Platform utilities

Chemicals
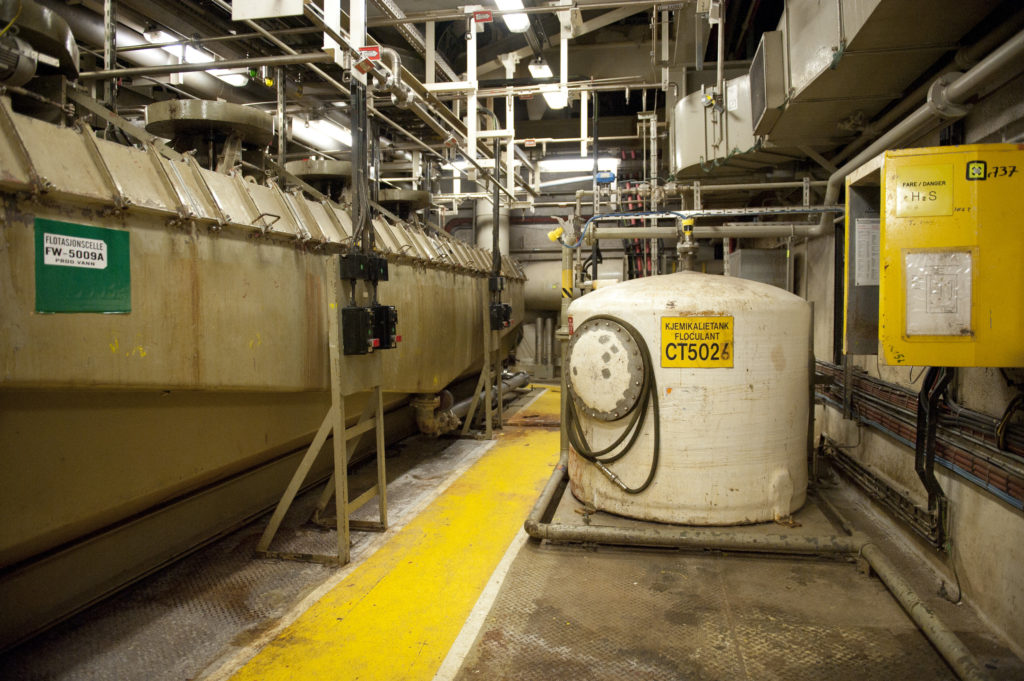
Many different chemicals and chemical compounds are used on the Statfjord platforms for such purposes as separating oil and water. Other applications include inhibiting or breaking down oil droplets in the produced water (emulsions), which is separated from the crude oil flow. Chemicals also prevent or stabilise foaming, or inhibit hydrate (hydrocarbon ice) formation, bacterial growth or corrosion. These substances are shipped out to the platforms on supply vessels. Among the commonest are the following:
Methanol is used to prevent the formation of hydrate plugs in pipelines, which can halt liquid flow. When gas contains small quantities of water, ice-like clumps can form under special pressure and temperature conditions.
Glycol primarily serves an agent for removing water from rich gas because it acts as an efficient absorber of water. It is also used in coolant systems to reduce the freezing point to -12°C.

Chlorine can be added to seawater to prevent the growth of bacteria in pipelines and ballast water, seawater and fire water systems. Sodium hydrochlorite (NaOCI) or bleach is used to kill unwanted organisms.
Corrotion inhibitor is added to prevent internal corrosion in piping and tanks. The substances used are usually based on organic compounds which form a protective film on metals.
Baktericides are deployed to control the growth of bacteria in water and hydrocarbons. The most serious problem for oil and gas production is provided by the sulphate-reducing bacteria, which develop hydrogen sulphide (H 2 S). This substance is not only toxic but also both explosive and extremely corrosive.
Anti-foaming agents are used to prevent foaming in the main process, and are injected ahead of the separator tanks in order to ensure that separation of water, oil and gas is as efficient as possible.
Fuel
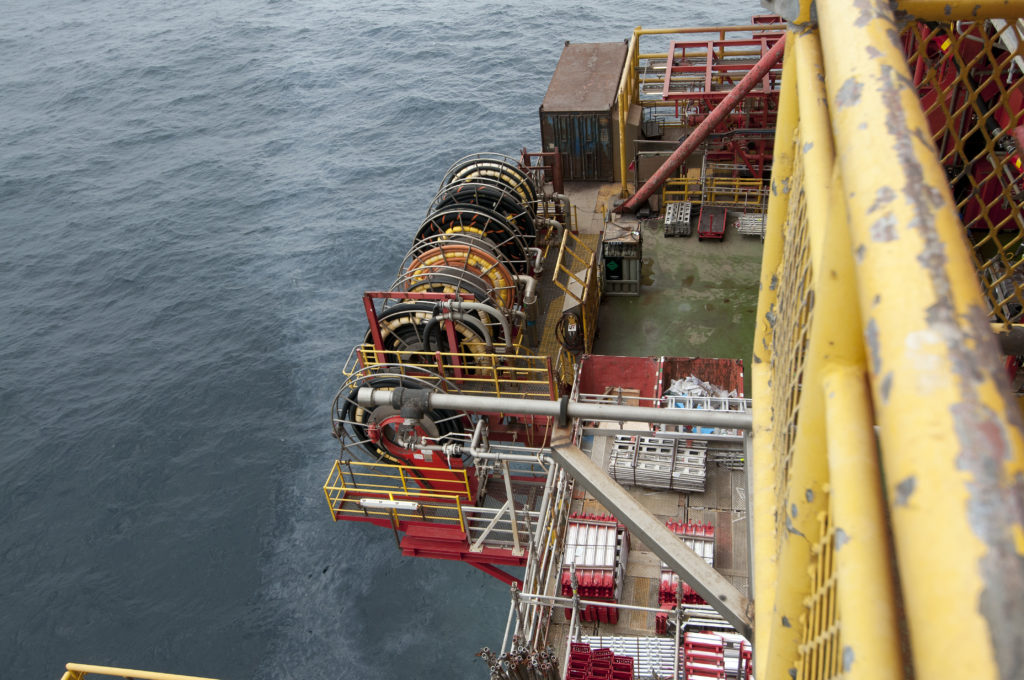
Two types of fuel are needed on the platforms – helicopter (aviation) fuel and diesel oil for power generation and other specialised machinery.
Supplies are brought in by ships equipped with special tanks for helicopter fuel. These can also pump diesel oil directly via hoses to special storage tanks in one of the cells of the concrete gravity base structures (GBSs).
Lubricating oil
This system distributes various types of lube oil to the main systems through a permanent piping network.
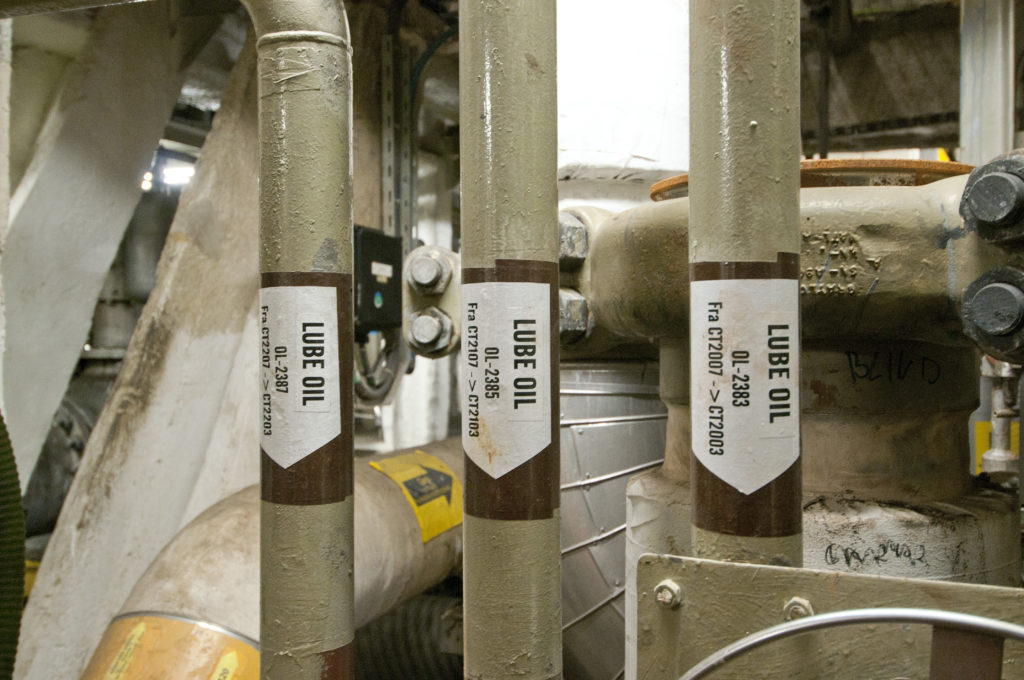
From the filling (tote) tanks, they are piped via lube oil distribution tanks to the most important consumers – gas turbines, generators, water injection pumps and fire pumps.
Other types of oils/lube oils are also required on board, but the level of consumption does not warrant a fixed distribution system for them.
Water
A platform requires a lot of water for various purposes. The sea and service water system is designed to supply all the liquid required for drilling, injection and ventilation systems as well as for producing fresh water. Separate systems are installed for fire and ballast water.
Flushing water is used to help wash sand out of the vessels used in the separation process.
Fresh water is produced from seawater with a maximum chlorine content of two parts per million (ppm). This is distilled in three evaporators. The resulting water is cooled down before being pumped through two units which regulate its acidity (pH value) and into storage tanks. The latter can also be filled with desalinated water or potable (drinking) water from supply ships. Most fresh water is used for drinking, with some also consumed by cleaning and cooling.
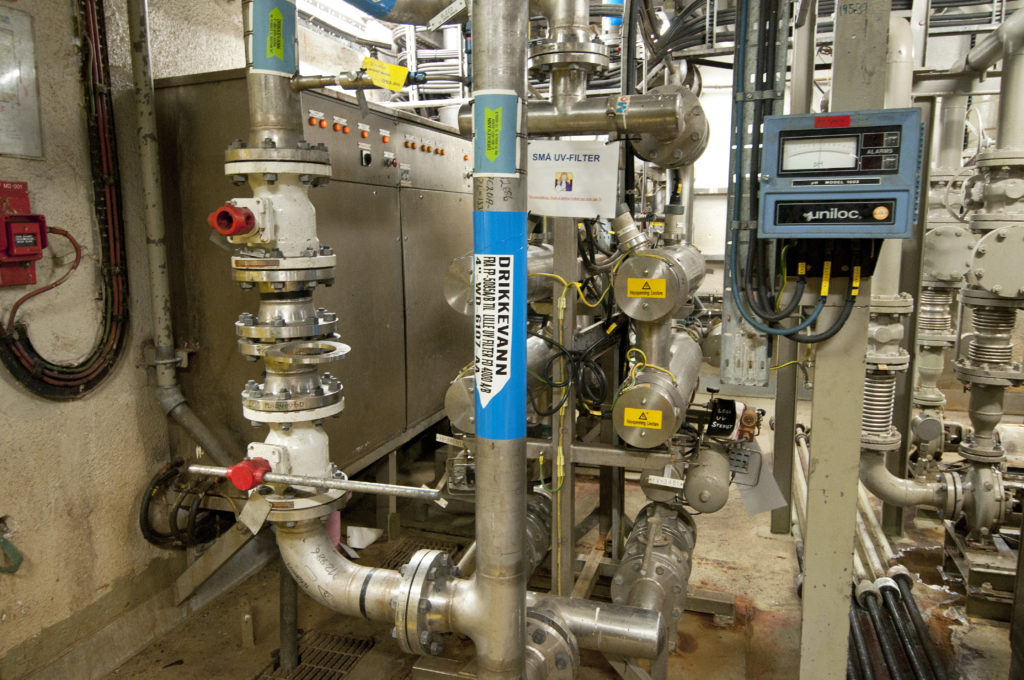
Potable water is produced for use in the living quarters and selected areas of the platform. Desalinated water is pumped from one of the storage tanks via ultraviolet sterilisation units to consumer tanks located on the roof of the living quarters.
Desalinated service water is fresh water of secondary quality stored in a tank on the cellar deck and distributed by pumps for cleaning, drilling and refilling coolant water.
Coolant water is used in coolers for gas and recovered oil. It is a mix of three parts fresh water from the distribution system for desalinated water and one part monoethylene glycol from the glycol system, giving a freezing point of -12°C. A small quantity of corrosion inhibitor is also added.
Warm water is produced to provide a reliable heat source with a constant temperature for the following applications:
- desalination of seawater in evaporators
- heating and ventilation systems (except for the living quarters, which have electrical heating)
- supplies of coolant water to the circulation pumps for hot medium.
Steam comes from a generator at a pressure of eight bar for cleaning process vessels and for various other types of cleaning. The steam generator is a heat exchanger.
Heating, ventilation and air conditioning
These functions are split into two separate systems, covering the production area and the living quarters respectively. The system for the production area is designed to deliver air at a specified temperature and pressure to the platform’s modules. This is intended in turn to reduce risk and accidents in spaces where fire and explosion are hazards (see compressed air below). Provision of such air is crucial for safe operation of the platform. Should the system fail for any reason, the process plant must be shut down immediately. Heating and ventilation of the living quarters involve a completely separate system, which functions in the same way as an installation in a normal building on land.
Heating Medium System serves as a heat source for:
the circulating hot water system for desalination of seawater and space heating, with the exception of the electrically heated living quarters
- steam generation
- superheating of sludge
- sludge treatment
- stabilising condensate
- glycol distillation
The heat source is a refined paraffin circulated to the user sites, where it is heated in furnaces over an open flame and in three recovery units for waste heat.
The air conditioning system in the living quarters serves cabins, recreation areas and the galley. Located in the ventilation room on the service floor, it sucks in fresh air and delivers it at a predetermined pressure, temperature and humidity to the whole living quarters.
A helideck heating system keeps the deck free of ice, maintains the temperature of the fuel gas and the process gas piping to prevent formation of condensate and hydrate (hydrocarbon ice) respectively, and prevents the fire and injection water systems from freezing. Heating cables are located in channels under the helideck, with electrical heating strips installed externally on piping. These activate automatically if the ambient temperature drops below 5°C.
Compressed air
In a process facility where explosive gases could build up, electrical instruments and spaces containing such equipment must be kept at a pressure above the surrounding plant. This is intended to prevent gas from entering and being ignited by electrical sparks. A dedicated system provides a reliable source of clean compressed air for instrument and working atmospheres.
Sewage treatment
This system collects all sewage and waste water for treatment and subsequent discharge to the sea. Most of the sewage comes from toilets, showers, washbasins, kitchen sinks and washing machines in the living quarters. It is conducted by gravity and negative pressure to septic tanks. A filter removes solid particles, which are then sent to mills for grinding to a liquid sludge. All bacteria in the sewage – particularly coliforms – are killed by chlorine injection before treated waste is discharged to the sea 10 metres below its surface. If necessary, raw sewage can be discharged to a barge through a hose connection for disposal on land.
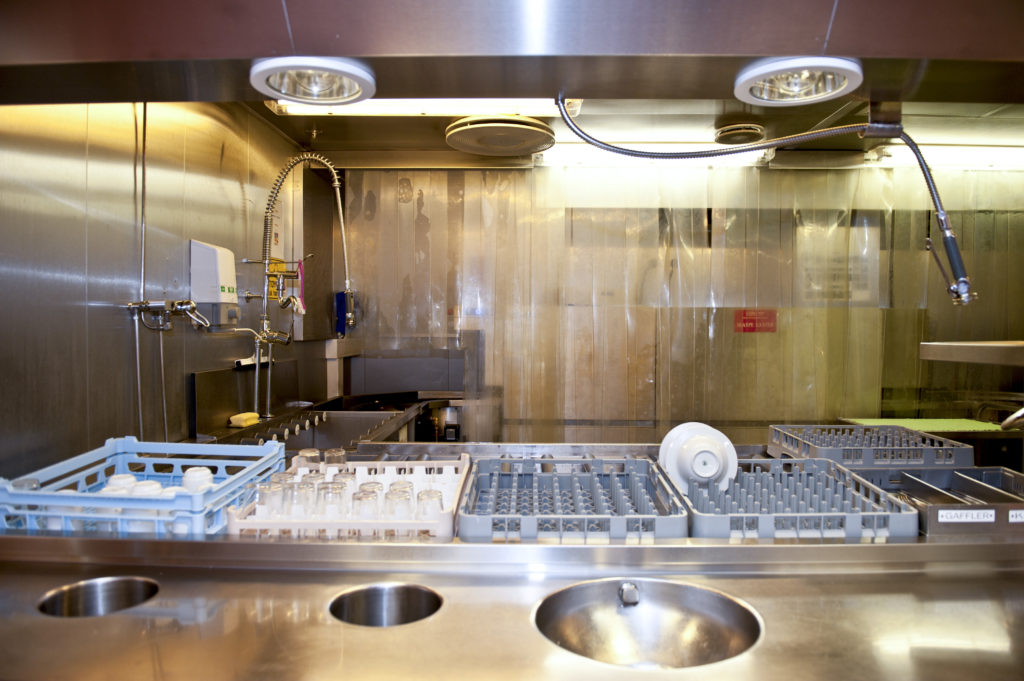
Hydraulic control system for the utility shaft
This ensure a fail-safe supply of hydraulic fluid to operate various valves. Three hydraulic power packs are installed in the utility shaft, supplying four systems.
Loading / Discharging
The loading/discharging system is designed to handle supplies brought in or taken away by sea.
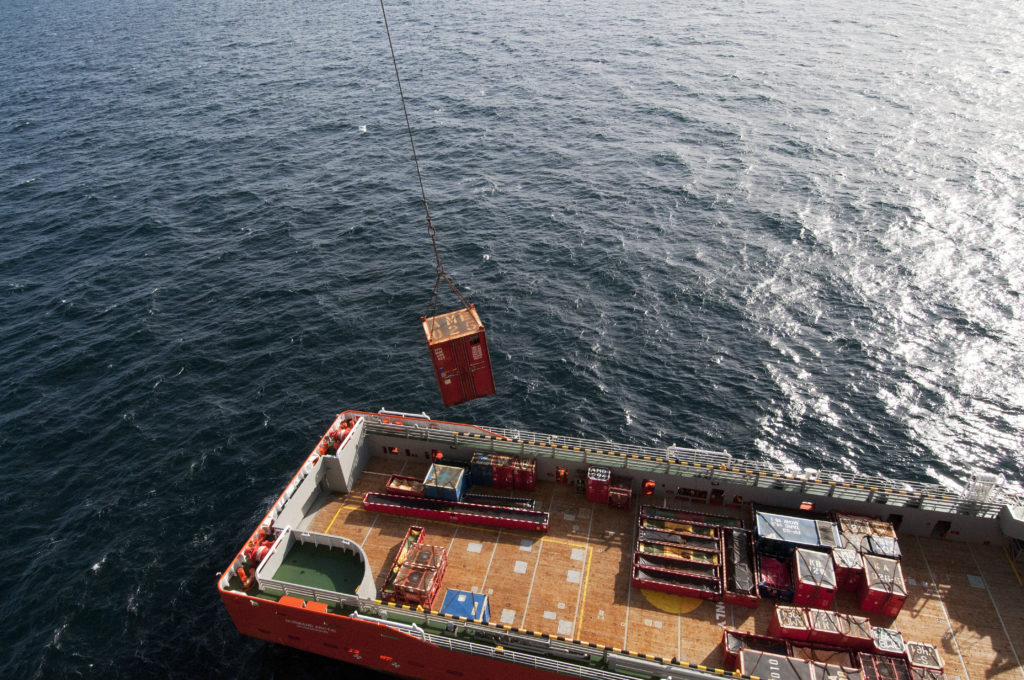
Cranes
Cranes on the platform are used for:
- lifting from or discharging to supply ships
- maintenance and construction lifting over the whole platform and in the equipment shaft
- handling pipes and equipment.
Bulk handling
Equipment for bulk handling is used to transport, handle and store various liquids, powders, gases and chemicals required for the platform’s process system and utilities. These products are brought out by supply ships and transferred to the platform either in tanks or via hoses.
Tanks and other bulk containers are lifted by crane from the supply ship to the platform’s storage area on the open deck. Liquids used in large volumes are transferred via permanently installed piping to the fixed storage tanks. Empty tanks are discharged for transport to land.
Diesel oil, fresh water, barytes, gel and cement are transferred to the platform’s bulk storage tanks with the aid of hoses lowered to the supply ship.
Power supply
The electrical system on the platform provides all normal and emergency power supplies.
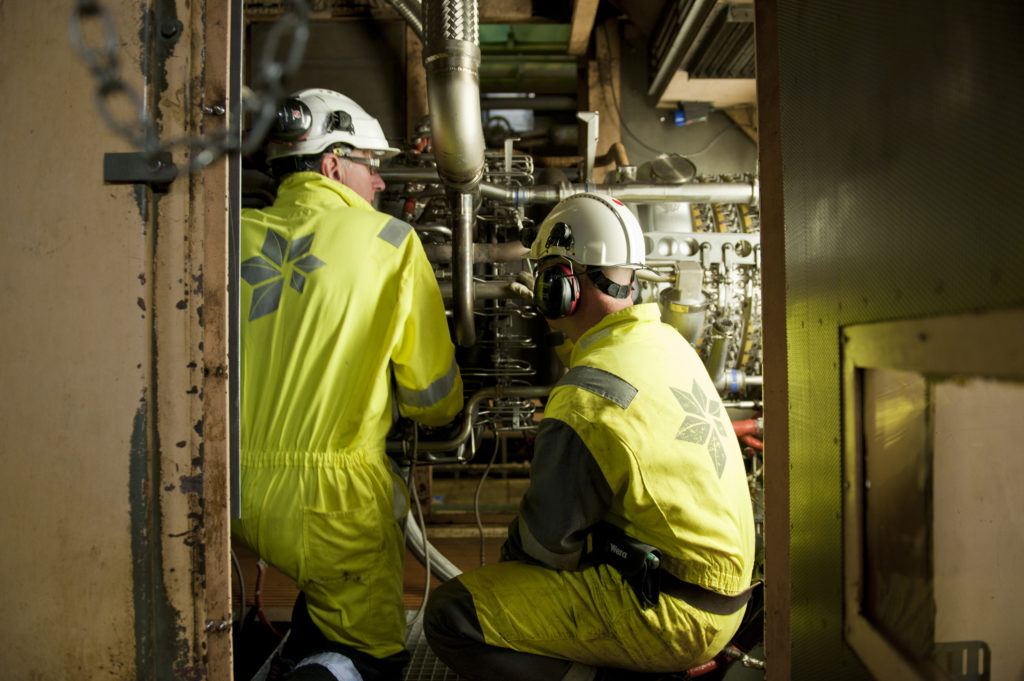
Main electricity is supplied by three 19-megawatt generators as 13.8 kilovolt, three-phase 60 Hertz current. The generators are driven by gas/diesel turbines.
Emergency power is supplied by three 1.18 MW generators which start up automatically and connect to a 6 kV panel. If both main and emergency power systems fail, supplies of alternating and direct current will be maintained by batteries..
Electricity for the living quarters comprises the normal supply of alternating current, and emergency supplies of both alternating and direct current. The normal supply is used for air conditioning, galley equipment, heating, hot water, laundry, lifts, lighting, refrigerators, waste units and ventilation. Emergency supplies are used to maintain necessary lighting and electronic equipment.
Flaring and atmospheric ventilation
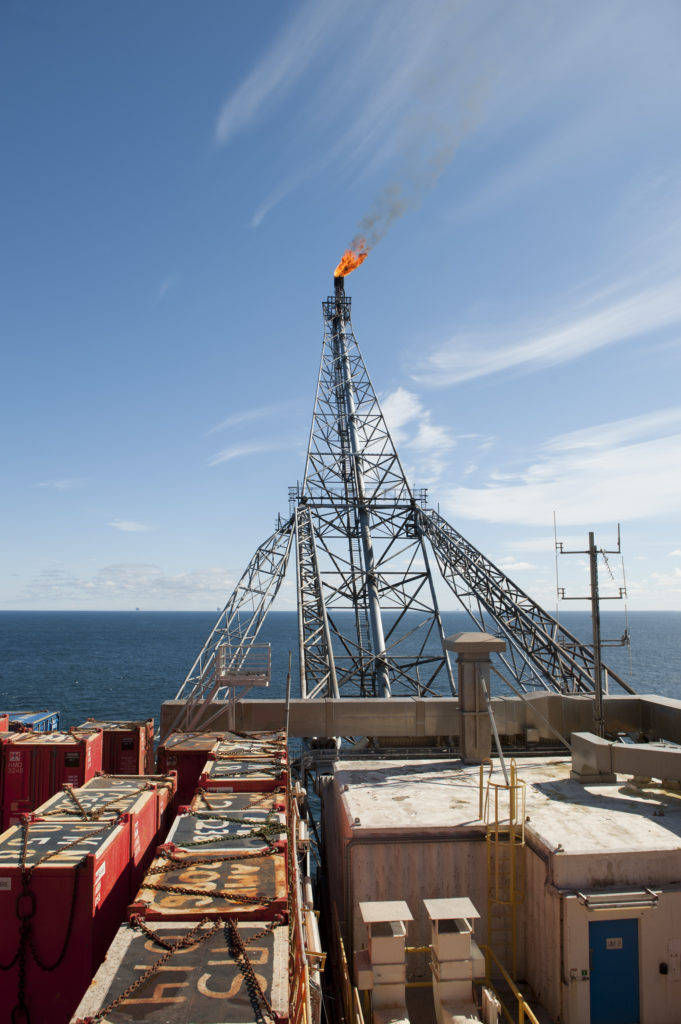
Hydrocarbons are found under varying pressure and temperature on large parts of the platform. For practical and safety reasons, some of the gas can be led to a safe place for flaring.
This can involve process gases, pressure reduction as part of an emergency procedure, or removal of gases so that maintenance can be carried out.
In the event of a total pressure dump, large volumes of gas will flow out at the tip of the flare boom. This is burnt off immediately to prevent undesirable distribution.
Tanks containing volatile liquids, which vaporise easily under atmospheric pressure, must also be vented safely. They are not all in the same place, and accordingly have dedicated vent pipes led to the sides of the platform or to points at least seven metres above the upper deck.
Monitoring and control
Process control monitors and controls all systems on the platform to ensure that hydrocarbons can be produced as safely as possible. The main functions involve:
- maintaining a check on data transmission between the production system and the control-room terminals
- analogue operating commands
- automatic switches and logical sequence control commands
- alarm logging
All this information is monitored from a central control room. Printers and displays for alarms and trends are also concentrated there to provide the operators with a good and accurate picture of conditions at all times.
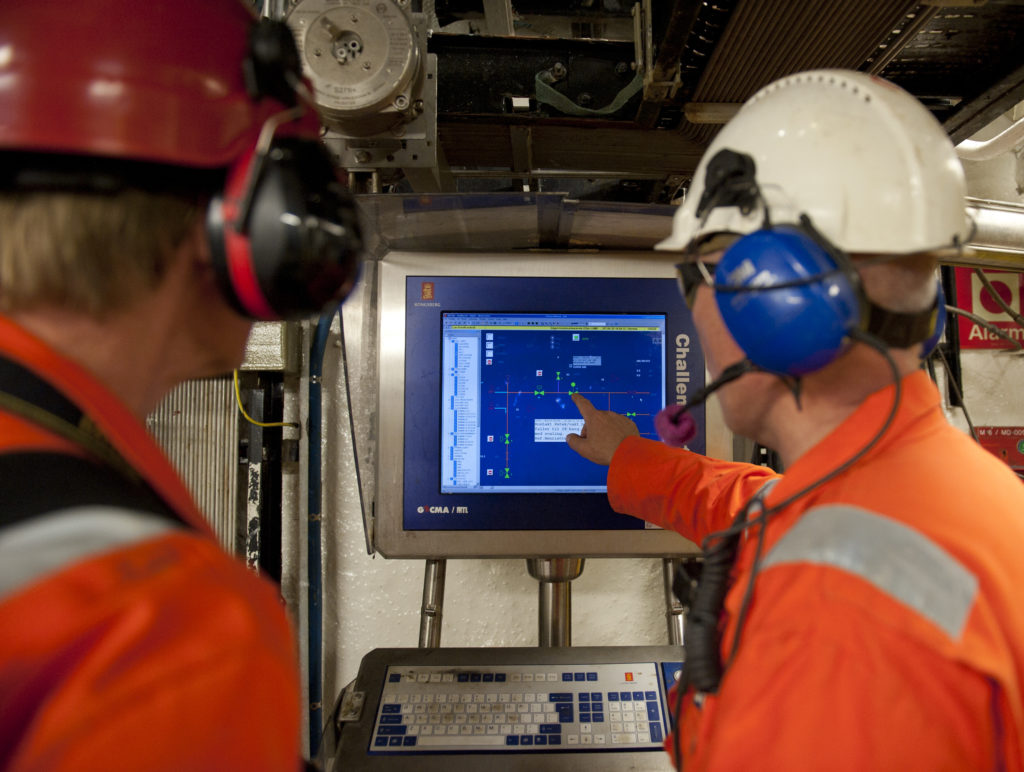
Safety monitoring is a system intended to handle “all” aspects of safety on the platform. Field instrumentation and sensors for fire and gas alarms monitor the whole process and every module.
The purpose of the system is to initiate emergency shutdown of production when the process monitoring system fails to handle the problems which might occur. In principle, it comprises two systems:
1. The process shutdown system monitors the process and shuts it down if control is lost, and thereby prevents the plant being operated in a hazardous manner – under pressures higher than the tanks are designed to handle, for example.
2. The emergency shutdown system, which reacts if hazardous conditions arise – such as a gas leak or a fire. This system receives signals from fire and gas detectors as well as from manual alarms.
The metering system for production and consumption meters the quantity of gas and oil exported from the platform as well as the amount of consumption and fuel gas used internally. This system attracts great attention from all levels of the organisation, since its measurements form the basis for the revenues generated and the tax to be paid on output.
Safety and security
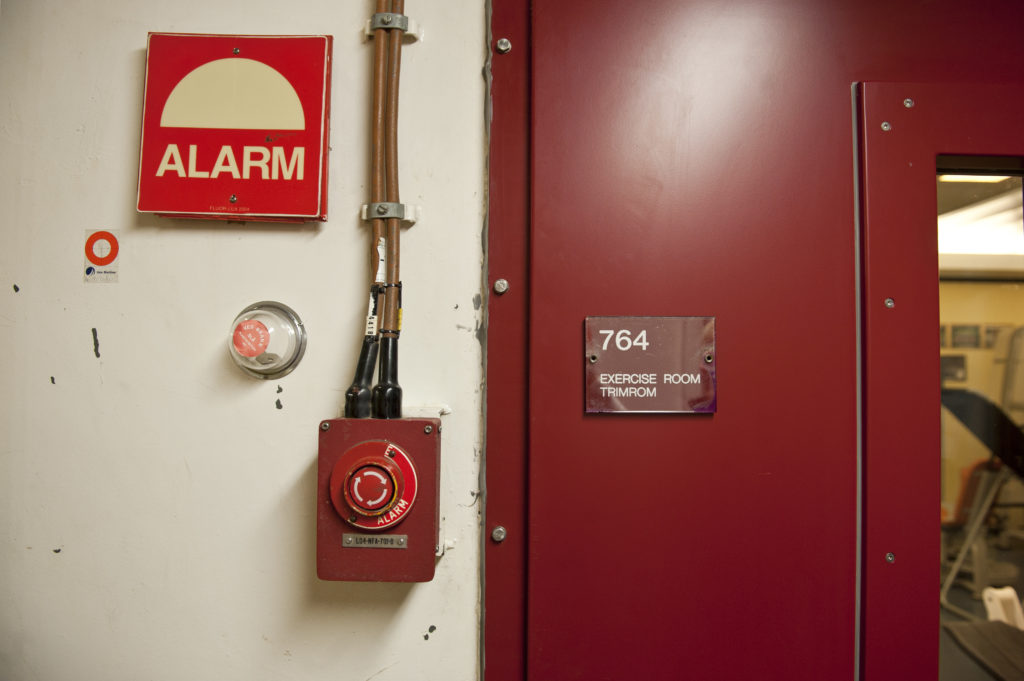
Systems in this category are required for notifying and executing actions to prevent or reduce major or minor damage. They also include systems for emergency evacuation or for retrieving people who have fallen into the sea.
Fire and gasdetection
All areas of the platform are fitted with fire and gas detectors. Should fires or leaks be registered, the following actions are initiated automatically:
- fire pumps start
- sprinkler/deluge systems are initiated (halon has been phased out)
- fire dampers in the ventilation system are closed
- emergency shutdown (ESD) of the platform is initiated.
Fire extinguishing system
This protects personnel, structures and equipment throughout the platform (including the shafts). Two types of system are installed:
- wet, using water or foam
- dry, using powder (and halon earlier).
The wet system is supplied by the fire water pumps installed on the service deck. Fixed foam extinguishers are positioned in areas with a high risk of oil fires. Halon
was originally used in technical spaces which contain much electrical and electronic equipment, but has been phased out. A large powder system has been
installed in connection with the helideck. In addition, fire extinguishers – both carbon dioxide and powder – have been positioned for quick response throughout the platform
Alarms
These are intended to warn of incidents which require a coordinated commitment by all personnel to saving life and maintaining platform safety. Alarms are given over the public address system, either as a signal or as a verbal announcement.
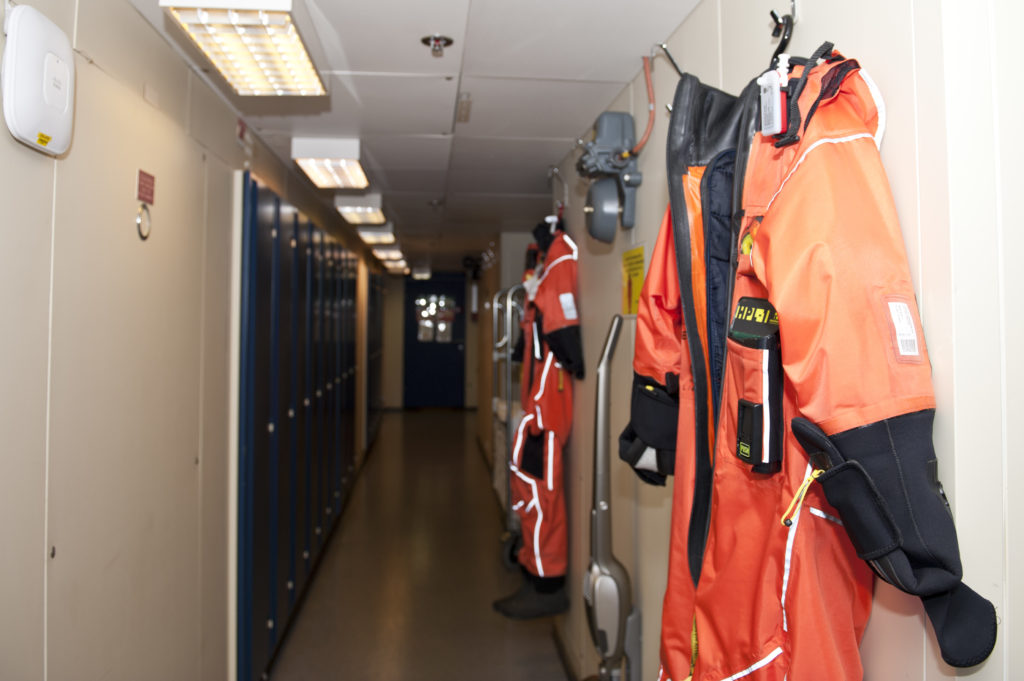
Rescue/safety equipment
This is intended to permit speedy evacuation of personnel from the platform in an emergency, or to retrieve people who have fallen overboard. It includes:
- covered free-fall lifeboats
- covered rafts which inflate on contact with the sea
- man-overboard boats (MOBs)
- chutes for evacuation to the sea
- personal survival suits.
Communication
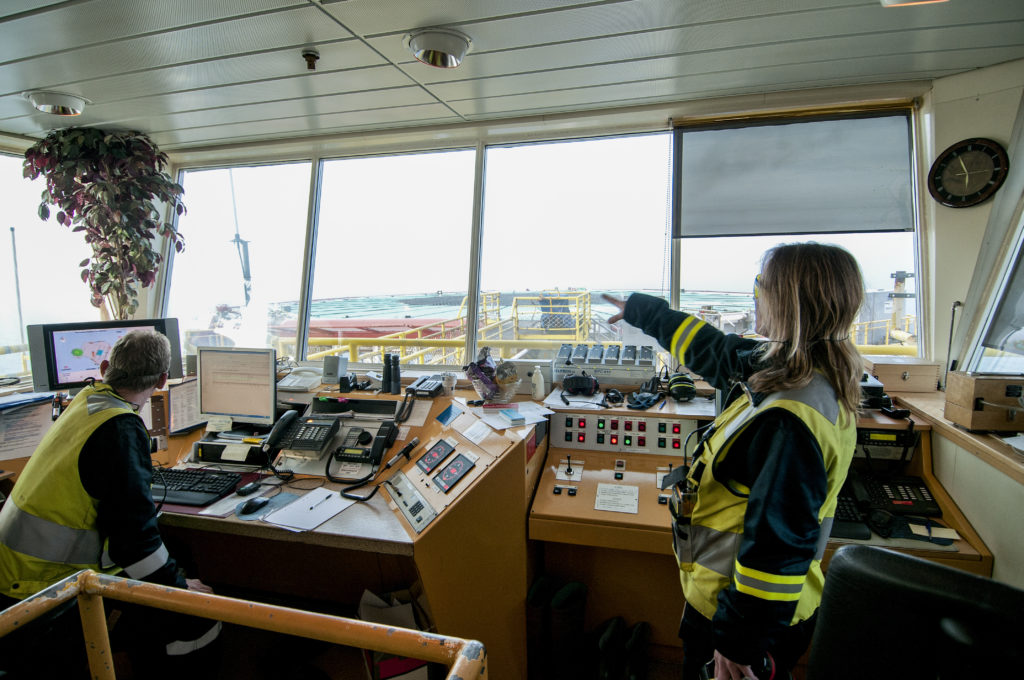
Rapid advances have been made in this area since Statfjord came on stream. The following
thereby describes both the original position and the current systems.
External communication
These systems provide the necessary links between the platforms and contacts on land, at sea and in the air.
1980
The satellite system installed on Statfjord A was intended to the main carrying channel for communication between the field and the Norwegian mainland. Communication
to/from the B and C platforms was relayed over line-of-sight microwave links to Statfjord A for onward transmission. Were the satellite system to go down, VHF and MF radio communication would take over. An emergency phone system provided direct communication with land.
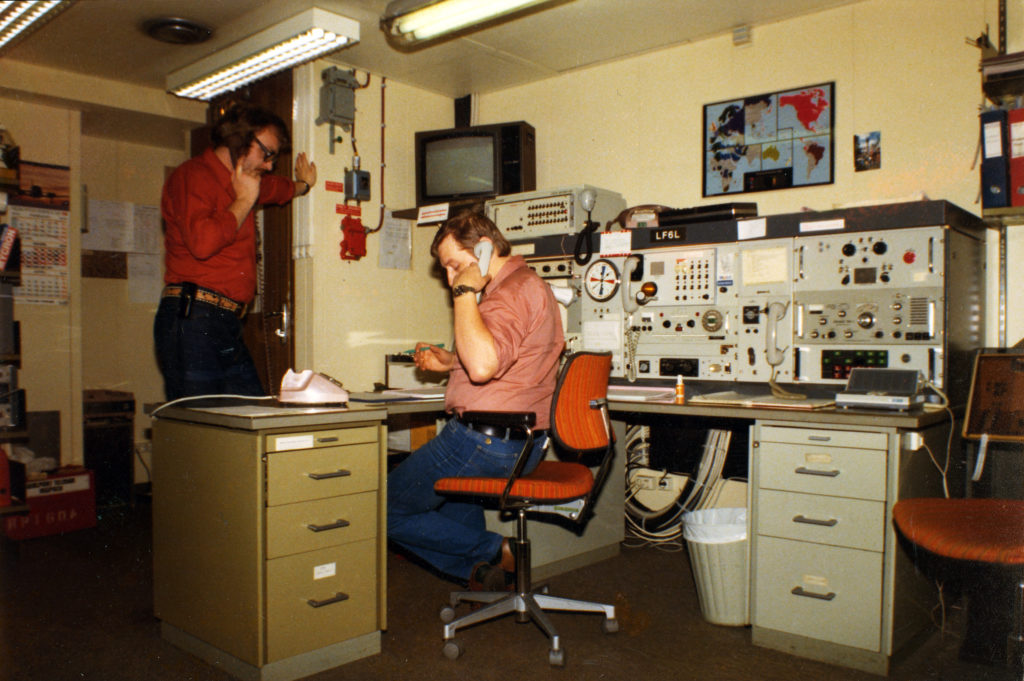
The radio shack on the A platform kept in touch with helicopters via VHF (AM) radio and with ships via VHF and MF communication. Crane drivers could communicate directly with ships using VHF radio-telephones operating on the marine frequency.
A telemetry system linking the platforms was designed for fail-safe operation during transfer of crude oil between the installations. The control room on each platform monitored and coordinated the oil pumps. This system also had a speech channel for communication between the control room and the loading buoy/shuttle tanker.
Walkie-talkies were used where phones were impractical. This system provided a back-up for the phone network, the public address system and ship-to-ship communication.
The internal phone system was operated from the radio shack. This was also the location for the telex system, which was operated via the satellite link.
2010
Microwave links (point-to-point by line of sight) installed on Statfjord A and B provide the two main carrying channels from Statfjord to Gullfaks and on via fibreoptic cable to the Norwegian mainland. Should one channel drop out, all communication is automatically transferred to the other. Communicationfrom Statfjord C is transmitted via microwave links to Statfjord A and B for onward transmission to land. An emergency system provides direct mobile phone communication with land via Gullfaks.
Communication managers on the platforms maintain contact with helicopters via VHF (AM) radio and with ships using VHF. Crane drivers also communicate directly with ships using VHF radio-telephones operating on the marine frequency.
A telemetry system linking the platforms is designed for fail-safe operation during transfer of crude oil between the installations. Changes to the loading buoys (see the separate article) mean that this system is now also used for communication between platform and tanker. The control room on each platform monitors and coordinates the oil pumps. A speech channel for communication between the control room and the shuttle tanker is also provided by the telemetry system.
Walkie-talkies and the internal telephone system function by and large in the same way as they did in the 1980s. The telex system is no longer in use.
Computer network
A revolution has taken place in computer technology since Statfjord came on stream. The platforms are currently equipped with a broadband network linked to Statoil’s computers on board and on land, and to the internet. This network is also used for videoconferencing between the platforms and the Statoil offices on land.
Internal communication
Internal communication systems have been installed to safeguard day-to-day operation and to protect important information flows in the event of a rescue or emergency. Today’s systems have naturally been modernised, but still include a public addresssystem, intercoms, an internal telephone network, and sick bay alarms and call-outs. The original closed-circuit TV facility has been replaced today by an internal monitoring system based on video cameras, and the sickbay alarm is now provided by a pager. A significant contribution to secure communication is provided by the installation of a repeater system, which ensures radio communication coverage of the whole platform.
UHF radio communication is extensively used at present in day-to-day operation of the platform and, in the event of an alarm sounding, for search and rescue teams and the fire brigade.
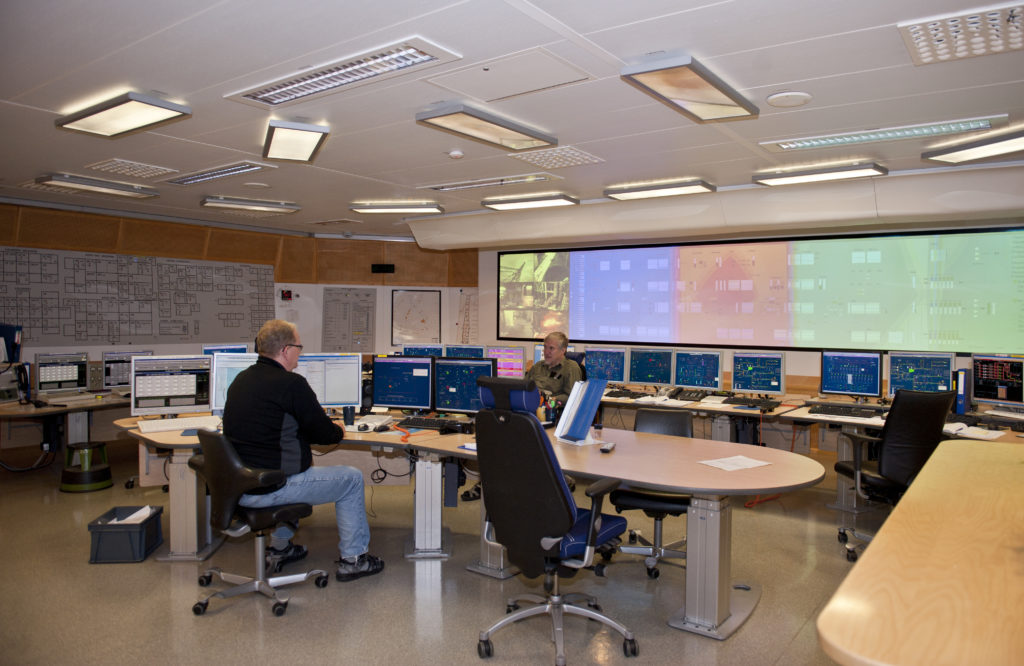
Control room
The control room is placed in a secured area, where process operators monitor and control the various process and service systems. Two
separate monitoring and control systems are provided:
- a control and information system for safe operation and shutdown, with a duplicated control system for ballast tank level
- a supervisory control and data acquisition (Scada) system which monitors and checks production, drilling, transport and other connected processes.
Process data are read off automatically by the system to provide the basis for dynamic process diagrams and tabulated reports presented to the operators. Possible changes to the status of a monitored process are presented as colour changes on the displays.