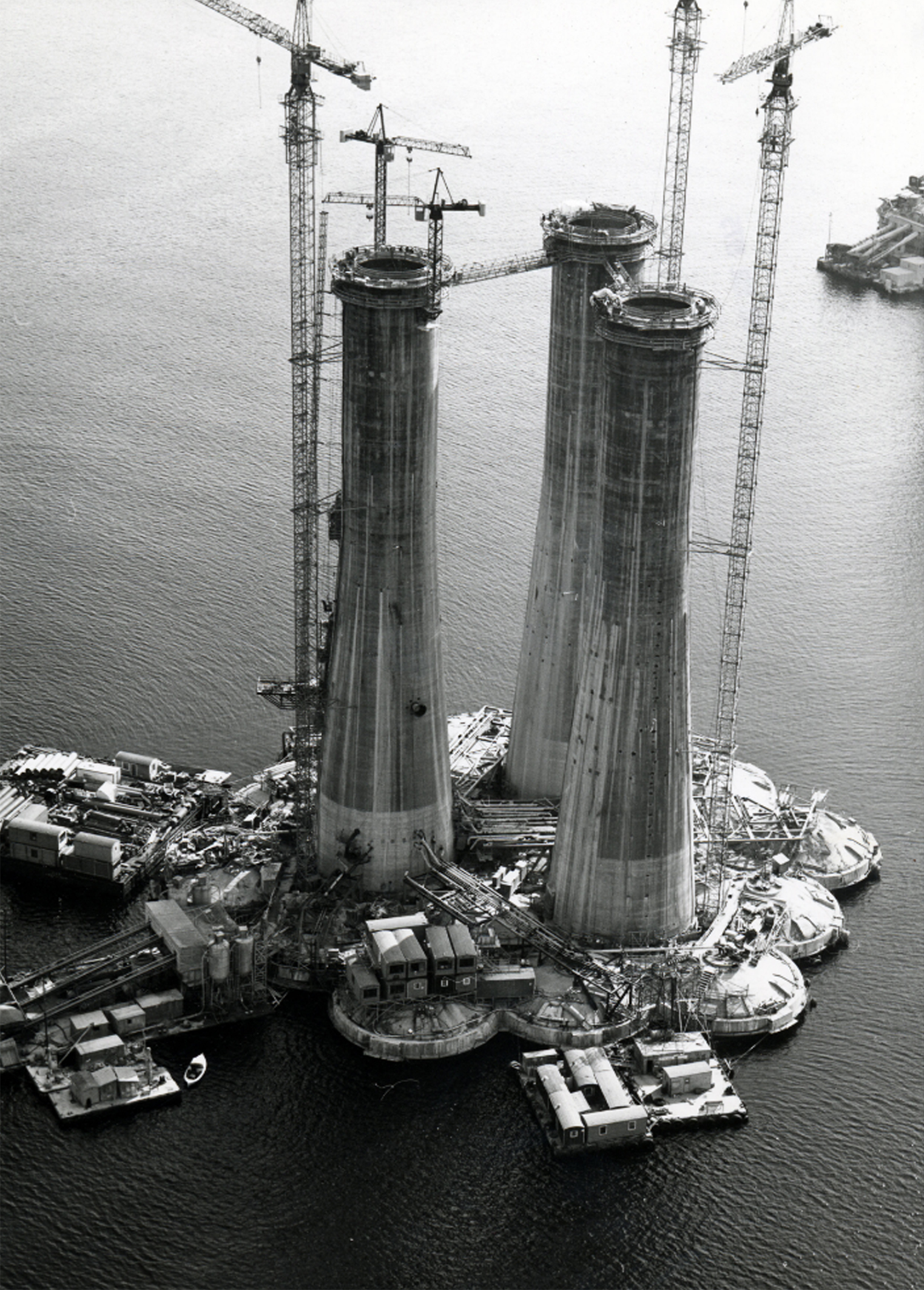
Skaftene fortsatte opp med en svak innsnevring. To av skaftene var boreskaft hvor brønnene til reservoaret skulle gå gjennom, 21 brønner i hvert. Det siste skulle brukes som utstyr- eller servicesskaft, hvor blant annet pumpeanlegg til overføring av råolje, brannvannsystem og ballastvann til og fra lagringstankene skulle stå.
Ved siden av condeepen lå et flytende betongblandeverk på lekter. Denne var fortøyd til betongstrukturen og under arbeidet med skaftene måtte betong og armeringsjern og annet utstyr heises opp ved hjelp av kraner. For mannskapet var det montert en heis på utsiden av hvert av skaftene og på toppen var det satt opp et stillas med rekkverk hvor arbeiderne kunne stå trygt. Da støpeformene ble jekket oppover, fulgte stillaset med opptil 100 mann i arbeid, sakte opp sammen med det.
Utrustning
Mens understellet fortsatt lå i tørrdokken, startet Aker Offshore Contractors arbeidet med utrustningen av cellene. Dette arbeidet fortsatte parallelt med støpingen også etter at understellet var forankret ute i Gandsfjorden. Det var arbeid under vanskelige forhold.
Arbeidsstedet var trangt, inne i skaftene var det rundt 15 meter i diameter. Utstyr ble låret ned ved hjelp av kraner eller tatt inn gjennom midlertidige åpninger nederst i betongveggen. Noe av arbeidet var å montere dekk, kalt sandwich-plater, inne i skaftene og det ble dermed arbeidet i mange høyder. Det var til slutt 13 dekk fordelt mellom de 177 meterne skaftet raget opp.
Det kunne være opp til 240 mann i arbeid samtidig i et skaft. Arbeidet besto i mye montering på steder med fritt fall på 15 til 20 meter.
Siden arbeidsarealet var lite og trangt kunne ikke alt arbeid utføres og alle mann jobbe samtidig. Noen måtte vike plassen for andre. Forskjellige fagfelt fikk dermed forskjellig prioritering; første, andre og tredje prioritet, noen helt nede som fjerdeprioritet. Hvilke grupper som hadde hvilken prioritet endret seg fra uke til uke etter som gliden gikk opp. Noen måtte vike for at andre skulle få gjort jobben på samme sted.[REMOVE]Fotnote: Intervju med Svein Jørpeland, av Trude Meland Norsk Oljemuseum.Norwegian Contractors eide noen store kraner som de brukte til å løfte betong, jern og annet utstyr opp på toppen. Aker fikk disponere kranen fire timer på dagtid og fire timer på natten for å få inn sitt utstyr i skaftene. Det var mye utstyr som skulle inn og all aktivitet måtte planlegges ned på detaljnivå slik at de timene kranen var tilgjengelig ble benyttet mest mulig effektivt.
Til ekstra hjelp hadde Aker en stor flytekran på 300 tonn. Den hadde relativt stor rekkevidde. På en så stor mobilkran kunne uteliggeren (bommen) tas ganske langt ut, men jo lengre uteliggere ble langt ut, jo lettere måtte lasten være. Kranen som lå på en lekter, var utsatt for vind og bølger. Selv små bølger fra båter som gikk forbi ga store utslag i kroken. Skade på utstyret som skulle heises om bord var ikke akseptabelt, heller ikke skader på folk hvis noe falt ned. Kranen måtte derfor brukes forsiktig. Når gliden var kommet helt opp, monterte Aker egne tårnkraner på toppen av skaftene.[REMOVE]Fotnote: Intervju med Svein Jørpeland, av Trude Meland Norsk Oljemuseum.
Matthew Hall Engineering og vektproblemene
Statfjord A er beskrevet som prosjektet som ble til underveis. Det ligger mye sant i det. Prosjektet var beryktet for arbeid som ble utført i feil rekkefølge, om tegninger som ble laget etter at arbeidet var gjort, såkalte DAB-tegninger – Drawn as Built.
Ingeniørselskapet Matthew Hall Engineering (MHE) i London var ansvarlig for tegningsarbeidet, prosjektering, ingeniørarbeid og design, innkjøp og byggeoppfølging av utrustningen av Statfjord A. Kontrakten mellom Mobil og MHE ble inngått i november 1974, altså en måned etter at arbeidet med betongunderstellet var satt i gang.
Planen var at det skulle bygges et betongunderstell med tre skaft og et enkelt dekk med prosessutstyr etter modulprinsippet, som et byggesett. Man skulle ikke gjenta løsningen med et integrert dekk som på Beryl A.[REMOVE]Fotnote: Moe, J. (1980). Kostnadsanalysen norsk kontinentalsokkel : Rapport fra styringsgruppen oppnevnt ved kongelig resolusjon av 16. mars 1979 : Rapporten avgitt til Olje- og energidepartementet 29. april 1980 : 1 : Sammenfatning av utviklingen, vurderinger og anbefalinger (Vol. 1). Oslo: [Olje- og energidepartementet]: 178. Men forutsetningene endret seg og Statfjord A skulle komme til å bli mye mer komplisert.
Særlig to forhold ble vesentlig endret i løpet av første byggeperiode. Da byggingen av plattformen startet var bare tre letebrønner boret på Statfjordfeltet. De viste alle tre at dette kunne være et stort felt, men hver ny brønn som ble boret avslørte at feltet var større enn antatt – mye større.[REMOVE]Fotnote: Lavik, H., Berge, L., & Statfjord-gruppen. (1997). Statfjord : Nordsjøens største oljefelt. Stavanger: Statfjord-gruppen: 27.
Det krevde større prosesskapasitet, og det ble besluttet at det var nødvendig med to parallelle prosesslinjer. Beslutningen om å doble produksjonskapasiteten fra 150 000 fat pr dag til 300 000 var svært viktig og har i ettertid vist seg å være riktig, den har kanskje mer enn noe annet bidratt til å gjøre Statfjord A til den pengemaskinen den har vært og fremdeles er. Det var selvfølgelig en dramatisk beslutning for prosjektet, og innebar at mye arbeid måtte starte forfra igjen.
Da produksjonskapasiteten ble doblet innebar det en dobling av alle gassystemer, kjølevann, ballastvann, kontrollsystemer, eksportsystemer for olje og gass og så videre. Omtrent alt på plattformen ble berørt og dette hadde svært stor betydning for vekten strukturene skulle bære.
Både utstyr og moduler måtte endres og den samlede vektbelastningen på dekket økte betraktelig. Med høyere vekt på dekket, økte belastningen på skaftene og ekstra bærebjelker og grovere godsdimensjoner måtte settes inn. Beslutningen om dobbelt prosessutstyr ble tatt etter at condeepen var ankret opp ute i fjorden og utrustningen var godt i gang. Nye tegninger måtte produseres og arbeid som var gjort, måtte gjøres om igjen.
Det andre som skjedde var at Akergruppen som hadde fått kontrakt på bygging av dekket, fikk gjennomslag hos Mobil for å bygge et mer integrert dekk, ikke et rent modulbasert som på Beryl A. Det ble bestemt at to tredjedeler av modulene skulle integreres. Aker fikk dermed en betydelig større del av leveransene til Statfjord A enn først planlagt, og Matthew Hall måtte lage nye tegninger også for dekket. Tegningene kom sent, og da de endelig kom, var de ofte for lite detaljerte. Det var konseptuelle tegninger og ikke detaljerte bygge-tegninger.[REMOVE]Fotnote: Intervju med Einar Jensen 2. oktober 2008, av Trude Meland Norsk Oljemuseum.
Skulle en holde fremdriftsplanen måtte mange aktiviteter utføres parallelt, en jobbet kontinuerlig med å forbedre reservoarsimuleringene, prosessoptimalisering, produksjon av byggetegninger og bygging. Tilgjengelige datasystemer for design og analyser av strukturer var i 1974/75 svært begrenset. Det tok tid å utføre kompliserte beregninger, ofte med stor mangel på designkoder, regelverk og spesifikasjoner. Det ble gjort best mulige antakelser og benyttet de koder som var tilgjengelige nasjonalt og internasjonalt.
NC var i gang med gliden for betongunderstellet da beslutningen om dobling av produksjonskapasiteten ble tatt. Arbeidet gikk fort og en trengte umiddelbart tegninger på utstyret som skulle inn i skaftene etterhvert som gliden gikk. Mye av utstyret skulle prefabrikkeres slik at det enkelt kunne løftes inn.
AOC var ansvarlig for utrustningen i betongstrukturen, men kunne ikke gjøre ferdig dimensjoneringen av systemene i utstyrsskaftet, som i hovedsak var støttesystemer for produksjon, før endelige detaljer om produksjonsanlegget på hoveddekket ble besluttet. Det ble derfor et kappløp med tiden å fremskaffe informasjon. Det var en svært krevende situasjon og mange kompromisser. Beslutninger måtte tas på grunnlag av den informasjonen som til enhver tid var tilgjengelig.[REMOVE]Fotnote: Intervju med Einar Jensen 2. oktober 2008, av Trude Meland Norsk Oljemuseum.
Matthew Hall brukte mye «draftsmen», eller tegnere i stedet for ingeniører, og sendte ofte fra seg skisser og ikke ferdige ingeniørtegninger. Arbeidet viste seg å være for komplisert for dem og de kom for sent i gang. Da deler av utstyret i skaftene skulle bygges hadde de ennå ikke fastslått vekten på dekkene og utstyret som skulle på plattformen. Det ble gjort en sannsynlighetsberegning som i etterkant viste seg å være feil. Dekkene ble mye tyngre og støttene måtte forsterkes. Engineering og tegningsarbeid lå hele tiden i etterkant, og førte til mye improvisering fra ingeniørene i Aker.
En av dem som var med på utformingen av utrustning i condeepen var Einar Jensen. Han kom til prosjektet i 1975 som nyutdannet ingeniør, ansatt i Aker Offshore Contracting. Hans første jobb var å lage detaljtegninger for rørinstallasjonene i lagercellene.
«Når vi begynte på designet i utstyrsskaftet, hadde vi en del konseptuelle tegninger [fra Matthew Hall] og vi visste vi måtte ha inn utstyr. Men vi hadde ingen detaljer på dette utstyret, vi visste blant annet ikke hva det veide. Hvor tung var en pumpe, en motor, et rør eller en ventil? Og vi var under tidspress. Vi måtte begynne å tegne fundamenter og tegnet dekket nedi skaftet for å få det ferdig og for å få kjøpt inn stål og ting som var prefabrikkert og så videre. Så måtte vi bare jobbe ut fra de beste antakelsene vi hadde. Og mange ganger tok vi feil. Det førte til at vi måtte gjøre modifikasjoner, gjøre endringer allerede mens plattformen lå her inne i Gandsfjorden. Det måtte legges inn veldig store forsterkninger på en del dekk i utstyrsskaftet.»[REMOVE]Fotnote: Intervju med Einar Jensen 2. oktober 2008, av Trude Meland Norsk Oljemuseum.
En kan nok si at mange av tegningene av dekkene i utstyrsskaftet ble tegnet ut i fra når en måtte ha tegninger for å kunne montere utstyret når NC var klar med gliden, og ikke når en var klar med detaljer av utstyret som skulle inn. Dette førte til at endringer/forsterkninger måtte gjøres etterhvert som endelig design av systemene ble ferdig.
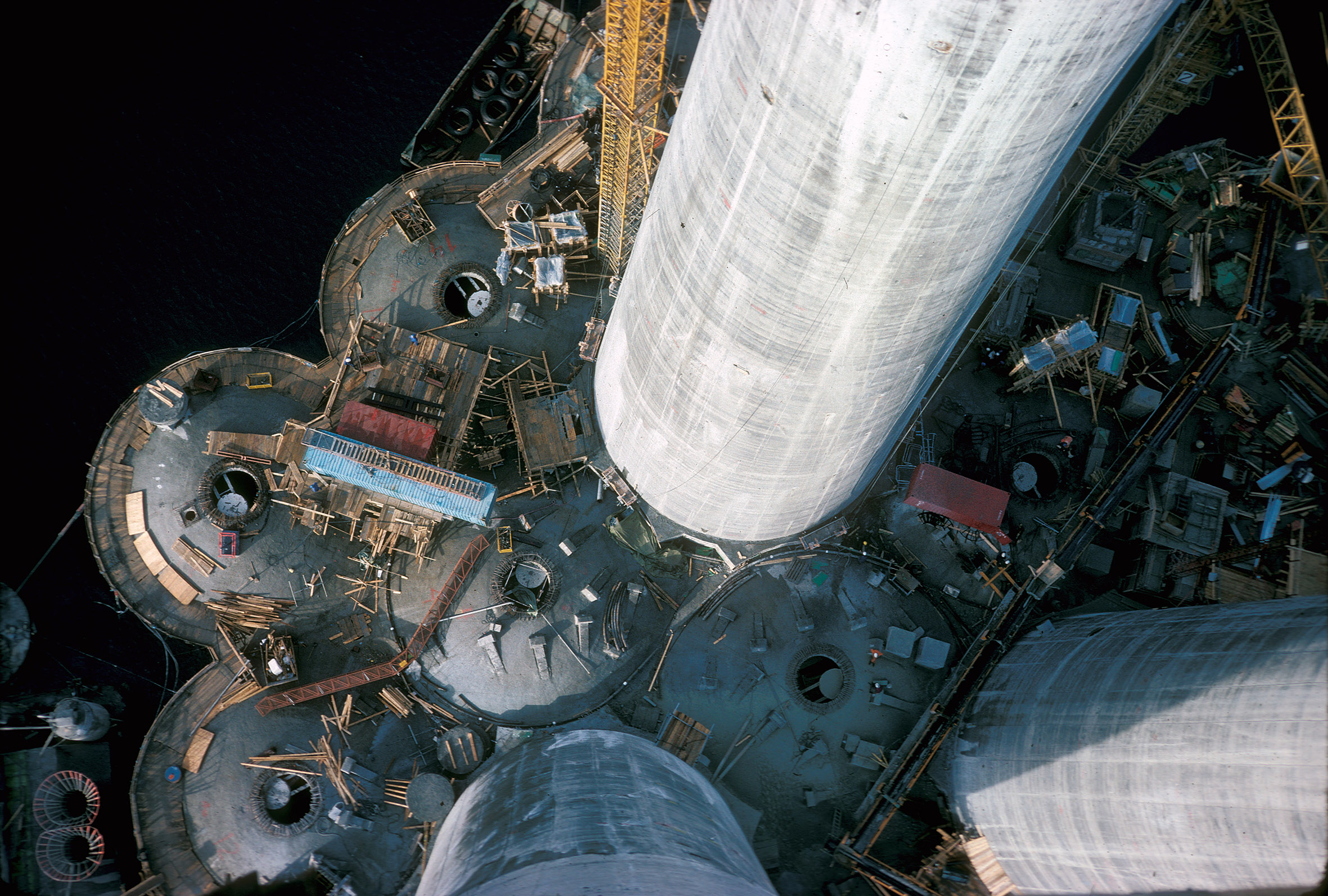
Ingeniøravdelingen hos MHE, Aker Engineering og AOC ble bemannet så sterkt en kunne, men det var likevel en umulig oppgave å fremskaffe tegninger slik en optimalt kunne ønske med tanke på byggearbeidet som pågikk. Mange av ingeniørene, kanskje de fleste, som deltok i designarbeidet hadde på dette tidspunktet aldri vært på, eller sett en produksjonsplattform. Det gjorde det selvfølgelig svært krevende for de som var senioringeniører og hadde en del erfaring. At det ble så mange endringer og mangel på informasjon underveis var selvfølgelig en frustrerende prosess for mange, og uforståelig for de som ikke kjente sammenhengen og bakgrunnen.
Flere feilberegninger ble gjort. Svein Jørpeland som var construction manager for Aker under utrustningen av Statfjord A, husker flere eksempler: «Dekkene i serviceskaftet hadde ballastpumper, crudeoljepumper, tanker, kjølevannspumper og svære rørsystem. Da dekkene ble tegnet og konstruert var det ikke tatt høyde for vannvekten i rørene. Det var jo ikke luft som skulle gå i rørene, det var vann, olje og annen væske. Så her måtte vi til å forsterke. Alle dekkene som skulle monteres inne i skaftet var prefabrikkert hos Aker Verdal, såkalte sandwich-plater. Vi installerte dem etter som gliden gikk.
Skaftet var smalere på toppen enn på bunnen så det var forskjellig diameter på de forskjellige dekkene Det betydde at vi måtte ha de rette dekkene til rett tid for ikke å stoppe gliden. Det gikk greit. Problemene startet etter hvert som vi hadde installert dekkene og begynte å installere utstyret. Da kom det fram at styrkeberegningen i dekkene ikke hadde tatt høyde for vannvekten. Opp til fem ganger måtte vi inn og forsterke dekkene. Når du kommer ned i utstyrsskaftet på Statfjord A, ser du derfor fem forsterkninger under hovedbjelken. Dette var tidskrevende arbeid, mye sveising. Alt var ferdig malt, så all malingen måtte slipes vekk, for sporet der stålet kom opp måtte være rent. Så var det til å sveise opp igjen, sandblåse og male på nytt. Og ved sandblåsing må alt dekkes til. Og så fem ganger!»[REMOVE]Fotnote: Intervju med Svein Jørpeland, av Trude Meland Norsk Oljemuseum.
Tid er alt
Ifølge Jensen var miljøet preget av kreativitet, hvor improvisasjon og det å finne nye løsninger ble verdsatt. Løsninger og tid betydde alt, kostnader var ikke et argument. Det var bare et spørsmål om når ting kunne leveres. Var det noe som manglet var det bare å ta noen telefoner rundt om i verden og se hvem som kunne levere raskest. «Jeg husker vi hadde tatt inn anbud til å lage noen ventilasjonskanaler i skaftet og jeg fikk en pris fra et firma på Østlandet. Her i Stavangerområdet kostet det kanskje tre ganger så mye, men de kunne levere mye raskere. Så det ble Stavangerområdet som fikk leveransen.»[REMOVE]Fotnote: Intervju med Einar Jensen 2. oktober 2008, av Trude Meland Norsk Oljemuseum.
Mobil og prosjektledelsen var svært fokusert på å holde fremdriftsplanen. Prosjektet omfattet til tider flere tusen personer, en rekke utstyr, båter og andre fasiliteter som var innleid. Dette representerte en høy timepris. I tillegg var man avhengig av «værvinduer» for å kunne gjennomføre værkritiske operasjoner. Og mer en noe, så var det et stort press fra eiere og myndigheter å kunne starte produksjonen som planlagt. Ekstrakostnader for å fremskaffe utstyr ble bagateller i denne sammenhengen. Å påføre prosjektet forsinkelser var ikke et alternativ.
En sluseventil som veide 3,5 – 4 tonn havnet i Australia istedenfor Gandsfjorden. Da var gode råd dyre. Ventilen var laget i California og skulle sendes til Stavanger, hvor ingen kunne finne den. Den ble sporet til Sydney, Australia. Det var en stor ventil, fire meter høy med en diameter på 48 tommer. For ikke å forsinke arbeidet mer enn nødvendig måtte Aker få tak i en ny. Svein Jørpeland tok ansvar: «Vi kunne ikke vente på den som lå i Australia. Jeg sa – få tak i en ny ventil og et nytt fly, og fly den direkte til Sola. Det lå en i LA vi kunne få, så jeg chartret en egen Boeing 707 fra Los Angeles, og den landet direkte på Sola. Så nå hadde Mobil to ventiler, en i Australia og en på Sola. Mobil mente jeg skulle ha diskutert med dem før jeg satt i gang, men jeg hadde ikke tid. Flyet landet på Sola og vi kom ut med lastebil, lastet ventilen rett om bord, kjørte direkte til Sandnes, på taubåt ut, og inn i skaftet med den. Alt var gjort innen 48 timer.»[REMOVE]Fotnote: Intervju med Einar Jensen 2. oktober 2008, av Trude Meland Norsk Oljemuseum.
Arbeidsplassen

Statfjord A var en spesiell arbeidsplass allerede mens den lå i Gandsfjorden. Etter slepet ut fra tørrdokken på Hinna måtte alle som arbeidet på betongkolossen fraktes til og fra arbeidsplassen med båt. Det gikk båt fra Hetlandskaien ved Hillevåg 25 minutter før skiftbytte. I tillegg gikk det mindre båter ut og inn hele døgnet.
Historien om Statfjord er historien om tilfeldigheter og om de som grep sjansen. En av dem var Alvilde Berge, kjent som Reder Tina. I et intervju med VG i 1981 fortalte hun hvordan hun ble skipsreder ved en tilfeldighet. Hun hadde vært på båttur utenfor Hinna med sin 28 fots cabincruiser da hun hadde sett en hel gjeng på Statfjordbetongen som vinket. Hun la turen bortom og det viste seg at det var arbeidere som var ferdig med skiftet sitt og mannskapsbåten som skulle ta dem til land var ødelagt.
Berge fylte opp båten og kjørte dem til land. Da sistemann var trygt på landjorden så båten ut som en svinesti og rekken var ødelagt. I tillegg ble hun skjelt ut av et verneombud for ikke å ha sertifikat for å frakte passasjerer. Dagen etter troppet hun opp hos Norwegian Contractors for å få erstatning for skadene. «Da kom mannen som hadde kjeftet på meg og spurte om jeg ville ha jobb. Jeg kunne begynne øyeblikkelig å kjøre folkene.» Det var begynnelsen for «Reder Tina», som etter hvert ble et begrep innen oljeindustrien. Navnet Tina kom av navnet på båten. I 1981 eide hun og kompanjongen syv båter med et mannskap på 25.[REMOVE]Fotnote: VG. (1981). 24. juli. Fikk kjeft, ble reder.
Hvem arbeidet på Statfjord A?
Arbeidet pågikk kontinuerlig etter fireskiftsordning. I desember 1975 hadde Norwegian Contractors 820 mann i arbeid. Av disse arbeidet rundt halvparten med Statfjord A, resten jobbet med Brent D som også var under støping. Yrkesgruppene som var representert på anlegget varierte stadig ut fra hvilke jobber som var prioritert. For de som arbeidet for NC med betongdelen var det forskalingssnekkere, jernbindere og støpere som var de tre største kategoriene. Disse tre gruppene arbeidet tett sammen. Jernbinderne bandt armeringsjernet, mens støperne fylte flytende betong i formene.
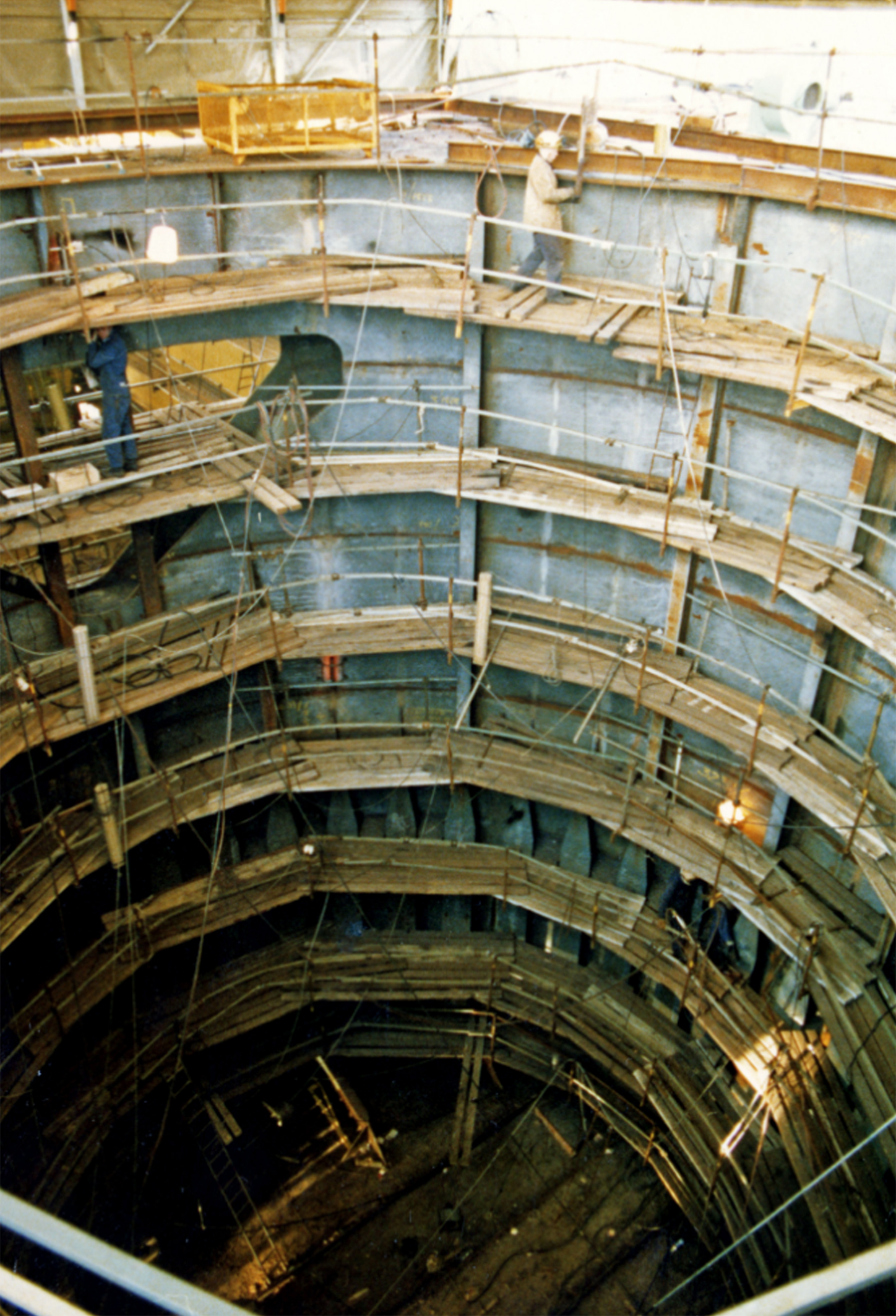
Snekkerne bygget stillaser, de sto for innstøping av spesielle fester i betongen og gjorde forefallende arbeid. I tillegg til de tre største, var det andre hjelpefunksjoner som transport av utstyr, kranførere, radiooperatører, elektrikere, blandemaskinkjørere, lagerarbeidere, flisegutter, glidekjørere, kokker og vaskehjelper. Heisføreren oppholdt seg i eller nær ved heisen hele tiden mens han var på jobb.
Støynivået var høyt og det var til tider kaldt og surt. Radiooperatøren satt i sambandssentralen, kalt tårnet, som var en kontorbrakke på konstruksjonen. Her styrte han walkie-talkier, VHF-radioen og flere telefonlinjer. Brakken fungerte også som varmestue og pauserom. Det var mest for formennene, men også annet mannskap kom innom, særlig på natten da sambandet var relativt rolig.[REMOVE]Fotnote: Stangeland, P. (1977). Condeep : En arbeidsplass i Stavanger (Vol. 1/77, Rapport (Rogalandsforskning : trykt utg.)). Stavanger: Rogalandsforskning.
Hos AOC var det rørsveisere, montører og elektrikere som dominerte, yrkesgrupper som en finner i verkstedsindustrien. Den største gruppen var sveisere. Det var mye rør som skulle sveises, men også dekkene inne i skaftene. I tillegg kom trapper, heiser og annet. Dette var for så vidt vanlig platearbeid, men monteringen var vanskelig på grunn av plassmangel og store høyder. Utluftingen var dårlig og akustikken litt for god.
Arbeidsmiljøet nede i skaftene var ikke det beste. Det lå stadig en tåke av sveisegass, gul eller blå alt etter som. Mange var plaget med hodepine, kvalme og bronkitt. Friskluftanlegget som blåste luft ned i bunnen av skaftene var lite effektivt.
Det var et tåket landskap med et virvar av rør, taljer, sveiseapparat og stillaser over alt. Lyskastere lyste opp enkelte steder og kompressorer og meislemaskiner lagte mye støy. Betongveggene og ståldekkene inne i skaftene forsterket all lyd.
Undersøkelser viser at få brukte øreklokker. Øreklokker ville ha stengt all lyd ute, og mange var redde de ikke ville høre hvis noe galt skulle skje. De som arbeidet nede i skaftene, måtte klatre opp og ned trapper tilsvarende en 20 etasjes blokk hver gang de skulle til arbeidsstedet. En skulle ikke ha høydeskrekk for å jobbe i Statfjord A-skaftene.[REMOVE]Fotnote: Stangeland, P. (1977). Condeep : En arbeidsplass i Stavanger (Vol. 1/77, Rapport (Rogalandsforskning : trykt utg.)). Stavanger: Rogalandsforskning: 130.
På plattformen var det bare menn som arbeidet. Av de 70 kvinnene som hadde sitt arbeid på anlegget, var 50 i anleggsleiren og 20 på losjiskipene, som kan sies at var en forlengelse av anleggsområdet.[REMOVE]Fotnote: Leira, A. (1978). Kvinner på en oljearbeidsplass : En undersøkelse ved Condeepanlegget i Stavanger (Vol. Nr 8-1978, Sosialdepartementets sammendragsserie (rapportsammendrag : trykt utg.)). Oslo: Sosialdepartementet: 30.
De aller fleste jobbet i servicevirksomhet med mat, servering, vask og renhold. Noen få skilte seg ut med mer spesialisert arbeid; sekretær, regnskap og sentralbord. Noen ganske få var også arbeidsledere som spisesalsjef, inspektør blant rengjøringspersonalet, kantineleder og så var det ei kokke – i storkjøkken var det vanlig at menn innehadde den stillingen. I tillegg var det to kvinnelige kranførere.[REMOVE]Fotnote: Leira, A. (1978). Kvinner på en oljearbeidsplass : En undersøkelse ved Condeepanlegget i Stavanger (Vol. Nr 8-1978, Sosialdepartementets sammendragsserie (rapportsammendrag : trykt utg.)). Oslo: Sosialdepartementet: 37. På det meste var 78 firma engasjert, men det finnes ingen liste over samtlige ansatte på anlegget på Hinna.
Miljø og fagforening
Ansettelsesforholdene på condeepene var usikre. En dag var det ikke nok arbeid, og arbeiderne kunne bli sagt opp med åtte timers varsel. De fleste som arbeidet for Aker var fagorganiserte, men for mange av de små firmaene var det vanskelig å få til en ordentlig tillitsmannsordning. Arbeidsstokken ble stadig skiftet ut, de ansatte arbeidet forskjellige skift og på forskjellige deler av anlegget og hadde liten mulighet til å snakke sammen.[REMOVE]Fotnote: Stangeland, P. (1977). Condeep : En arbeidsplass i Stavanger (Vol. 1/77, Rapport (Rogalandsforskning : trykt utg.)). Stavanger: Rogalandsforskning: 91. Tillitsmennene i de større firmaene var ikke villig til å ta seg av de ansatte i mindre selskapers saker.
Det var mange arbeidere fra Finland og finnene var kjent for å være meget dyktige og effektive sveiser. Ryktet sier at når de kom til skiftet sitt, hadde de matpakken med seg, gikk ned i cellene og kom ikke opp igjen før skiftet var over. Jørpeland kan ikke få rost dem nok: «Uten finnene hadde ikke prosjektet gått like bra. Finnene sveiset feilfritt. En finsk sveiser hadde tre års utdannelse og var metallurg. I Norge var utdannelsen på tre måneder. Men selvfølgelig, finner er finner og etter en arbeidsperiode tok de seg gjerne en fest. Og da var de vekk i to dager, før de kom tilbake for fullt igjen.»[REMOVE]Fotnote: Intervju med Svein Jørpeland, av Trude Meland Norsk Oljemuseum. Mellom 50 og 80 finner arbeidet på Statfjord som sveisere og rørleggere.
Ting som forsvant
Et hvert industrianlegg er kjent med at ting forsvinner og Statfjord A var intet unntak. Folk stjal de rareste ting. Alt som var mulig og umulig å ta med seg, ble tatt. «En nyttårshelg forsvant en standby radiosentral fra GBS-en (betongunderstellet). Et eget vaktselskap skulle passe på, men ting forsvant like fremt. Kveiler på 4000 meter kobberrør som skulle brukes til hydraulikken i skaftene forsvant. Det ble bestilt nye med lovnad om at de skulle følges hele veien fra leverandør til Aker sitt lager.» Men selv det så ikke ut til å hjelpe.
«Jeg kom opp i Haugesundsgaten og utenfor skraphandler Bøen sto en lastebil med nye kobberrør kveilet på lasteplanet. Det var kobberkveilene til Statfjordunderstellet som skulle vært kjørt rett fra leverandør til Aker under overvåkning. De var kjørt rett til skarphandleren. Prisen på kobber var høy.»[REMOVE]Fotnote: Intervju med Svein Jørpeland, av Trude Meland Norsk Oljemuseum.
Jørpeland ringte politiet som fant både første og andre leveranse. Så i stedet for 4000 meter, hadde de nå 8000 meter.
Også stillasplanker var populært tyvegods. Planken som ble brukt til gulv i stillasene var kvistfri plank som kom i bunker på flere hundre kvadrat. Det som oftest forsvant var verktøy. Hvert firma hadde sitt eget verktøy i egne konteinere og alle som arbeidet måtte signere ut for det verktøyet de trengte. Men svinnet var likevel stort.
Ali Installation A/S
Et av selskapene som hadde en stor kontrakt som underleverandør til AOC var det statseide svenske selskapet Asken Industri AB sitt norske datterselskap, Ali Installation A/S.[REMOVE]Fotnote: Nerheim, Jøssang, Utne, Dahlberg, Jøssang, Lars Gaute, Utne, Bjørn Saxe, . . . Kværner Rosenberg. (1995). I vekst og forandring : Rosenberg verft 100 år 1896-1996. Stavanger: Kværner Rosenberg: 387. Ali Installation forble datterselskap av svenske Asken Industri AB til november 1980 da det ble Ali kjøpt opp av Moss Rosenberg Verft A/S og skiftet navn til MRV Installasjon. I 1985 skiftet det igjen navn til Kværner installasjon A/S. Ali hadde tidligere utført utrustningen av Brent B, men selskapet var en utfordring. Fremdriften på utrustningen var allerede på etterskudd og arbeidet gikk 24 timer i døgnet hver dag hele uken. En lørdag morgen i 1975 kom ikke svenskene og finnene fra Ali på jobb. Av en arbeidsstyrke på 420 mann var halvparten gått ut i streik. De mente selv at de var lovet å ikke måtte betale skatt av lønnen sin.[REMOVE]Fotnote: Stavanger Aftenblad. (1975). 7. mars. Skattestreik på Condeep.
Ali var heller ikke fornøyd med at Aker hadde kontrakten på utrustningen av understellet, mens de selv bare var underkontraktør og ifølge Jørpeland forsøkte selskapet derfor å boikotte Aker. Problemet var at Aker og framdriften var avhengig av Ali og den kompetansen svenskene og finnene hadde. Nordmenn hadde lite erfaring med den kvaliteten som krevdes for en offshoreinstallasjon.
Svenskene og finnene hadde arbeidet på kjernekraftverkene og hadde erfaring med den kvaliteten som ble forlangt på Statfjord.[REMOVE]Fotnote: Intervju med Svein Jørpeland, av Trude Meland Norsk Oljemuseum. Men Jørpeland var ikke en leder som ga etter. Han fant en annerledes løsning: «Da jeg kom på jobb ringte jeg en venn av meg i Portugal som driver et stort firma og spurte om han kunne skaffe 400 mann pronto. Jeg ga beskjed til Ali ’off the platform – dere har fire timer på å rydde verktøy og alt annet fra plattformen, for her skal det inn portugisere. Jeg har en jumbojet stående klar i Lisboa, så det er bare å ta en siste telefon.’ Det ble huskestue av det. Jeg sa at jeg ikke godtok oppførselen til Ali, sabotasje rett igjennom, nå var jeg lei. Hvis de ikke krøp til korset, var klokken fire siste timen om bord på plattformen. De krøp selvfølgelig til korset, for de hadde egentlig gunstige betingelser. Jeg ringte Portugal igjen og sa at vi avblåser.»[REMOVE]Fotnote: Intervju med Svein Jørpeland, av Trude Meland Norsk Oljemuseum.
Svenskene forble underentreprenører, men etter denne episoden begynte Aker for alvor å bygge opp en norsk arbeidsstyrke og svenskene ble etter hvert faset ut. En del av de finske sveiserne fikk jobb direkte i Aker.
Jørpeland godtok ikke unnasluntrere og visste at ledere som ikke tålte presset i jobben sin var en fare for prosjektet. Det skulle monteres en riser, et rør på om lag 80 meter formet som en S, som skulle gå utenpå cellene før den gikk inn i det ene skaftet. Røret var prefabrikkert i Tananger og skulle fraktes til Gandsfjorden på kranskipet Uglen. Vekten var nøye beregnet. Den skulle henge i kranen under seilaset, for så å legges ned på en lekter i nærheten av plattformen.
Selve tauingen fra Tananger til Gandsfjorden gikk bra og Aker sine folk fulgte hele transporten. Men lederen for operasjonen stilte ikke. Jørpeland forteller: «Jeg ble oppringt klokken halv fire om morgenen og fortalt at Aker sine folk ikke var i Gandsfjorden for å ta imot. Jeg hev meg i bilen og kom meg av gårde. Da jeg kom fram, så jeg at av ti stropper som holdt riseren hadde fem slitt seg. Jeg fikk mitt livs største sjokk. Så fort og forsiktig som mulig ble riseren rigget om og senket ned dit den skulle festes. Det gikk bra.»[REMOVE]Fotnote: Intervju med Svein Jørpeland, av Trude Meland Norsk Oljemuseum. Men hva skjedde med lederen i Aker som hadde forlatt stedet? Jørpeland var ikke nådig. «Jeg sa til ham at du skal få en enveisbillett med tog så du får tid til å sitte og tenke på hva har du gjorde feil. Jeg sa det humørfylt.» Han ble degradert men fikk bli for AOC trengte folk.[REMOVE]Fotnote: Intervju med Svein Jørpeland, av Trude Meland Norsk Oljemuseum.
En annen ting som ikke ble akseptert var illojalitet. Det fikk en gjeng briter erfare. «Det var viktig at vi ikke hadde åpne dører i Aker, slik at Mobil ikke fikk vite alt om våre problemer. Men på nattklubben Cobra møttes Aker og Mobil sine folk. Mobil spanderte villig gratis øl til disse engelskmennene i Aker som snart begynte å fortelle om våre problemer. Så da vi gikk i byggemøter og prosjektmøter med Mobil, så visste de alt i detalj. Dette måtte jeg få satt en stopper for. Jeg bestilte ti flybilletter, gikk til engelskmennene, pekte på dem og sa: ‘Here is a one way ticket’. Jeg ga ut de ti billettene helt vilkårlig og sa: If you continue to leak to Mobil, I will get back next week with another twenty tickets.» Det ble slutt på lekkasjen.
Sikkerhet!

Sikkerhetsregimer har endret seg gjennomårene. Under byggingen og utrustningen av Statfjord var tanken at folk måtte ta vare på sin egen sikkerhet. Det var egne sikkerhetsfolk som overvåket sikkerheten og det var brannvakter som gikk rundt og sjekket at brannapparater og hjelpeutstyr var på plass i de forskjellige etasjene i plattformen. På stillasene var det strengt forbud mot å legge igjen verktøy eller avkapp eller andre ting som kunne falle ned.
Den enkelte var selv ansvarlig for å overholde forbudet. Hvis en sveiser satt oppe på skaftet, det var hundre meter ned, og knipset enden på sveiseelektroden ned når han skulle skifte elektrode, kunne enden gå gjennom to tommers plank. På innganger til skaftene ble det derfor bygd overbygg med stålplater som elektrodene ikke kunne gå igjennom. Oppå stålet ble det lagt treplanker, et nytt lag med stål og så et siste lag med tre. Når elektrodeenden falt ned satte den seg fast i treet, men gikk ikke gjennom. Hadde enden truffet rett på en stålplate, hadde den sklidd og flydd videre. Treplankene på toppen kunne se ut som rene spikermatter.
I skaftene var det såkalte droppsoner hvor bårer og lignende kunne heise opp hvis det skulle skje en ulykke i bunnen på skaftet. Båren kunne heises opp ved hjelp av kranen. Det ble heist ned en basket som var stor nok til en båre.
Ulykker
Det skjedde ulykker under arbeidet med betongunderstellet. Den mest alvorlige var da en 20 år gammel arbeider fikk en spade i hode og senere døde av skadene. Ulykken skjedde 25. juli 1976, bare dager før understellet skulle slepes til Stord. Arbeidet med byggingen av plattformen var ferdig og det foregikk opprydding. Ungdommer hadde fått i feriejobb å rydde og klargjøre plattformen. De var delt opp i forskjellige lag hvor noen skulle plukke opp rester av materialer etter stillaser og rør og rørdeler og legge dem i tønner. Så kom nye lag og kostet dekkene og – ved hjelp av spade – tok opp restene i tønner.
Fra toppen av skaftet og ned til 80-metersdekket var det et dropphull for vertikal transport ned i skaftet. Her ble tønnene heist opp ved hjelp av kranen, tømt i konteinere som siden ble fraktet til land. På toppen av skaftet sto en med radio og dirigerte kranen med tønnene nedover det første stykket, hvor en annen overtok og dirigerte kranen dit den skulle. Rundt dropphullene på de forskjellige dekkene var det et gjerde og en 15 – 20 cm høy trelist som skulle hindre at gjenstander ble skjøvet fra dekket og ut i åpningen.
Det hadde skjedd ett uhell tidligere hvor en tom tønne ble slått ned i dropphullet da kranen kom borti den med en full tønne. Deler av gjerdet ble ødelagt og hullet sikret med et tau. Ingen ble den gangen skadet. Den omkomne var signalmann for kranføreren og sto under dropphullet på 80-meters- dekket og slappet av da ulykken skjedde. Rundt dropphullet på 128-metersdekket var en del av trelisten ødelagt, og på dette dekket drev et arbeidslag og kostet. Feltet på 80-metersdekket rett under dropphullet var ikke avmerket eller avsperret slik at det vanskeliggjorde å oppholde seg der.
Hva som skjedde ble aldri helt klart, men det er sikkert at en spade kom gjennom dropphullet i skaftet og traff den forulykkede i hodet. Spaden gikk igjennom hjelmen. Den skadde ble lagt på båre og tatt opp av skaftet ved hjelp av kran og redningskurv. Det var vanskelig å få redningskurven ned gjennom skaftet og det måtte stå folk å støtte i den nedover. Politiet kunne ikke bringe på det rene hvilket dekk spaden kom fra eller hvordan den kan ha kommet til å falle ned. Ingen ble lastet for ulykken.[REMOVE]Fotnote: Stavanger Politikammers arkiv. Justissaker. Sak nr. 3243/76.
Dykkerulykke
Det var mye dykkerarbeid knyttet til bygging av Statfjord A-understellet – oppmålinger, rørinspeksjoner, rørplugging, montering av anoder på skjørtekanten og testing av jetdyser som var plassert nede på utsiden av ballasttankene. Ballasttankene var til å sprute vann under høyt trykk ned mot bunnen når plattformen ble plassert på feltet slik at bunnslammet ble virvlet opp og plattformen kunne settes sikkert ned. Det var dykkerne som måtte ned for å finne gjenglemte ting og utstyr som var mistet i sjøen.
Før utslep måtte alt hjelpeutstyr som kranfundamentene under vann, fjernes og ankerkjettingene kuttes. Høsten 1975 foregikk det dykk inne i stjernecellene. De var åpne med tilgang fra toppen. Noen bolter på 25 meters dyp skulle brennes av for å fjerne en flens. Men flensen løsnet ikke og dykkeren hadde behov for verktøy til å brekke den løs med. Han gikk til overflaten for å få verktøyet og hang i brennerkabelen mens han ventet. Oppe ble et spett festet til brennerkabelen i en renneløkke.
Det var ingen kommunikasjon mellom dykkeren og lederen, så dykkeren hadde ingen mulighet til å vite hvordan verktøyet skulle sendes ned. Spettet hadde fritt fall langs brennerkabelen og traff dykkeren i brystet og stakk ut igjen i ryggen. Dykkeren overlevde, men fikk dykkerforbud i all framtid på grunn av skade på lunger og ble etter hvert uføretrygdet. Dykkerleder ble gjort ansvarlig for ulykken og pålagt en bot.[REMOVE]Fotnote: Gjerde, K., Ryggvik, H., & Meland, T. (2009). Nordsjødykkerne. Stavanger: Wigestrand: 156.
Statoil informasjonsansvarligPlaner for fase I