Building the Statfjord A GBS

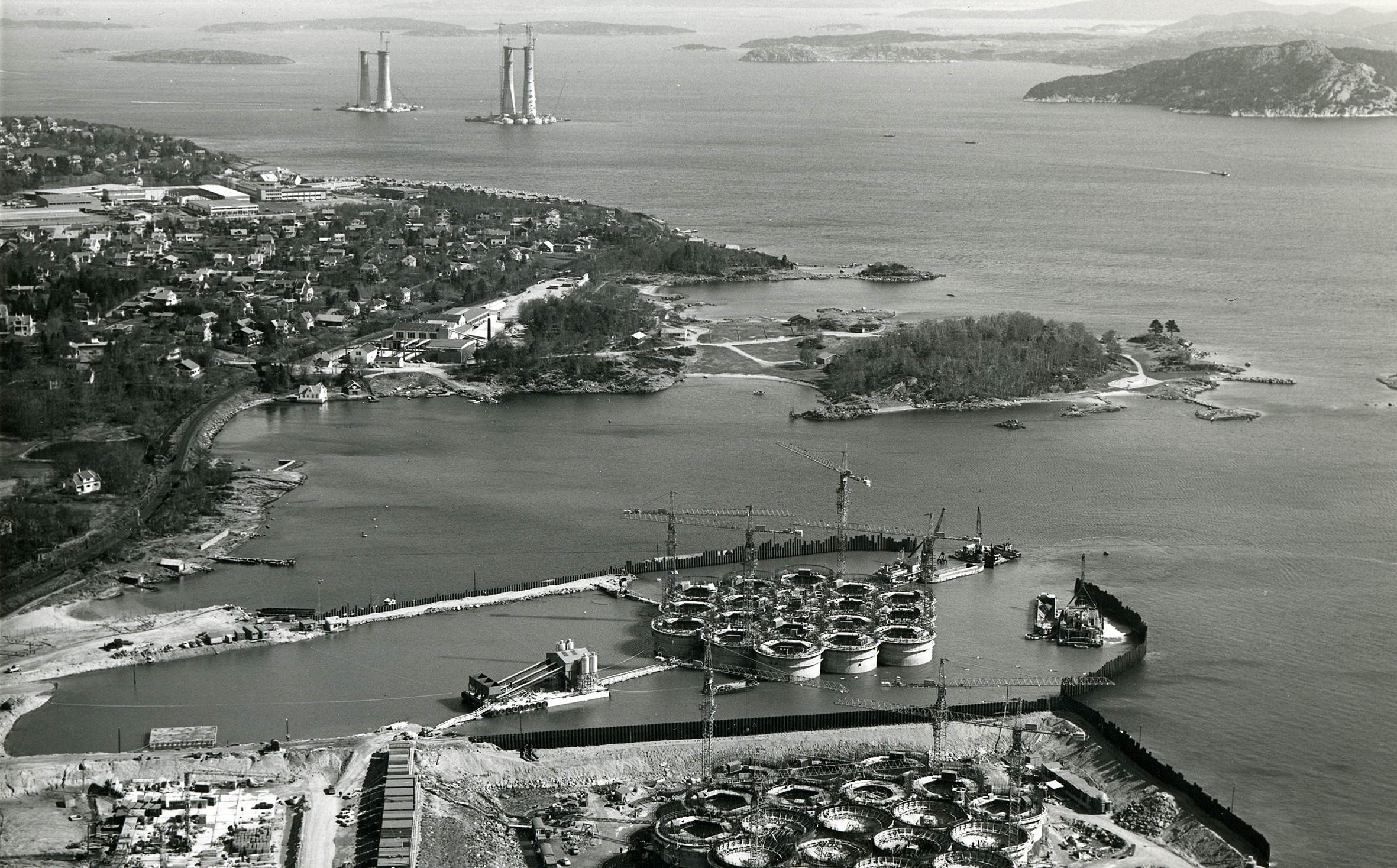
Mobil’s Beryl A and Shell/Esso’s Brent B units – both destined for the UK North Sea – were moored in deep water out in the fjord during the autumn of 1974, while work was under way on the base sections for Statfjord A and Brent D in the Hinnavågen dry dock.
All four were built to the Norwegian Concrete Deepwater Structure (Condeep) design. Other well-known designs for concrete GBSs – so called because they stand on the seabed under their own weight – included the Andoc, developed and built by McAlpine at Ardyne Point in Scotland, the Sea Tank from C G Doris (the Ekofisk tank in the Norwegian North Sea is an example) and Arup’s Concrete Gravity Substructure (CGS).
The Condeep solution had been developed by Høyer-Ellefsen. On 13 July 1973, this company, fellow Norwegian construction company Ing F Selmer A/S and the Aker group received a contract for the very first of these structures. Aker was to handle mechanical outfitting of the shafts which supported the topside. This order was placed by Britain’s Mobil North Sea Limited for use on the Beryl field.
Building this unit proved a big challenge, so Høyer-Ellefsen and Selmer joined forces with a third construction company, Ingeniør Thor Furuholmen A/S, to carry out the work.[REMOVE]Fotnote: Steen, &., & Norwegian Contractors. (1993). På dypt vann : Norwegian Contractors 1973-1993. Oslo: [Norwegian Contractors]: 16. They formed a joint venture called Norwegian Contractors (NC).
Mobil had secured tenders from seven different companies for Beryl A. These proposed various steel and concrete solutions for delivery in 1975. After careful consideration of all the bids, the US company opted for the Condeep.
This came out well in price terms and the NC group had experience with concrete construction from building the Ekofisk tank a few years earlier. In addition, the Condeep offered a foundation solution which suited the bottom conditions on Beryl. These arguments outweighed the fact that the Condeep represented a completely new application of technology. It was a pioneer project.[REMOVE]Fotnote: Steen, &., & Norwegian Contractors. (1993). På dypt vann : Norwegian Contractors 1973-1993. Oslo: [Norwegian Contractors].
The choice of a Condeep for Statfjord A primarily reflected the fact that Mobil had secured an option for a second of these structures, which it originally intended to use for Beryl B. When that proved unnecessary, the British arm of Mobil offered the option to its Norwegian affiliate and the Statfjord licence. Mobil appreciated that Statfjord was to be developed as quickly as possible.[REMOVE]Fotnote: Moe, J. (1980). Kostnadsanalysen norsk kontinentalsokkel : Rapport fra styringsgruppen oppnevnt ved kongelig resolusjon av 16. mars 1979 : Rapporten avgitt til Olje- og energidepartementet 29. april 1980 : 1 : Sammenfatning av utviklingen, vurderinger og anbefalinger (Vol. 1). Oslo: [Olje- og energidepartementet]: 141.
As on all fields, however, the reservoir primarily determines the appropriate production installation – and Statfjord was no exception. Reservoir properties, the design of production and injection wells, pressure and temperature conditions and oil/gas composition must be taken into account. An export solution for the field also needs to be decided.
When decisions on building Statfjord A were taken in 1974-75, information on these factors was extremely limited., More data were acquired on the reservoir as appraisal drilling continued. These details in turn provided the basis for analyses of rock formations, production properties, the oil/gas ratio and so forth – and thereby the basis for designing production systems on the platform.
The Beryl B option available to Mobil offered an opportunity to get started quickly, and the Statfjord licensees resolved to seize this chance. They were aware that the project was launched with very limited reservoir information. Substantial design changes had to be expected compared with Beryl A.
Those who took the decision also had limited experience of constructing such a large and complex installation as Statfjord A, and did not fully foresee the consequences of the limited preliminary design work.[REMOVE]Fotnote: Intervju med Einar Jensen 2. oktober 2008, av Trude Meland Norsk Oljemuseum.
Slipforming
NC had secured a lease from the City of Stavanger for the use of Hinnavågen bay and a mooring site in the Gands Fjord. It filled in the bay to create a dry dock and made provision for warehousing and a work camp in the adjacent fields.[5]
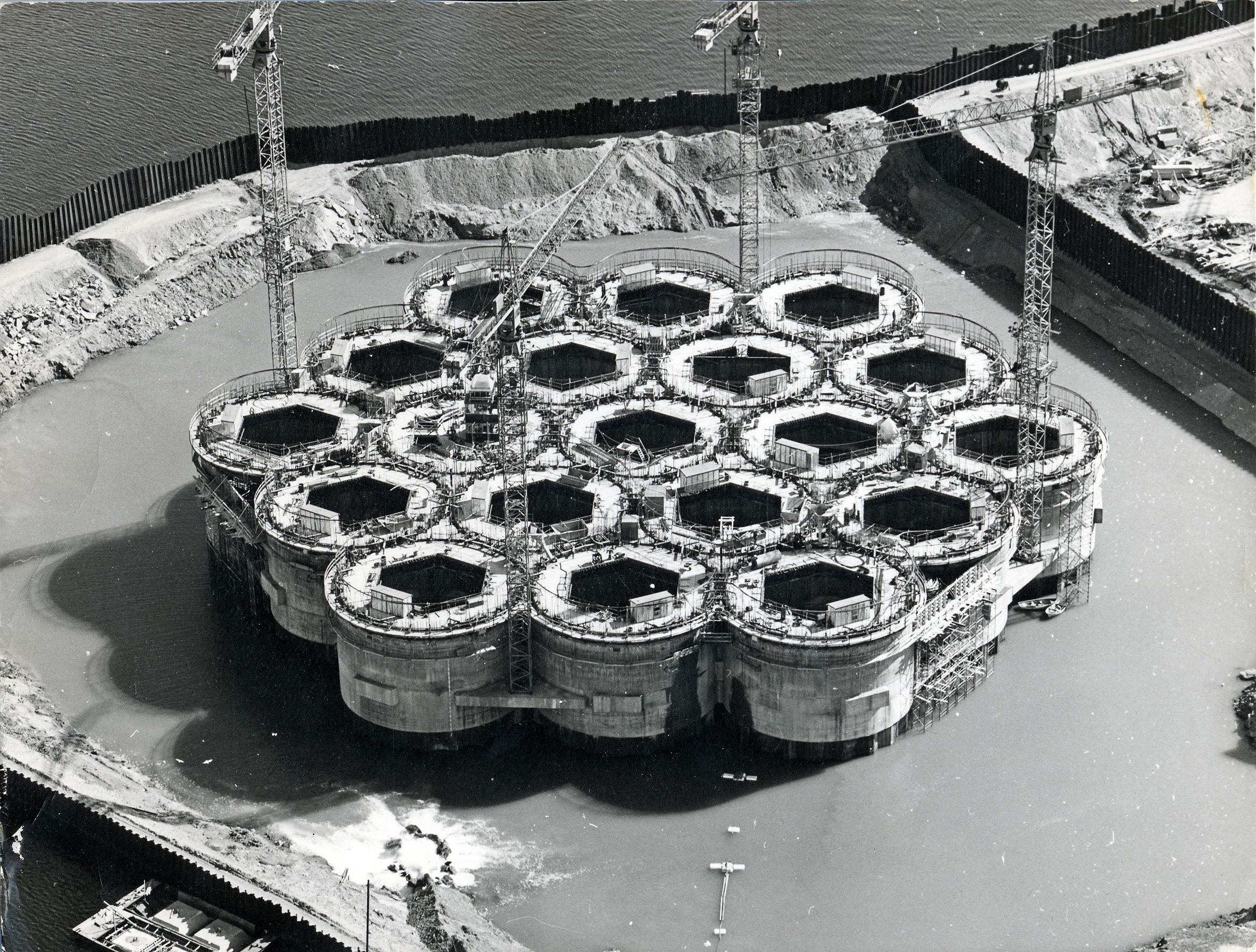
The base section of the GBS was cast in this dry dock. The first step was to install a “steel skirt” under each cell, which was intended to dig into the seabed and help ensure the platform’s stability.[REMOVE]Fotnote: Norsk Oljerevy. (1977). Nr. 3. februar. 17-18. Statfjord “A” – den første i sitt slag etter nytt regelverk.
Nineteen concrete cells were then cast on top of this skirt to a height of 14 metres. Once that work had been completed, the dock was filled with water so that the structure floated and could be towed out and moored in the fjord roughly a kilometre from land.
From that point on, all equipment and personnel had to be ferried to and from land by boat. Fifteen of the cells were due to serve as storage tanks for crude oil, one would store diesel oil to drive machinery on the platform, and the last three would be extended upwards as shafts to support the topside.
Casting the cells in the Hinnavågen dock proceeded without problems or delays, and the base structure was towed out into the fjord in May 1975 for continued slipforming of cells and shafts.
Slipforming is a technique based on the use of moving formwork, which is jacked up the concrete columns as they are built.[REMOVE]Fotnote: Stavanger Aftenblad (1975). 8. februar. Gliden på CONDEEP. The 19 cells were first slipformed to their full height of 70 metres. The caisson was ballasted down in the sea as the walls rose at a rate of 15 millimetres every seven minutes – equivalent to three metres per day.[REMOVE]Fotnote: Stavanger Aftenblad (1975). 8. februar. Gliden på CONDEEP.
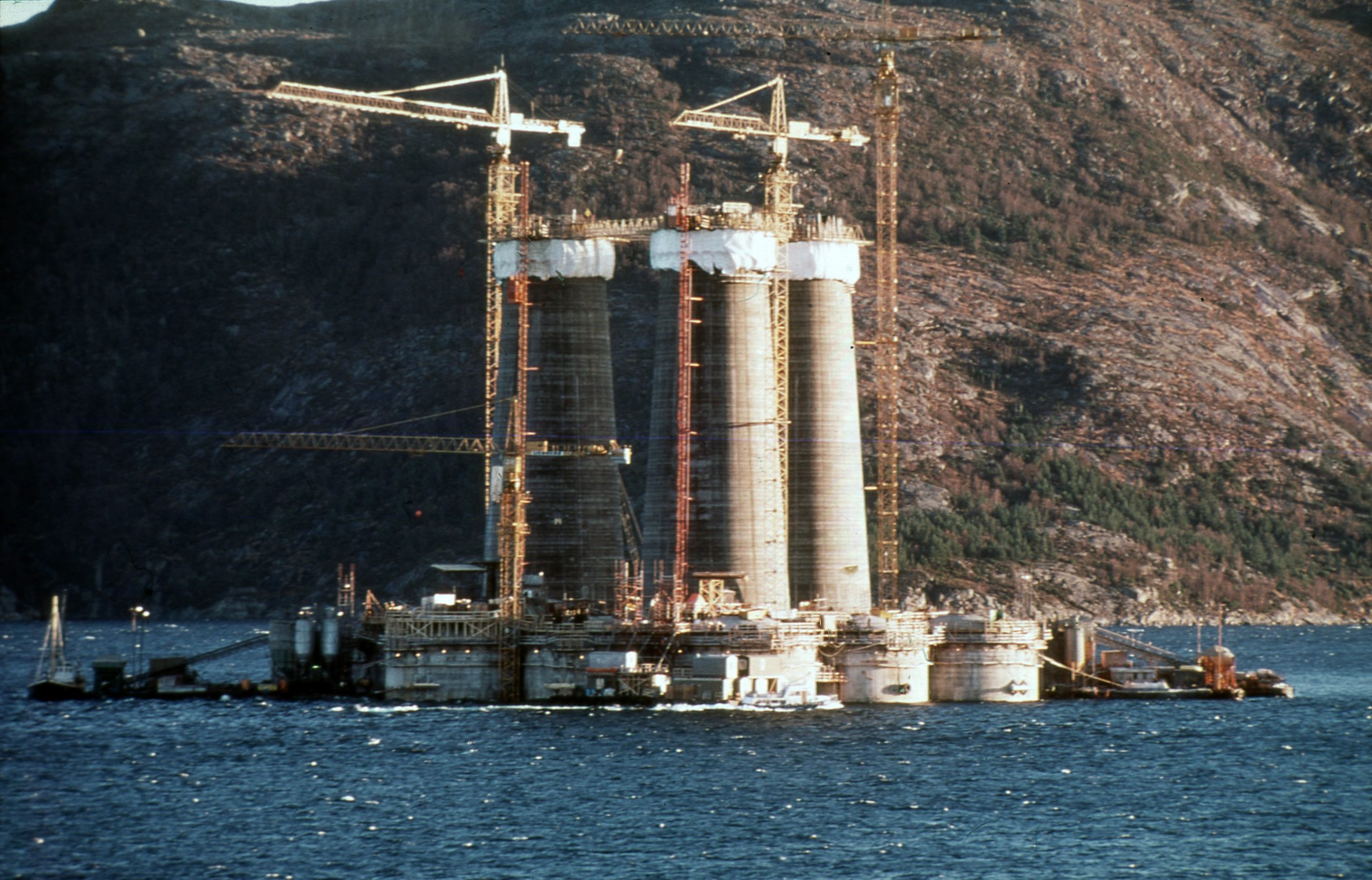
Liquid concrete was poured into the formwork before the concrete below was fully cured – a method known as “wet on wet”. Pouring in this way had to continue around the clock in order to avoid cracks forming in the concrete. When the cells were complete, work continued on slipforming the shafts to a height of 100 metres.[REMOVE]Fotnote: Norsk Oljerevy. (1977). Nr. 3. februar. 17-18. Statfjord “A” – den første i sitt slag etter nytt regelverk. They were raised in parallel.
The Condeep solution
The concrete structure comprises the base, the caisson and the shafts.
Nineteen cylindrical cells with diameters of 20 metres externally and 18.4 metres internally – in other words, a wall thickness of 0.8 metres – make up the caisson. Standing some 70 metres tall, they collectively form a hexagonal base. The main cells are completed top and bottom with cast domes, which are 1.1 metres thick at the base (1.65 metres in cells 3 and 5) and 0.54 metres thick at the top.
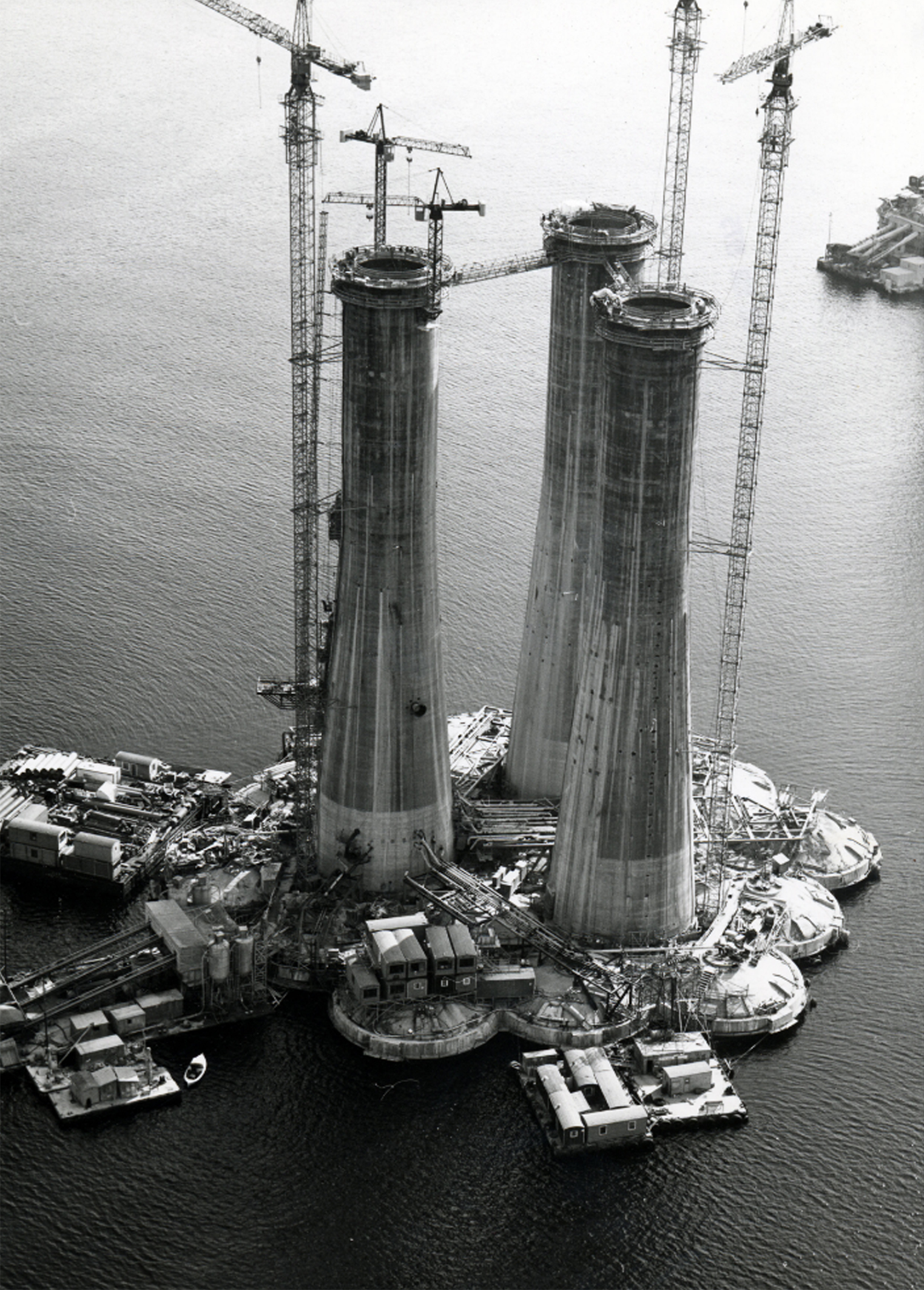
The base comprises the bottom domes as well as the concrete and steel skirts, which are arranged as follows. An 0.5-metre-thick concrete ring with an internal diameter of 13 metres is cast under seven of the main cells and extended with a steel skirt three metres in height. Similarly, 30 concrete rings with an internal diameter of 8.9 metres are cast around the periphery of the caissons and extended with three-metre-high steel skirts.
This continuous chain of concrete and steel skirts is stepped out from actual caisson to increase the base area. In addition, the base incorporates three steel guide pillars embedded in the star cells which extend 3.5 metres below the bottom of the steel skirts.
Three of the main cells – 1, 3 and 5 – are not sealed with domes but continue upwards as three shafts. On Statfjord A, these top out at 26.5 metres above the sea surface on the field and 171.5 metres above the bottom edge of the steel skirts. Through steel transition pieces, the shafts carry the topside structure.
The lower section of each shaft is conical, with an internal diameter of 18.4 metres narrowing upwards to 12 metres at the transition to the topmost cylindrical section. Wall thicknesses in the shafts vary from 1.15 to 0.6 metres.
The cells were slipformed using formwork 1.2 metres high and 0.6-0.6 metres wide, and the liquid concrete was poured into the ready-made forms. Reinforcement bars (rebars) had already been installed by the iron fixers. Some 40 tonnes of iron and 2 200 tonnes of concrete were consumed for every metre of slipforming.
Since the shafts sloped inwards, extending them was a more complicated process. Each shaft has an external diameter of 20.6 metres at its base and 12.2 metres in its topmost sector. The form of the shafts was controlled with the aid of a detailed system of screws. Their diameter was measured every four centimetres.[REMOVE]Fotnote: Stavanger Aftenblad (1975). 8. februar. Gliden på CONDEEP.
The shafts continued upwards with a slight narrowing. Two were intended to house the conductors which extended the production wells to the topside – 21 in each. The third shaft was to contain various utilities, including pumps for transferring crude oil, fire water and ballast water to and from the storage tanks.
During the slipforming process, a barge-mounted concrete mixing plant was moored alongside the Condeep. Concrete, rebars and other equipment had to be lifted up the shafts by cranes as the work progressed.
A lift was installed on the outside of each shaft to take personnel up and down, and scaffolding with railings was positioned at the top so that they could work safely. When the formwork was jacked up, the scaffolding and up to 100 workers rose slowly with it.
Mechanical outfitting
While the base section was still in the dry dock, Aker Offshore Contractors (AOC) had stared work on outfitting the cells. This job continued in parallel with the slipforming after the base was moored out in the fjord.
It was carried on under difficult conditions. The working space inside the shafts was confined, with a diameter of about 15 metres. Equipment was lowered by crane or brought in through temporary openings at the bottom of the concrete wall.
Part of the outfitting involved installing decks – known as “sandwich plates” – inside the utility shaft, which meant working at a number of heights. In the end, a total of 13 decks were spread over the 177-metre height of the shaft. Up to 240 people at a time could be working inside a shaft. The work called for a lot of assembly in places with a free fall of 15-20 metres.
Since the working space was small and narrow, not all the job could be done or all the personnel work at the same time. Some had to yield to others. Various trades were accordingly given first, second, third or even as low as fourth priority. Which teams had what priority varied from week to week as the slipforming progressed.[REMOVE]Fotnote: Intervju med Svein Jørpeland, av Trude Meland Norsk Oljemuseum.
NC owned some large cranes which were used to lift concrete, rebars and other equipment to the top of the shafts. Aker was allowed to use these for four hours during the day and four at night to get its own hardware in. There was a lot of this, and all activities had to be planned down to the smallest detail to ensure that the available crane time was used as efficiently as possible.
Aker also had a large floating crane of 300 tonnes to provide additional assistance. This had a relatively long reach. Although the boom could be extended quite a distance on such a large crane, however, the further it stuck out the lighter the load which could be lifted.
The crane stood on a barge and was exposed to wind and waves. Even a slight wash from passing vessels could have a big effect on the hook. Damage to equipment being hoisted up was not acceptable – nor was injury to people if anything fell down. So the crane had to be used carefully. When the slipforming had topped out, Aker installed its own tower cranes on the shafts.[REMOVE]Fotnote: Intervju med Svein Jørpeland, av Trude Meland Norsk Oljemuseum.
MHE and the weight problems
Statfjord A has been described as a project which was created on the go, and there is a great deal of truth in that characterisation. It was renowned for jobs being done in the wrong order and for drawings produced after the work had been finished – known as “drawn as built”.
Engineering drawing and design, procurement and construction supervision of the Statfjord A outfitting were the responsibility of Matthew Hall Engineering (MHE) in London. Its contract with Mobil was awarded in November 1974 – in other words, a month after work on the GBS had started.
Plans called for the building of a concrete structure with three shafts and a simple module support frame to carry process equipment assembled on the modular principle. That was fairly similar to Beryl A.[REMOVE]Fotnote: Moe, J. (1980). Kostnadsanalysen norsk kontinentalsokkel : Rapport fra styringsgruppen oppnevnt ved kongelig resolusjon av 16. mars 1979 : Rapporten avgitt til Olje- og energidepartementet 29. april 1980 : 1 : Sammenfatning av utviklingen, vurderinger og anbefalinger (Vol. 1). Oslo: [Olje- og energidepartementet]: 178. But conditions changed, and Statfjord A was to become much more complicated.
Two aspects altered significantly during the early construction phase. When work began on the platform, only three exploration wells had been drilled on Statfjord. All indicated that this could be a big field, but each subsequent appraisal well revealed that it was much larger than assumed. That demanded a bigger processing facility, and it was resolved that two parallel trains would be required.
The decision to double production capacity from 150 000 barrels per day to 300 000 was very important, and has subsequently been proved right. It was perhaps this more than anything else which helped to turn Statfjord A into the money machine it has been and remains.
But it was naturally a dramatic change for the project, and meant that a lot of work had to be done all over again. A twofold increase in production capacity meant that all gas systems, coolant water, ballast water, control systems, oil and gas export facilities and so forth also had to be doubled. Virtually everything on the platform was affected, and this was extremely significant for the load the structures had to bear.
Both equipment and modules had to be changed, and the overall weight on the module support frame grew considerably. A heavier topside increased the strain on the shafts, and more and stronger rebars had to be incorporated.
The decision to double the processing equipment was taken after the Condeep had been moored in the fjord and mechanical outfitting was well under way. New drawings had to be produced and work already carried out had to be redone.
The second development was that the Aker group, which had won the contract to fabricate the topsides, secured Mobil’s agreement to build this as a more integrated structure rather than the purely modular solution used on Beryl A, for instance. It was resolved that two-thirds of the modules were to be integrated.
Aker thereby secured a substantially larger part of the deliveries to Statfjord A than initially planned, and MHE also had to produce new drawings for the topside. The latter arrived late and, when finally received, often proved inadequate. They were conceptual rather than detailed construction drawings.[REMOVE]Fotnote: Intervju med Einar Jensen 2. oktober 2008, av Trude Meland Norsk Oljemuseum.
If the schedule was to be maintained, a number of activities had to be carried out in parallel – continuous work was pursued on improving reservoir simulations, optimising the process, producing construction drawings and building.
The computer software available for structural design and analyses in 1974-75 was very limited. Complex calculations took time to perform, often with little in the way of design codes, regulations and specifications. Best estimates were made instead, supported by such codes as were available nationally and internationally.
NC was slipforming the GBS when the decision to double production capacity was taken. The work advanced swiftly, and the company urgently needed drawings of the equipment to be installed in the shafts as construction progressed. A lot of the equipment was supposed to be prefabricated so that it could be easily lifted into place.
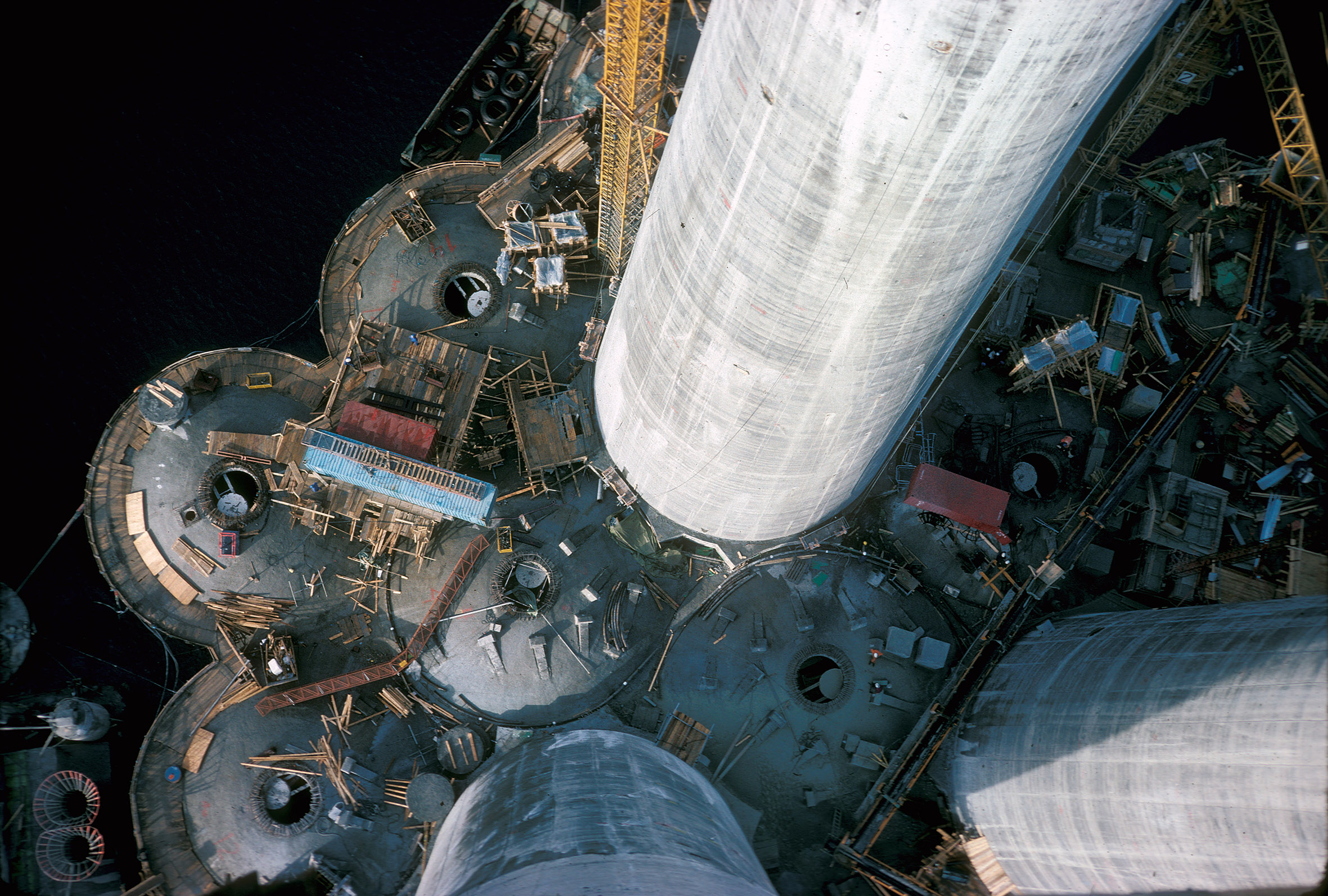
AOC was responsible for mechanical outfitting of the GBS. But it could not complete the dimensioning of systems in the utility shaft, which were primarily intended to support production, until final details of the process facility on the main deck had been decided. Obtaining information accordingly became a race against time. The circumstances were very demanding, and many compromises and decisions had to be made on the basis of the data available at any given time.[REMOVE]Fotnote: Intervju med Einar Jensen 2. oktober 2008, av Trude Meland Norsk Oljemuseum.
MHE made extensive use of draftsmen rather than engineers, and often issued sketches rather than finished engineering drawing. The work proved too complex for the company, and it got started too late.
When part of the equipment for the utility shaft came to be fabricated, the weight of the decks and the systems they were to carry had still not been determined. A probability calculation was carried out, which later proved inaccurate.
The shaft decks became much heavier and their supports had to be reinforced. Engineering design and drawing work constantly lagged behind, and led to much improvisation by Aker’s engineers.
One of the people involved in designing the mechanical outfitting for the Condeep was Einar Jensen. He joined the project in April 1975 as a recently graduated engineer employed by AOC. His first job was to produce detailed drawing for the pipework in the storage cells:
“When we started designing the utility shaft, we had a number of conceptual drawings [from MHE] and we knew what equipment had to be accommodated. But we had no details about this hardware. We had no idea how much it weighed, for instance. How heavy was a pump, a motor, a pipe or a valve? And we were short of time.
“We had to start designing foundations and draw the deck down in the shaft in order to get it finished and to buy in the steel, prefabricated items and so forth. So there was nothing for it but to work in accordance with the best estimates we had. And we were wrong many times. That meant we had to make modifications even while the [GBS] lay here in the Gands Fjord. Very substantial reinforcements had to be incorporated in a number of the decks in the utility shaft.”[REMOVE]Fotnote: Intervju med Einar Jensen 2. oktober 2008, av Trude Meland Norsk Oljemuseum.
It is undoubtedly the case that many of the drawings for the utility shaft decks were produced because they had to be in order to install equipment when NC had reached the relevant point in the slipforming, and not when the details of the equipment to be installed were to hand. That meant changes/reinforcements had to carried out as the final design of the systems was completed.
The engineering departments at MHE, Aker Engineering and AOC were staffed as strongly as possible, but securing the drawings which would optimally have been wanted in relation to the on-going construction work was an impossible task.
Many, perhaps the majority, of the participants in the design work had never at that time been on or seen a production platform. That naturally made things very demanding for those who were senior engineers and had a good deal of experience.
The many changes and lack of information along the way was a source of frustration for many, and incomprehensible to those who did not understand the context and the background.
A number of erroneous calculations were made. Svein Jørpeland, construction manager for AOC during the mechanical outfitting of Statfjord A, remembers a number of examples:
“The decks in the utility shaft carried ballast and crude oil pumps, tanks, coolant water pumps and massive piping systems. When the decks were designed and drawn, no account was taken of the wet weight of the piping. The pipes weren’t going to contain air, after all, but water, oil and other liquids. So we had to set to work with reinforcements.
“All the decks – or “sandwich plates” – to be installed in the shaft were prefabricated at Aker Verdal. We installed them as the slipforming progressed. The shaft was narrower at the top than at the bottom, so the various decks had different diameters. This meant that we had to have the right deck at the right time so that the slipforming wasn’t interrupted. That went OK.
“The problems began after we had installed the decks and began to put the equipment on them. That’s when it emerged that the strength calculations for the decks had not taken account of the wet weight. We had to go in up to five times to reinforce the decks.
“So when you get down in the Statfjord A utility shaft, you see five reinforcements under the main beam. This was time-consuming work, with a lot of welding. Everything was precoated, so all the coating had to be ground off, because the spot where the steel made contact had to be clean. Then you had to weld again, sandblast and re-coat. And everything had to be covered up when sandblasting. Five times!”[REMOVE]Fotnote: Intervju med Svein Jørpeland, av Trude Meland Norsk Oljemuseum.
Time was everything
According to Jensen, the team was characterised by a spirit of creativity which valued improvisation and finding new answers. Solutions and time were the essentials, cost was not an argument. The only question was when things could be delivered. If anything was lacking, it was just a matter of making some phone calls around the world to find out who could deliver the fastest:
“I remember that we’d requested bids for manufacturing some ventilation channels in the shaft, and I got a price from a company in eastern Norway. The job cost perhaps three times as much in the Stavanger area, but delivery was much faster. So the contract went to the Stavanger area.”[REMOVE]Fotnote: Intervju med Einar Jensen 2. oktober 2008, av Trude Meland Norsk Oljemuseum.
Attention at Mobil and the project management was heavily focused on maintaining the schedule. At times, the project embraced several thousand people as well as a great deal of equipment, vessels and other facilities hired at high hourly rates. In addition, operations which needed good weather were dependent on periods when such conditions were most likely – known as “weather windows”.
The most important factor of all was the heavy pressure from the licensees and the government to get production started as planned. Additional costs for securing equipment were trivial in such a context. Causing delays to the project was not an option.
A sluice valve weighing 3.5 to four tonnes ended up in Australia instead of the Gands Fjord. That presented a big problems. Manufactured in California, it was a big structure, four metres high and 48 inches in diameter. AOC had to secure a replacement to prevent the work being delayed more than necessary. Jørpeland took responsibility:
“We couldn’t wait for the one in Australia. I said ‘get hold of a new valve and a new aircraft, and fly it directly to [Stavanger’s] Sola airport’. They had one in LA that we could have, so I chartered a Boeing 707 from there to Sola.
“The operator then had two valves, one in Australia and the other at Sola. Mobil maintained I should have discussed with them before I took action, but I didn’t have time. The aircraft landed and we drove out with a lorry, loaded the valve straight onto it, drove directly to Sandnes, took a tug out and installed it in the shaft. Everything was done in 48 hours.”[REMOVE]Fotnote: Intervju med Einar Jensen 2. oktober 2008, av Trude Meland Norsk Oljemuseum.
The workplace

Statfjord A had become a distinctive place to work even while the GBS lay in the Gands Fjord. After it was towed out of the Hinna dry dock, everyone working on the concrete colossus had to be shipped to and from work by boat. Ferries left the Hetland quay in Hillevåg 25 minutes before each change of shift. Smaller vessels were also going to and fro throughout the day.
The history of Statfjord is a story of chance events and those who seized these opportunities. One of these was Alvilde Berge, known as Shipowner Tina. In an interview with Oslo daily VG in 1981, she explained how she became a shipowner by accident. She was out in her 28-foot cabin cruiser off Hinna when she saw a whole gang standing by the Statfjord GBS and waving. Steering over to them, she learnt that they were workers who had finished their shift but whose ferry to land was out of commission.
So Berge filled up her boat and took them to land. When the last of her passengers was safely ashore, the boat looked like a pigsty and one of the railings was broken. She was also abused by a safety representative for carrying passengers without a certificate.
She turned up at the NC office the next day to claim compensation for the damage. “Then the man who had told me off came up and asked if I wanted a job. I could start ferrying people at once.” That was the start for Shipowner Tina, who eventually became a well-known name in the Norwegian oil industry. Tina was the name of her cabin cruiser. By 1981, she and her partner owned seven boats with a crew of 25.[REMOVE]Fotnote: VG. (1981). 24. juli. Fikk kjeft, ble reder.
Who worked on Statfjord A?
Work continued around the clock on the basis of four shifts. NC had 820 people at work in December 1975, with roughly half of them engaged on Statfjord A and rest on the simultaneous slipforming of Brent D.
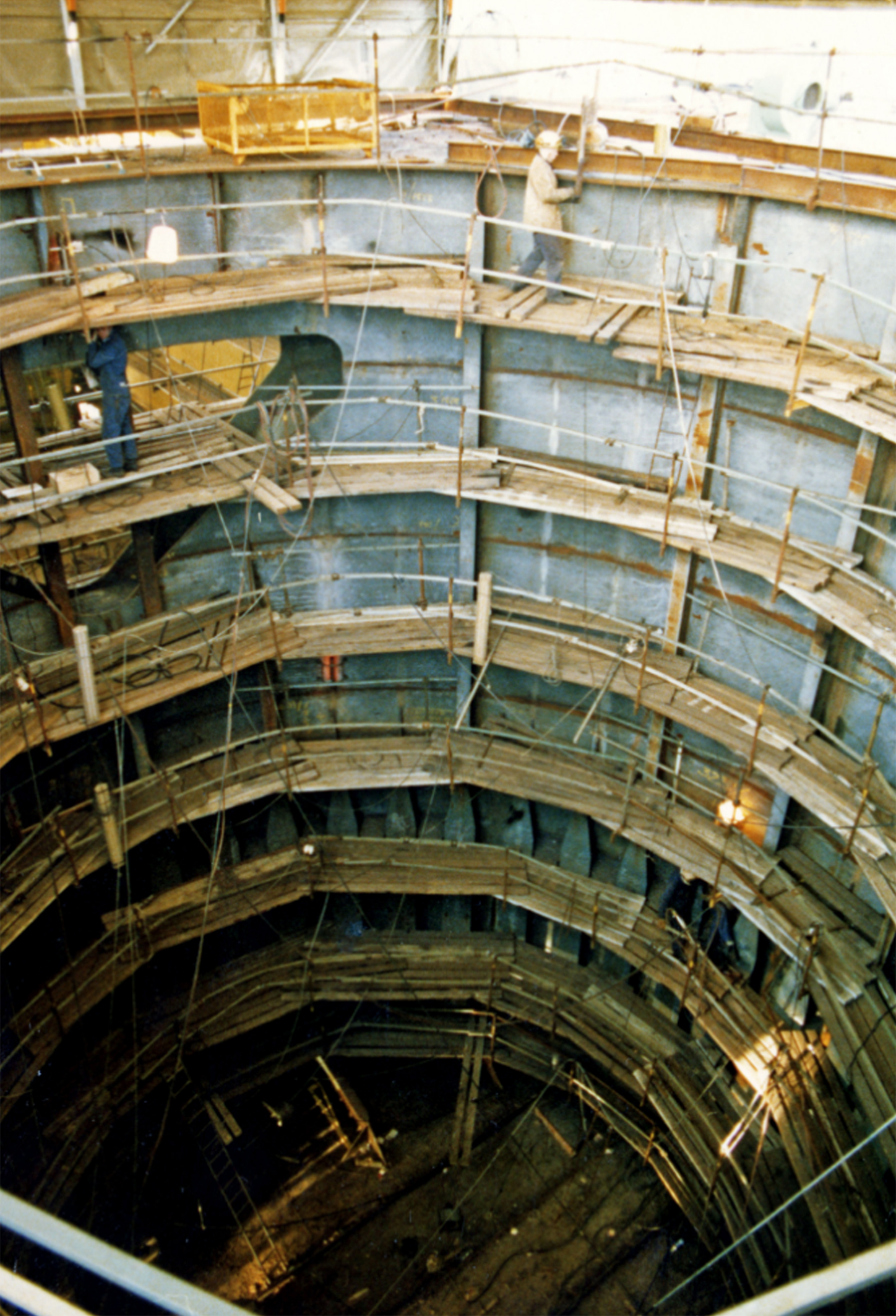
Trades represented at the facility varied constantly on the basis of which jobs had priority at the time. The biggest categories among those employed by NC were formwork setters, iron fixers and concrete pourers. These three groups worked closely together. While iron fixers tied together rebars, the pourers filled the formwork with liquid concrete. The carpenters also built scaffolding, were responsible for embedding special attachment points in the concrete and did odd jobs.
These three groups were supplemented by support personnel such as equipment transporters, crane drivers, radio operators, electricians, cement mixers, warehouse workers, rodmen, formwork jackers, cooks and cleaners. Lift operators
stayed in or near the lift all the time they were at work. The noise level was high, and it was cold and wet at times.
Radio operators occupied the communication centre, known as the tower, which was a temporary office on the structure. They controlled the walkie-talkies, the VHF radio and a number of telephone lines. The tower also served as a place to warm up and take breaks. This was mainly used by the foremen, but other personnel also came in, particularly at night when communication traffic was relatively low.[REMOVE]Fotnote: Stangeland, P., & Baldvinsdottir, A. (1977). Condeep : A platform construction site in Stavanger. Stavanger.
Pipe welders, fitters and electricians – trades found in the mechanical engineering industry – dominated in AOC. Welders formed the largest group. A lot of pipes needed welding, as well as decks in the shafts, stairs, lifts and the like. This was basically conventional sheet metal work, but installation was difficult because of the confined space and large heights. Ventilation was poor and the acoustics a little too good.
The working environment down in the shafts was not of the best. A fog of welding gases, yellow or blue, constantly filled the space. Many workers were plagued by headaches, nausea and bronchitis. The ventilation system which blew fresh air down to the base of the shafts was not very efficient. This was a foggy landscape with a confusion of pipes, tackle, welding gear and scaffolding everywhere. Spotlights lit up certain area, and compressors and cutting machines made a lot of noise.
The concrete walls and the steel decks amplified all sound in the shafts. Surveys reveal that few of the workers used ear protectors. These blocked out all noise, and many were afraid that they would fail to hear if something went wrong.
Those who worked in the shafts had to climb up and down stairs corresponding to a 20-storey building every time they went to work. Anyone afraid of heights was best advised not to work in the Statfjord A shafts.[REMOVE]Fotnote: Stangeland, P., & Baldvinsdottir, A. (1977). Condeep : A platform construction site in Stavanger. Stavanger.
All the workers on the GBS were men. Of the 70 women employed at the facility, 50 were in the work camp and 20 on the hotel ships – which can be regarded as an extension of the site.[REMOVE]Fotnote: Leira, A. (1978). Kvinner på en oljearbeidsplass : En undersøkelse ved Condeepanlegget i Stavanger (Vol. Nr 8-1978, Sosialdepartementets sammendragsserie (rapportsammendrag : trykt utg.)). Oslo: Sosialdepartementet: 30.
The great majority of the women worked in service jobs, such as food, waitressing, laundry and cleaning. Some had more specialised posts, including secretaries, bookkeepers and switchboard operators, while a few had supervisory jobs such as canteen manager, cleaning supervisor and head cook. The last of these roles was usually played by men in the canteen kitchens. There were also two female crane drivers.[REMOVE]Fotnote: Leira, A. (1978). Kvinner på en oljearbeidsplass : En undersøkelse ved Condeepanlegget i Stavanger (Vol. Nr 8-1978, Sosialdepartementets sammendragsserie (rapportsammendrag : trykt utg.)). Oslo: Sosialdepartementet: 91. At peak, 78 companies were involved in the project, but no list is available of all the employees at the Hinna facility.
Environment and unions
Job security on the Condeep was limited. If there was not enough work one day, employees could be dismissed with eight hours notice. Most of the Aker personnel were unionised, but many of the small companies had difficulties establishing proper union representation.
The workforce was constantly changing, employees worked different shifts and had little opportunity to speak with each other.[REMOVE]Fotnote: Stangeland, P., & Baldvinsdottir, A. (1977). Condeep : A platform construction site in Stavanger. Stavanger. Union officials in the large companies were unwilling to deal with issues at the smaller sub-contractors.
Many of the workers came from Finland, and were known for being very able and efficient welders. Some 50-80 Finns worked as welders and pipefitters on Statfjord A. Rumour had it that when they arrived for their shift, they brought packed food with them, went down into the shaft and did not reappear until it was time to go home. Jørpeland is full of praise for them:
“The project wouldn’t have gone as well as it did without the Finns. Their welds were perfect. A Finnish welder had three years of education and was a metallurgist. Their Norwegian counterparts got three months of training. But Finns are Finns, obviously, and after a working stint they usually had a party. And then they were off for two days before they got properly back in the saddle again.”[REMOVE]Fotnote: Intervju med Svein Jørpeland, av Trude Meland Norsk Oljemuseum.
Disappearing acts
Every industrial plant is familiar with materials disappearing, and Statfjord A was no exception. People stole the strangest things. Everything they could take with them was taken, Jørpeland recalls:
“A standby radio centre disappeared from the GBS one New Year’s holiday. Coils of 4 000 metres of copper piping for the hydraulics in the shafts also vanished. New lengths were ordered with a promise that they would be monitored all the way from the supplier to Aker’s warehouse.”
But this did not seem to help:
“I came up to Haugesundsgaten and saw a lorry loaded with new coils of copper piping outside Bøen’s scrapyard. They were the coils destined for the Statfjord GBS which were supposed to be driven directly from the supplier to Aker under supervision. They had been driven straight to the scrapyard. The price of copper was high.”[REMOVE]Fotnote: Intervju med Svein Jørpeland, av Trude Meland Norsk Oljemuseum.
He called the police, who found both the first and the second delivery. So instead of 4 000 metres of piping, Aker now had 8 000 metres.
Scaffolding planks were also popular with the thieves. These knot-free flooring boards were delivered in piles containing several hundred square metres.
The objects which vanished most frequently were tools. Each company had its own tools in dedicated containers, and every worker had to sign for the ones they received. But the losses were nevertheless substantial.
Ali Installation
One of the companies with a big assignment as an AOC sub-contractor was Ali Installation A/S, the Norwegian subsidiary of Sweden’s Asken Industri AB.[REMOVE]Fotnote: Nerheim, Jøssang, Utne, Dahlberg, Jøssang, Lars Gaute, Utne, Bjørn Saxe, . . . Kværner Rosenberg. (1995). I vekst og forandring : Rosenberg verft 100 år 1896-1996. Stavanger: Kværner Rosenberg: 387. While it had previously done outfitting on the Brent B GBS, the company nevertheless presented a challenge.
Outfitting was already behind schedule, and work went on around the clock. One Saturday morning in 1975, the Swedes and Finns in Ali failed to turn up. Half the 420-strong workforce had gone on strike, claiming that they had been promised no tax would be deducted from their pay.[REMOVE]Fotnote: Stavanger Aftenblad. (1975). 7. mars. Skattestreik på Condeep.
Nor was Ali pleased that Aker had the mechanical outfitting contract for the GBS, while it was only a sub-contractor. According to Jørpeland, the company therefore tried to boycott Aker.
The problem was that Aker and progress were dependent on Ali and the expertise possessed by the Swedes and Finns. The Norwegians had little experience of the quality required for an offshore installation, but the Swedish and Finnish personnel had worked in nuclear power stations and were accordingly familiar with the standards set for Statfjord.[REMOVE]Fotnote: Intervju med Svein Jørpeland, av Trude Meland Norsk Oljemuseum.
But Jørpeland was a manager who did not give way. He found a different solution
“When I came to work, I called a friend of mine in Portugal who runs a big company and asked if he could secure 400 men pronto. I ordered Ali off the platform – ‘you have four hours to clear away your tools and everything else,’ I said, ‘because Portuguese workers are coming. I have jumbo jet waiting at Lisbon airport, so all I’ve got to do is to make the final phone call.’
“That sparked a hullabaloo. I said I refused to accept Ali’s behaviour, pure sabotage all down the line, now I’d had enough. If they didn’t apologise, 16.00 was their last hour on board. They naturally ate humble pie, because they actually had favourable terms. I called Portugal again and said that we cancelled.[REMOVE]Fotnote: Intervju med Svein Jørpeland, av Trude Meland Norsk Oljemuseum.
Svenskene forble underentreprenører, men etter denne episoden begynte Aker for alvor å bygge opp en norsk arbeidsstyrke og svenskene ble etter hvert faset ut. En del av de finske sveiserne fikk jobb direkte i Aker.
The Swedish company remained a sub-contractor, but the episode prompted Aker to launch serious efforts to build up a Norwegian workforce. While the Swedes were eventually phased out, a number of the Finnish welders were taken on directly by Aker.
Jørpeland refused to accept shirkers, and knew that managers who could not cope with the pressure of their job were a danger to project.
A riser was due to be installed outside the cells before entering one of the shafts. This S-shaped length of piping, about 80 metres long, had been prefabricated at Tananger outside Stavanger and was due to be shipped to the Gands Fjord on the Uglen crane ship.
Its weight had been carefully calculated. The riser was to hang from the crane during the voyage, and then be placed on a barge close to the GBS. The actual tow from Tananger to the Gands Fjord went well, and Aker’s personnel supervised the whole transport. But the manager for operation did not turn up. Jørpeland recalls:
“I was called up at 03.30 and told that Aker’s personnel were not in the fjord to take delivery. I jumped into my car and got going. When I arrived, I saw that five of the 10 slings holding the riser had broken. I had the biggest shock of my life. The riser was re-rigged as quickly and carefully as possible and lowered to where it was to be attached. It all went well.”[REMOVE]Fotnote: Intervju med Svein Jørpeland, av Trude Meland Norsk Oljemuseum.
That was not the case for the Aker manager who had left the site. Jørpeland was merciless. “I said to him that you’ll get a one-way ticket on the train so that you’ve got time to think about what you did wrong. I said it jokingly.” The manager was downgraded but allowed to remain – AOC needed people.[REMOVE]Fotnote: Intervju med Svein Jørpeland, av Trude Meland Norsk Oljemuseum.
Disloyalty was another type of behaviour which was not accepted, something a gang of Britons discovered. Jørpeland relates:
“It was important that we didn’t have open doors in Aker, so that Mobil was kept in the dark about all our problems. But our people and Mobil’s met at the Cobra nightclub. Mobil willingly bought beer for these Britons in Aker, who began to relate our problems. So when we turned up for construction and project meetings with Mobil, it knew everything in detail.
“I had to put a stop to this. So I bought 10 flight tickers, went to the Britons, pointed at them and said: ‘Here’s a one-way ticket’. I handed out the tickets completely at random and said: ‘If you continue to leak to Mobil, I’ll be back next week with another 20 tickets’”.
That put a stop to the leaks.
Safety

Safety regimes have changed over the years. During the construction and outfitting of Statfjord A, the idea was that people had to take care of this themselves.
Dedicated personnel monitored safety, and fire guards went around and checked that extinguishing equipment and rescue aids were in place on the various levels in the GBS.
Leaving tools, cut-offs or other objects which could fall down on scaffolding was strictly prohibited. But compliance was a matter for the individual.
If a welder sat on top of a shaft, above a 100-metre drop, and flicked away a spent welding rod while changing to a new one, it could drill through a two-inch plank. So superstructures of sheet steel which such rods could not penetrate were installed at entry points to the shafts.
Wooden planks were placed on the first layer of steel, then another sheet of steel and finally more planks. A dropped rod stuck in the wood, but did not penetrate. If it had hit an unprotected steel plate, it would have skidded and continued down. The topmost wooden layer could look like a carpet of nails.
The shafts contained “drop holes” which could be used to hoist out stretchers and the like with the aid of a crane if an accident occurred at the bottom. A basket big enough to serve as a stretcher was lowered in such cases.
Accidents
Accidents happened during work on the GBS. The most serious was on 25 July 1976, when a 20-year-old was hit on the head by a spade and later died from his injuries. That was only days before the structure was due to be towed to Stord for mating, construction work had finished, and clearing up was under way. The victim had secured a holiday job to clear up and get the GBS ready.
This work was being done by various teams who were collecting residual scaffolding and piping materials and putting them in barrels. A new team then came along to sweep the deck and put the trash in more barrels with the aid of spades. A drop hole for vertical transport ran from the top of the shaft to the 80-metre deck. The barrels were lifted up through these openings by the crane, and emptied into containers which were eventually shipped to land.
One man stood on top of the shaft with a walkie-talkie and directed lowering of the barrels by the crane for the first section. Another person then took over to direct the lift to its final destination. A wooden fence about 15-20 centimetres high stood around the drop hole on each deck to prevent objects being shoved off the deck into the opening.
An accident had already occurred when an empty barrel was knocked into the drop hole after being hit by a full container hanging from the crane. Nobody was hurt on that occasion. Part of the fence was damaged and the hole was secured with a rope.
The victim was the banksman for the crane driver, and was standing on the 80-metre deck beneath the drop hole and relaxing when the accident occurred. Part of the wooden barrier was damaged on the 128-metre deck, where a team was sweeping up. The area on the 80-metre deck directly beneath the drop hole above was not marked or cordoned off to make it difficult to stand there.
Exactly what happened was never clarified, but it is certain that a spade fell through the drop hole above and hit the victim on the head. It cut right through his hard hat. The injured man was placed on a stretcher and removed from the shaft by crane and rescue basket. Getting the basket down the shaft was difficult, and people had to stand and guide it. The police could not establish which deck the spade came from or how it had come to be dropped. Nobody was blamed for the accident.[REMOVE]Fotnote: Stavanger Politikammers arkiv. Justissaker. Sak nr. 3243/76.
Diver accident
A lot of diving work was carried out during the construction of the Statfjord A GBS – measurements, piping inspections, pipe plugging, installing anodes on the steel skirts and testing jet nozzles. The last of these were placed low down outside the ballast tanks for spraying high-pressure water during installation on the field to make the bottom sediment swirl up and help the platform be safely positioned. Divers also had to descend to find forgotten objects and tools dropped into the sea. Before the tow-out, too, all temporary underwater installations such as crane foundations had to be removed and the mooring chains cut. A dive was under way in the star cells during the autumn of 1975. These were open, with access from above. Some bolts had been burnt off in 25 metres of water to remove a flange. But the latter would not loosen, and the diver needed a something to break it off instead. He returned to the surface to request the necessary tool, and hung onto the flame-cutter hose while waiting.
Personnel at the top attached a crowbar to the cutter hose with a noose. The diver and the supervisor were not in communication, so the former had no idea how the tool was going to be sent down.
Sliding down the hose in free fall, the crowbar hit the diver in the chest and emerged from his back. The diver survived, but was banned from diving for life because of the damage to his lungs. He eventually ended up on disability benefit. The diving supervisor was held responsible and fined.[REMOVE]Fotnote: Gjerde, K., Ryggvik, H., & Gooderham, R. (2014). On the edge, under water : Offshore diving in Norway. Stavanger: Wigestrand.
Development plan for StatfjordResponsible for Statfjord information