Diving on Statfjord

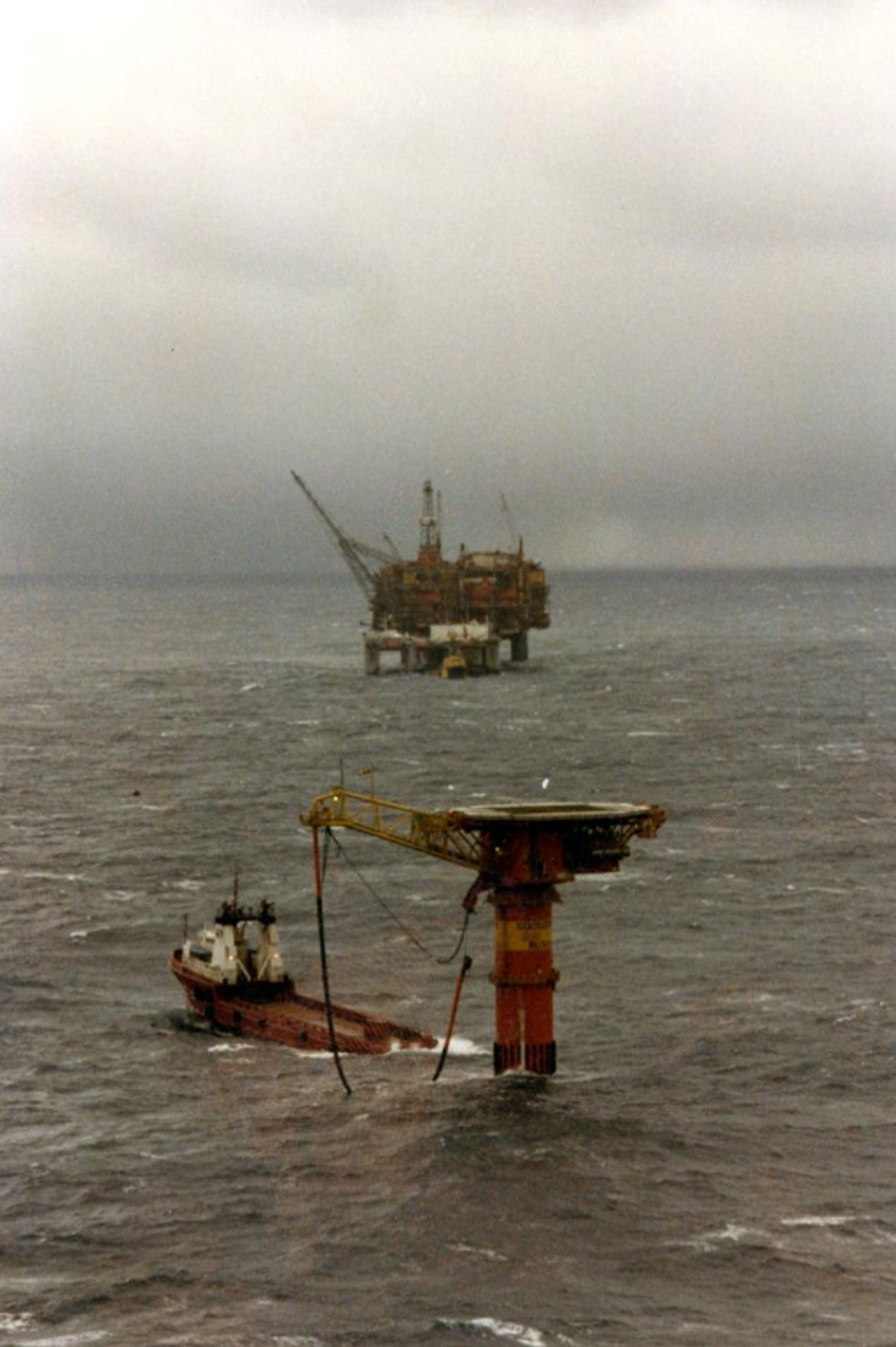
Comex, which won the first major diving contracts related to exploration operations on Statfjord, conducted all its deep dives using the saturation method. Bounce diving with a bell, of the kind carried out by the company from Ocean Viking and other drilling rigs in the Ekofisk area, became both uneconomic and hazardous at a depth of about 150 metres.
As soon as Statfjord was found, intensive producing drilling began in the area. Diving became a really large-scale activity when Statfjord A (1977), Statfjord B (1982) and Statfjord C (1985) were installed.[REMOVE]Fotnote: Hanisch & Nerheim 1992, chapter 6 on the construction of Statfjord. Lavik 1997. Technological barriers constantly needed to be breached, both above and below the waves. getting production going was a matter of urgency. . In many respects, it was even more urgent. The huge investment in oil had created Norway’s biggest-ever trade deficit of NOK 20.5 billion in 1977.[REMOVE]Fotnote: Statistics Norway 1994, p 546. This corresponded to about 11 per cent of that year’s gross domestic product. The country’s foreign debt was rising on year on year, and the government budget was also in deficit.
All the occupational groups who worked to complete the platforms offshore were under great pressure. The overriding priority was clear. It was essential to meet the schedule, make sure that production started as soon as possible, and ensure that the oil and gas could be transported to market. Statfjord A remained far from finished when it was towed out to the field in 1977. The next two platforms could build on experience from the first, but were also characterised by incomplete drawings, hasty planning and poor design, and occasionally by solutions which were far too complicated. Many of the weaknesses were below water. That meant it was the divers who had to carry out difficult repairs and improvement work. Without an intensive commitment by this group, the platform would never have produced oil.
Particularly big problems were created on Statfjord A by the loading buoy installed alongside it. The effort to pipe the oil ashore had been dropped in favour of loading into tankers on the field. Although this was simpler than laying a pipeline over the Trench, it presented difficulties enough. Vessels of 150 000 deadweight tonnes lay in high seas and strong currents and tugged on the buoy. The latter was attached to a swivel on the seabed which allowed it to oscillate a little in response to pressure from the tanker. As so many times both before and since in the Norwegian oil industry, however, what might seem a simple solution on an engineer’s drawing board did not behave as intended once it was exposed to ungovernable natural forces and required to function together with other complicated technological systems. So the divers had to set to work. They first had to go down to survey the problem. Repairs could then begin. These included having to weld on a wedge system – work of kind which not even the most advanced submersibles could perform. In such circumstances, a diver could undoubtedly feel at times like a remotely controlled machine. The work was monitored on cameras from surface. Not a few, often contradictory, orders could flow from the diving leadership and the contractor responsible for the construction work. The result therefore depended crucially on the assessments and actions of the diver on the spot. In such cases, what mattered was his ability not only to operate under water but also and equally to improvise and act as a practical problem-solver.
Even though friction could arise between the divers on the seabed and the person leading the operation, however, both sides were trained to understand each other. The position most divers feared above all was having to follow decisions made by the operational management on the production platforms. On drilling rigs, the rig manager, drilling personnel and maritime crew were people the divers could relate to on a day-to-day basis. Work acquired a routine character as the rig moved from well to well. Operating large platforms also became routine – as the years passed. But much more complex technological systems were involved. A number of functions which on land would have been located in separate factories were concentrated in one and the same place.

From a diver perspective, the big production platforms presented a number of dangers. Several submerged intakes might be present, drawing in cold seawater to cool down machinery on board. These were activated without regard for possible divers in the vicinity. Other types of pipe sticking out from a platform could be equally hazardous. A common potential trap for divers was the blind flanges closing off pipes which might be required for later connections. Divers assigned to remove these covers depended on the platform management having the pressure under control.
That was not always the case. An episode in 1984 can serve as an example. A diver was told that it would be safe to enter a pipeline for inspection. While he was inside, a valve was opened and the diver was blasted out into the sea like a bullet from a gun.[REMOVE]Fotnote: Interview with Albert Johnsen, 24 April 2007. The dive was being conducted with an umbilical in 30 metres of water. Both mask and equipment were blown off. The diver had to ascend rapidly and enter saturation treatment. He survived. However, a diving superintendent recalls having to pluck pieces from destroyed equipment out of the diver’s skin.
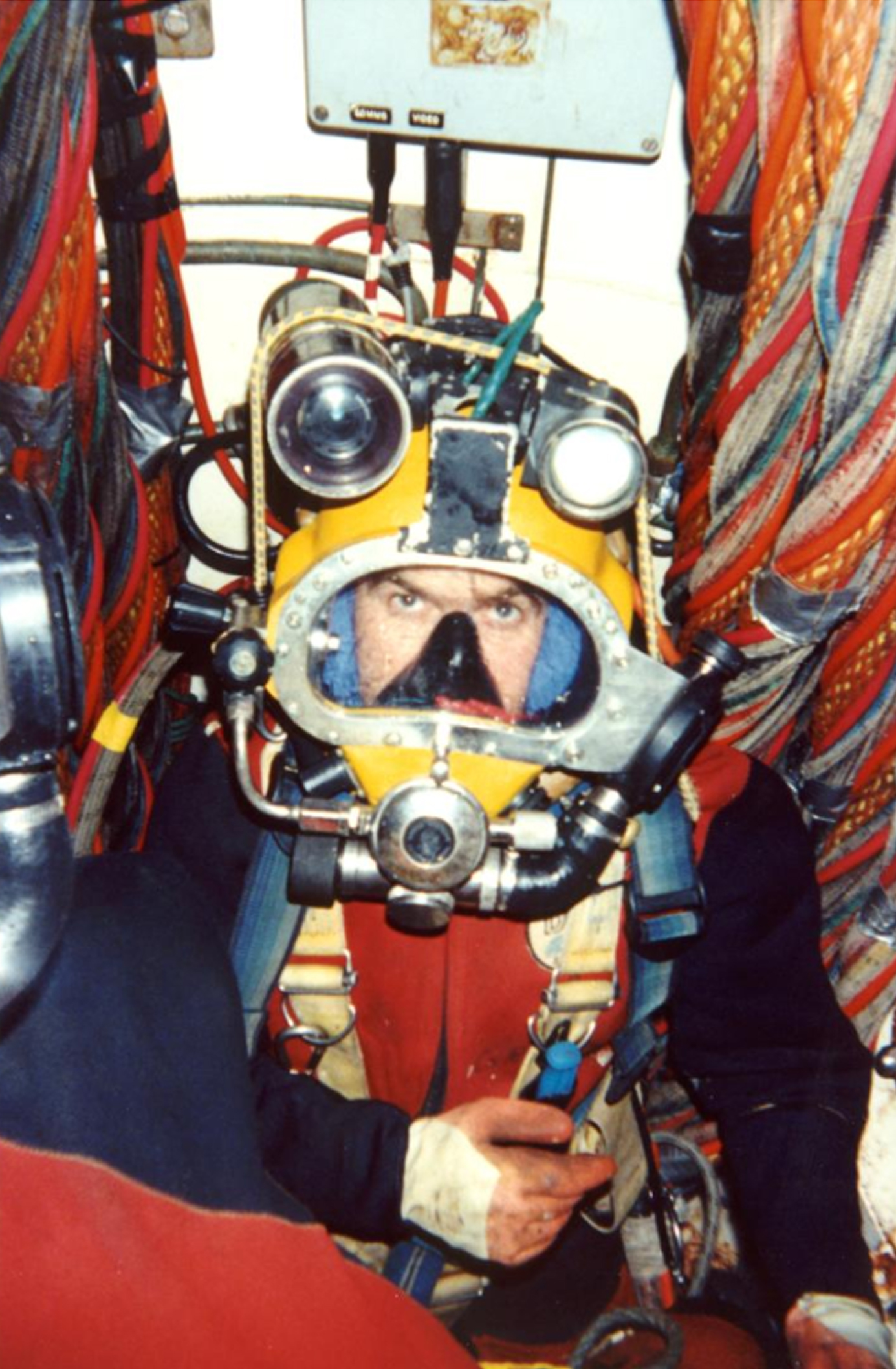
A substantial part of the diving on Statfjord was conducted to install a complex system of flowlines between the various platforms. Unlike the gathering lines from Ekofisk and Frigg, and the later gas pipeline from Statfjord, these infield flowlines were welded together by divers on the seabed. For simple jobs, this could be done directly in the water. Although it might be thought that such surroundings would extinguish any flame, the heat generated by a welding torch is so great that it will also work on the seabed. Unless additional aids are deployed, however, subsea welding creates a brittle weld which will be too weak in most contexts – not least for flowlines required to carry large volumes of oil and gas without leaking. As a result, most of the seabed welding on Statfjord was conducted in the dry using a hyperbaric chamber similar to the system first adopted on Frigg. After welding, the flowlines were buried by a specially designed trenching machine. Given all the activity which took place in the waters around the platforms, the risk that flowlines lying uncovered on the seabed would be damaged was particularly high. But the divers were responsible for ensuring that the job was done properly. Moreover, they were not infrequently required to help lay sandbags. Handling such loads under saturation in a depth of 150 metres for four hours or more at a stretch and for many days in succession was hard work.
Never before or since have so many divers worked in one and the same place off Norway as during the Statfjord development. During a single season, six-seven DSVs could be at work in connection with the field. In addition to its maritime crew, such a vessel employed about 30 people on the diving side. So 200-300 people could have been involved in underwater work during the peak period. Since their time was split roughly 50-50 between ship and shore, a total of 500 diving-related personnel could have been involved with Statfjord at peak.
The diving companies competed vigorously for a long-term main diving contract on Statfjord when it was put out to tender in 1979. Possessing experience, sufficient suitable equipment, and a staff of experienced divers and diving supervisors was naturally essential for a contractor. But it was still the case that the most important competitive advantage over rival companies was how fast a specific job could be done and at what price. The crucial consideration in that context was the kind of diving tables used.
Mobil was operator for Statfjord and thereby primarily responsible for awarding contracts. But Statoil, with 42.7 per cent of the unitised field and ambitions to take over the operatorship, also influenced the choice. Many people in the Norwegian diving community accordingly expressed disappointment when the contract went to Britain’s Wharton Williams (2W) and not one of the domestic companies.[REMOVE]Fotnote: VG , 1979 (undated from cuttings archive), ”Dykkere som arbeider i Nordsjøen: Nordmenn presses ut.”
Although 2W was a foreign company, however, the first long-term diving contract on Statfjord nevertheless represented a certain degree of Norwegianisation. It worked from DSV Tender Comet , owned by Norway’s Anders Wilhelmsen. The company also undertook to use Norwegian divers as far as possible. Since this was a long-term assignment, that was in many respects advantageous for the British company – providing the Norwegians had the necessary expertise. After all, divers had to be flown in and out of the Statfjord area from heliports in Norway. Over time, it was therefore beneficial that they lived nearby. The first North Sea divers were used to moving from one company to another, and many found a long-term job on Statfjord attractive. So 2W had no difficulty recruiting Norwegian personnel. During the 1980s, close to 70 per cent of its divers hailed from Norway.
Nor was 2W by any means the only company to secure work on Statfjord. The scale of diving operations was so great that both Comex and Seaway Diving – which had now changed its name to Stolt-Nielsen Seaway (SNS) – won contracts for short-term work relating to various special assignments. Precisely because these were short jobs, the companies relied heavily on contract divers. The proportion of Norwegian divers employed by SNS was smaller at times than in 2W’s operations on the NCS. That was something of a paradox, given that a SNS representative had complained about 2W not being Norwegian.
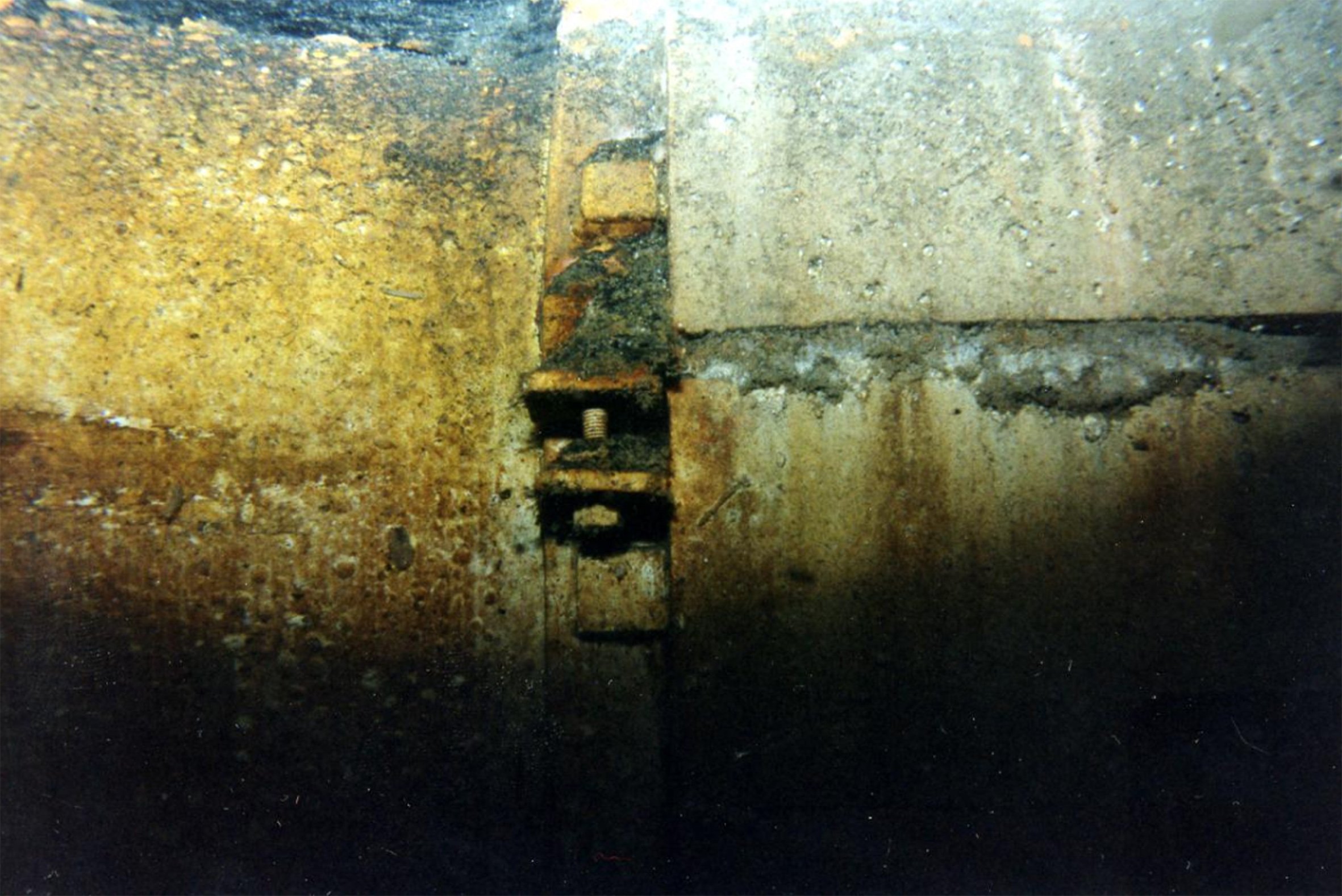
The sub sea technology has changed. At the end of the 1980s, ROV technology had completed its first trial-and-error stages and these vehicles were largely able to replace divers in a number of areas. In the 1990-s Statoil wanted to do all their offshore operations without divers, and the first diverless inspection on Statfjord took place in 1996.