Gas treatment
Natural gas removed from the wellstream through pressure reduction is a mix of several different light hydrocarbons, with methane as the main component. Ethane, propane and butane are also present. Statfjord’s gas production was initially injected back into the reservoir.

Once Statpipe became operational in 1984, however, the Norwegian share of that output was transported to Kårstø. This processing plant north of Stavanger separated out the various components (a process known as fractionation) for onward sale. From 2007, all the natural gas from Statfjord has been piped to the UK via the Tampen Link pipeline and Britain’s gas gathering system.
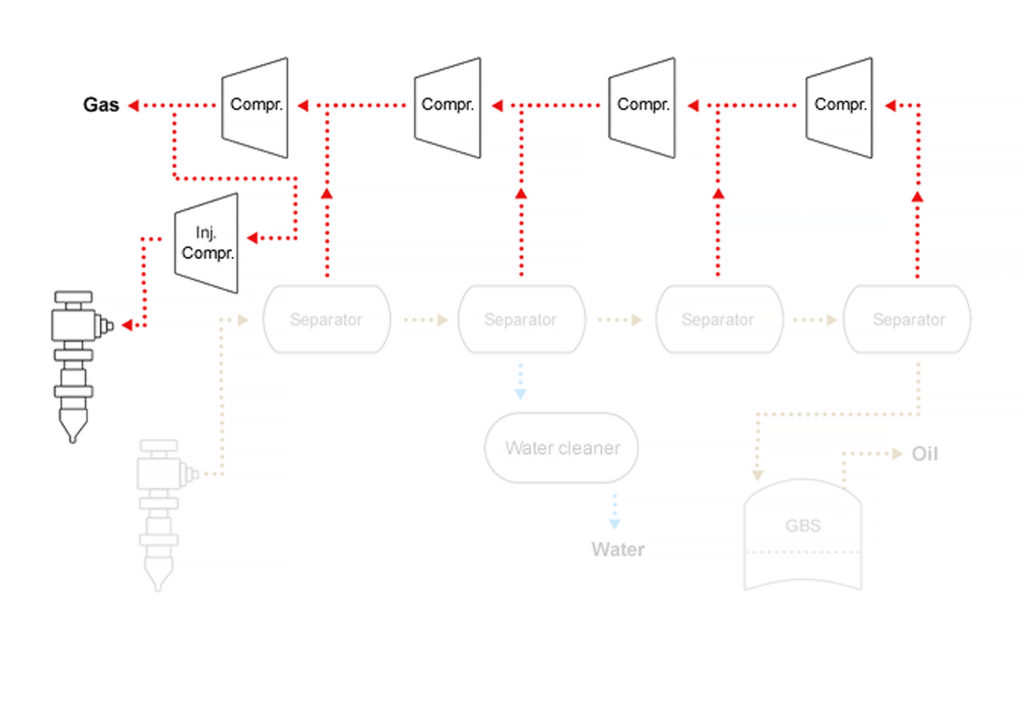
More about process
close
Close