Building Statfjord C

Another project team was accordingly appointed by the licensees to consider alternative development solutions for the northern part of the field. This work was to take account of reservoir properties, safety, and operational and maintenance friendliness. But the main emphasis would be on simplifying equipment, reducing weight and optimising construction methods. The concept had to be cheaper than Statfjord B.
Variations on the table ranged from a subsea development to a two-platform solution. One question was whether Statfjord C should be a satellite to the A platform, with drilling capacity alone, or a separate structure with processing and storage facilities.
The first option was a combined drilling, quarters and water injection platform with a daily production capacity of 285 000 barrels. It would have a concrete substructure, but without drilling or loading opportunities.
Produced oil would be piped directly from the wellhead to Statfjord A for processing. The drawback was that this would not be possible until output began to decline on the A platform and spare capacity became available.
The second solution was an integrated production, drilling and quarters (PDQ) platform with water injection capabilities, which could process 180 000 barrels per day (b/d) and transfer a further 150 000 b/d to Statfjord A. This would be supported on a steel jacket, and the use of tankers for both storage and loading of crude was envisaged.
The final option considered in this round was a PDQ platform with 180 000 b/d in processing capacity. It would rest on a three-shaft Condeep concrete gravity base structure (GBS) with storage. Loading would use the buoys on Statfjord A and B.
Further studies of detailed estimates for costs and timetables were carried out with these variants until 22 January 1980, when the licensees decided on the third option – an integrated PDQ platform.
To benefit from both time and cost savings, Statfjord C was intended to be a duplicate of the B platform. But this was not achieved – it was only an approximate copy of Statfjord B. The differences were not necessarily easy to spot, but had great significance for production, safety and living conditions.
The biggest change was that the C platform was dimensioned to produce 210 000 b/d from 19 wells, compared with 180 000 from 15 wells on Statfjord B.
Since the gas processing train on Statfjord C had been completed when the platform reached the field, it became the first installation on the field to deliver to the Statpipe network running to Kårstø north of Stavanger and on to Emden in Germany via Ekofisk.
The most visible change was the helideck, which was elevated to avoid the wind forces and turbulence created by the drilling module on Statfjord B. Because the helideck on the latter was below the level of other structures, helicopter traffic to and from the platform had faced problems. When the wind was in a certain direction and stronger than a stiff breeze, flights could neither land nor take off. So the Statfjord C helideck rose high and free above the rest of the topside, as if on stilts.
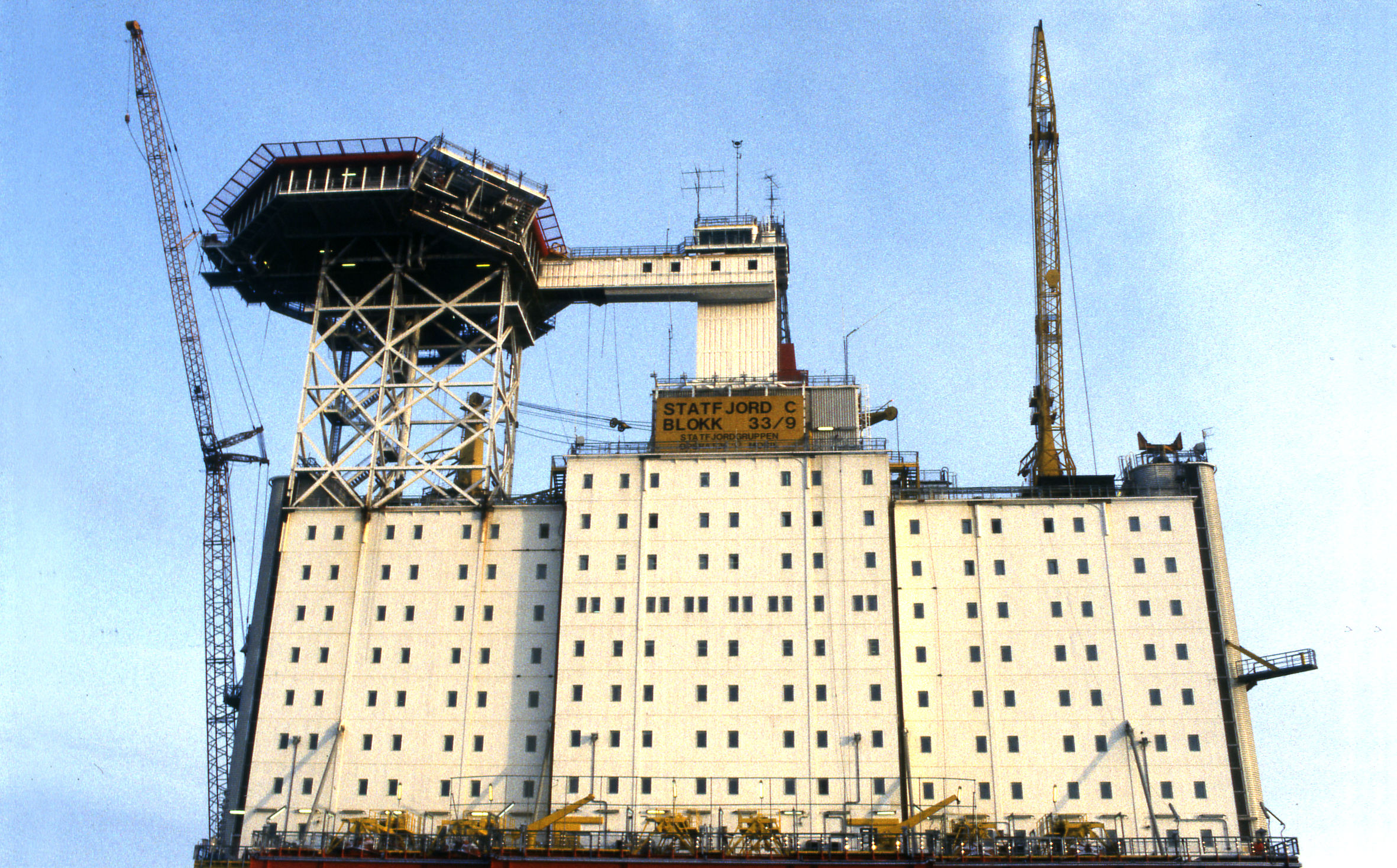
The size of the living quarters was also increased, from 200 berths on the B platform to 272. This was achieved by placing an extra storey of cabins on top, and moving the stairwells to the sides. An additional storey for ventilation equipment was installed above that again.
Seabed conditions at the northern end of the field, where Statfjord C was to be installed, were firmer than further south. This meant that the base of its GBS did not have to be as large as it was on B – 14 000 square metres compared with 18 000. The design of the steel skirts under the base was amended.
Since the plans called for a larger production capacity, the diameter of a number of pipes had to be increased. At the same time, the tanks for separating gas from oil were provided with new internal equipment to boost their efficiency.
Another type of gas dewatering facility was also specified. This involved a contractor pump to remove water from the gas with triethylene glycol, instead of injecting glycol into a heat exchanger. A similar system was later installed on both A and B platforms.
Other equipment made it possible to increase water injection rates to 296 000 b/d – and actually as high as 350 000 b/d if necessary – compared with 272 000 b/d on Statfjord B. In addition, ballast pump capacity was expanded. But the main structure and most of the equipment were indeed copied from the B platform.
Approved and initiated
The official approval given for Statfjord B also applied to the C platform, and the concept for the latter was approved in a letter to operator Mobil on 24 December 1980.
Norway’s offshore supplies industry was impatient to get going on the third Statfjord platform. Employment in the engineering industry was still down in 1979, and a rapid development was the only way to close the gap facing the Norwegian oil-related industrial sector.
After the licensees had resolved to build Statfjord C, however, rumours began to circulate of changes to petroleum taxation in Norway. The price of crude oil had risen sharply, and the Norwegian government wanted to capture more of the consequent profits. It planned to raise tax on these earnings from 70 to 80 per cent. Such schemes create problems.
International conditions provided the background for the rising prices. Put briefly, Egypt signed the Camp David accord in 1978. Iraq maintained that this represented a betrayal of the Arab cause, and only Saudi Arabia prevented Egyptian isolation at the Arab summit in November 1978.
The consequence was instead that the Saudi role in the Organisation of Oil Exporting Countries (Opec) was weakened. Its efforts to secure moderation on the issue of raising oil prices accordingly failed to win through at the Opec meeting in December. The organisation raised prices by 10 per cent during 1979.
This was paralleled by political unrest in Iran. The Shah’s position had been weakened since the autumn of 1978, and extensive strikes at Iranian petroleum facilities reduced production. Panic began to spread in western oil markets. The Shah was forced to leave Iran in January 1979 and Ayatollah Khomeini came to power two months later.
Iranian oil production continued to decline, creating uncertainty in the market. Opec failed to bring oil prices under control in the spring and summer of 1979, demand rose and spot prices reached new heights. High spot prices also prompted producers to demand supplements on the official price, which boosted their revenues. The Norwegian government wanted to secure its slice of these increased profits through higher taxes.
A number of the Statfjord licensees were unhappy at the thought of tax changes, and wanted to discuss a possible cancellation of the C platform. Mobil took the lead on these efforts.
Investment costs were weighed against income potential, and showed – according to Mobil’s calculations – that the new operating parameters imposed by the government would make the profitability of Statfjord C doubtful. Unless income for the Statfjord licensees was improved, Mobil would propose that the platform be dropped.
The shipyard crisis was still not over in 1980, and a refusal to build Statfjord C would have had serious consequences for jobs in Norway’s engineering industry. Some eight million working hours would be lost. The Federation of Norwegian Industries (MVL) accordingly supported Mobil and took contact on its own account with the Ministry of Industry. It feared that the new tax rules might prompt the postponement of construction contracts.
Opponents of the new tax argued that three platforms would make it possible to regulate production in a way which ensured optimum utilisation of all the installations and the whole field. For its part, the Ministry of Finance maintained that Mobil had failed to take account of the increased oil price in its calculations.
It nevertheless transpired that cross-party consensus prevailed on the tax changes. The main opposition parties – the Conservatives, the Christian Democrats and the Centre Party – found the increase reasonable and accepted the Labour government’s proposal to raise the tax on profits to 80 per cent. The Socialist Left and the Liberals would have been happy to go even further.
A decision on building Statfjord C was due to be taken by the Statfjord Unit Operating Committee (SUOC) in July 1980. Mobil was uncertain about support for its proposal to drop the platform, and proposed a test vote. This showed that the operator was the only opponent of building the platform.
Mobil did not want to be directly voted down, and proposed that the order of voting be reversed so that it did not have to cast a ballot first. Since the majority for building Statfjord C was binding, the operator abstained. Once the decision had been made, however, it tackled the job with great enthusiasm.
Compensation claims
The City of Stavanger was sued in 1980 by five homeowners in Hinnasvingen and Hindalsveien, who primarily wanted GBS construction operations in Hinnavågen to cease. They also demanded compensation of NOK 100 000 each for damage and nuisance, or up to NOK 20 000 per property per year for future problems.
The claimants alleged that they were subject to noise and intrusive illumination from the powerful spotlights used at night. Their view had also been destroyed.
While the court agreed that all the properties had suffered nuisance from the activity, this was not of any special character and could not be expected to be different if other industry had been located there. It could not be considered unreasonable. The judge found in favour of the city, and Condeep construction could continue. But the council was not awarded costs.
Since the city had clearly told the homeowners that the construction work was temporary and would not continue beyond 1978, the latter felt they had been misled when it became clear that the work was set to go on for many years.
Source: Stavanger Aftenblad
Constructing the GBS
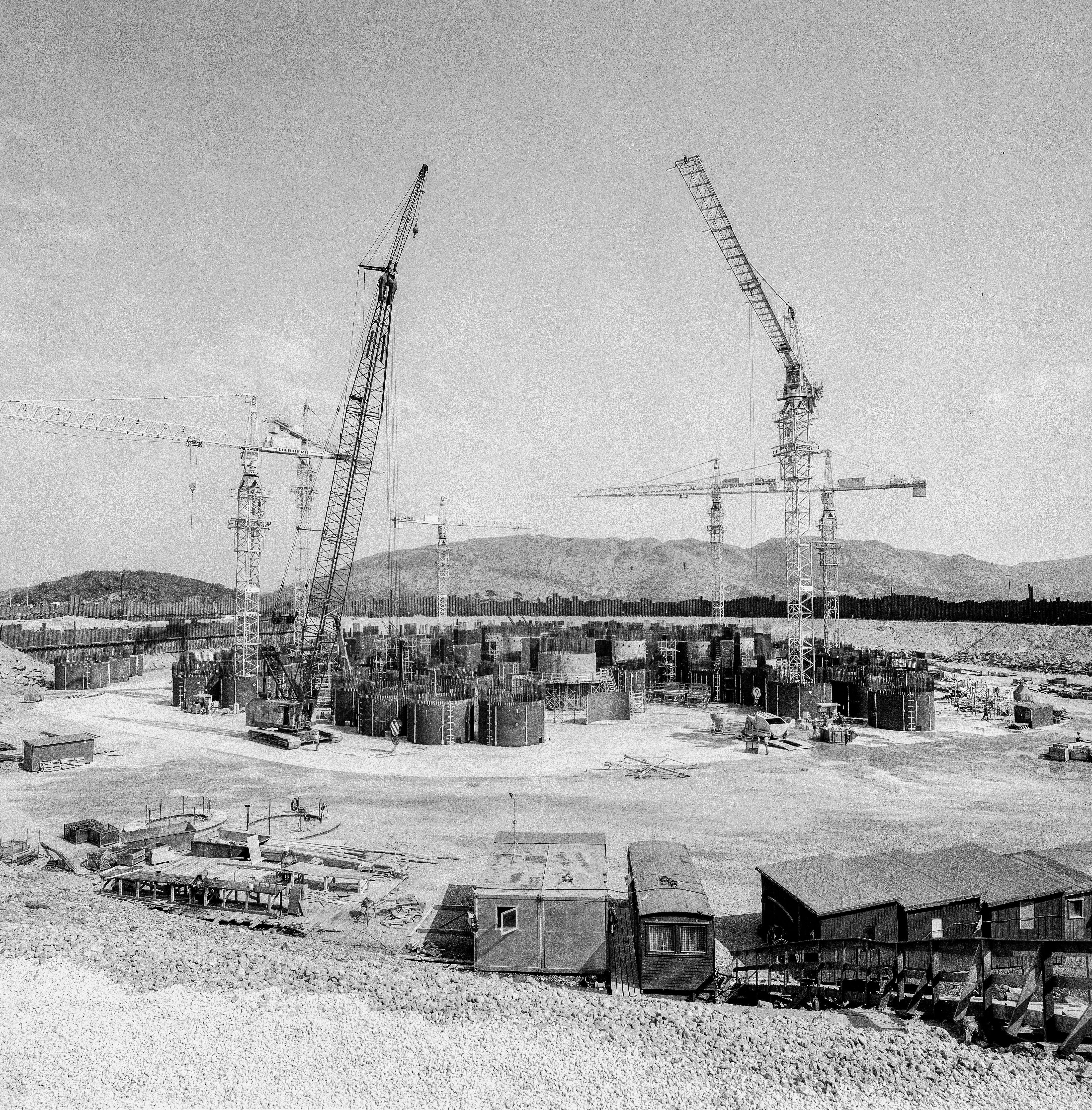
Constructing the GBSNorwegian Contractors (NC) began work on building the concrete GBS for Statfjord C on 10 November 1980, before the contract had officially been signed, in order to employ personnel it wanted to retain. The sheet pile retaining wall was re-established by 1 December, and notifications issued to shipping in the Gands Fjord.
The NC contract was the first awarded for the Statfjord C construction project, and covered a four-shaft GBS. This structure was virtually identical to Statfjord B, with 20 oil storage cells forming its bottom section. Each cell could store 260 000 tonnes of crude.
NC needed 200 additional permanent employees, and 1 500 people would be working at the Hinnavågen facility during the most hectic phase when the shafts were slipformed. Schoolchildren and students once again had the chance to earn a few thousand kroner during the four weeks that this operation would take.
Installation of the steel skirts to ensure that the platform stood stably on the field started during January. NC’s design personnel only had a short time to do their work before construction began in the dock. Bottom conditions at the Statfjord B and C sites differed greatly, and a completely new base structure was required.
The computers used to calculate pressure, stress and other key conditions lacked the capacity that such machines now possess. It took them 12.5 days to conduct the global analysis ¬– the most extensive of the lot – covering stresses in the concrete.
Physical work in the dry dock could begin on 12 January 1981. Three years later, on 18 January 1984, after a three-day delay because of bad weather, the concrete structure could leave the Gands Fjord off Stavanger for Vats and mating with the topside.
Adding it all up
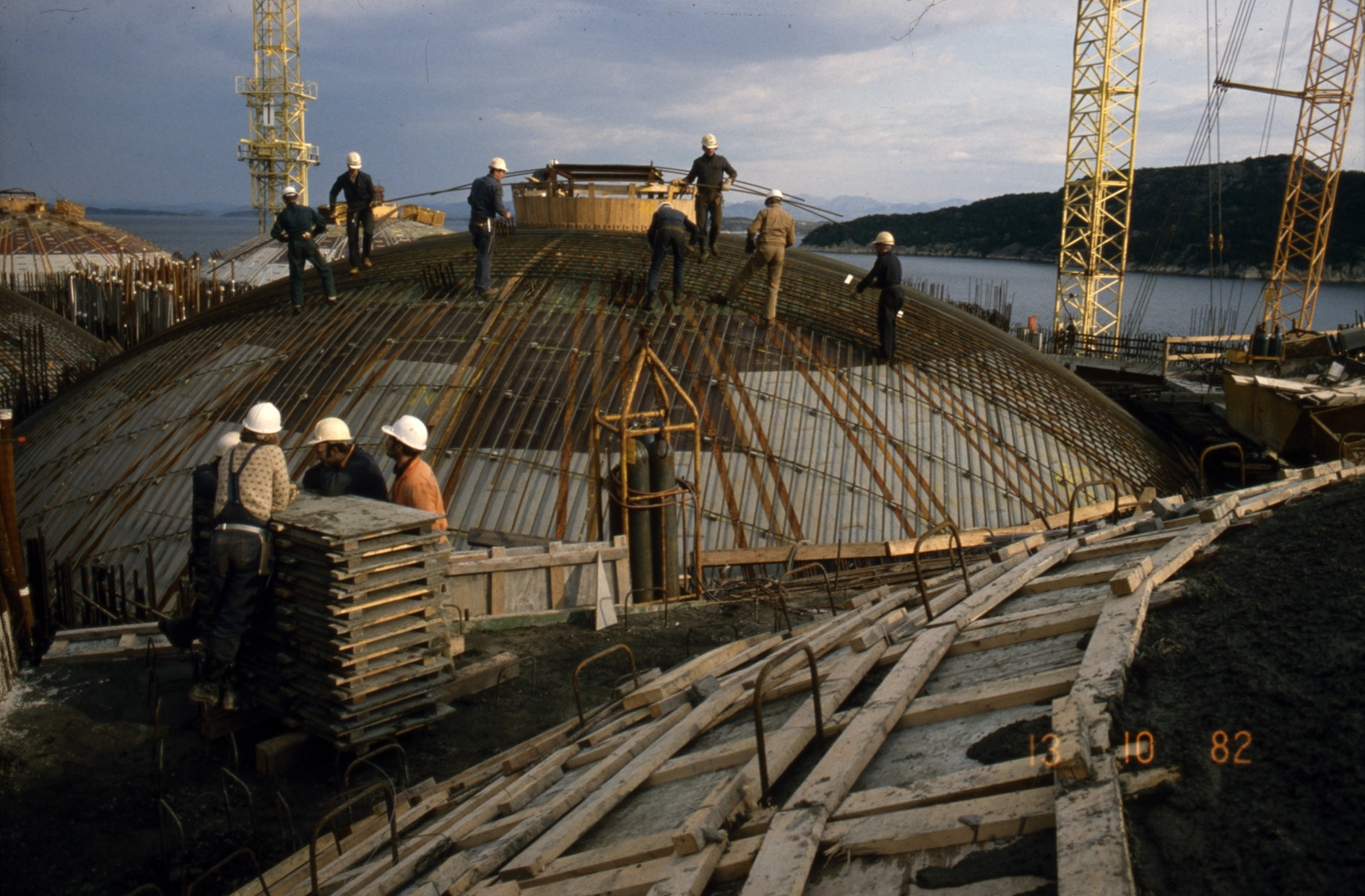
The concrete GBS had a base area of 12 800 square metres, and 24 cells with an internal diameter of 23 metres. These stood 64 metres high, with the exception of four which were extended as shafts to a height of 176 metres.
With a dry weight of 600 000 tonnes, the structure contained 13 000 cubic metres of concrete and 35 000 tonnes of reinforcement bars (rebars) – equivalent to five Eiffel Towers.
In addition, the project went through three tonnes of coffee, 60 000 pairs of gloves, 3 000 crowbars, 12 000 rebar fixings, 5 000 plastic buckets and 4 000 spanners. But a new communication system meant that consumption of walkie-talkie batteries declined by 200 000 compared with Statfjord B.
Organisation
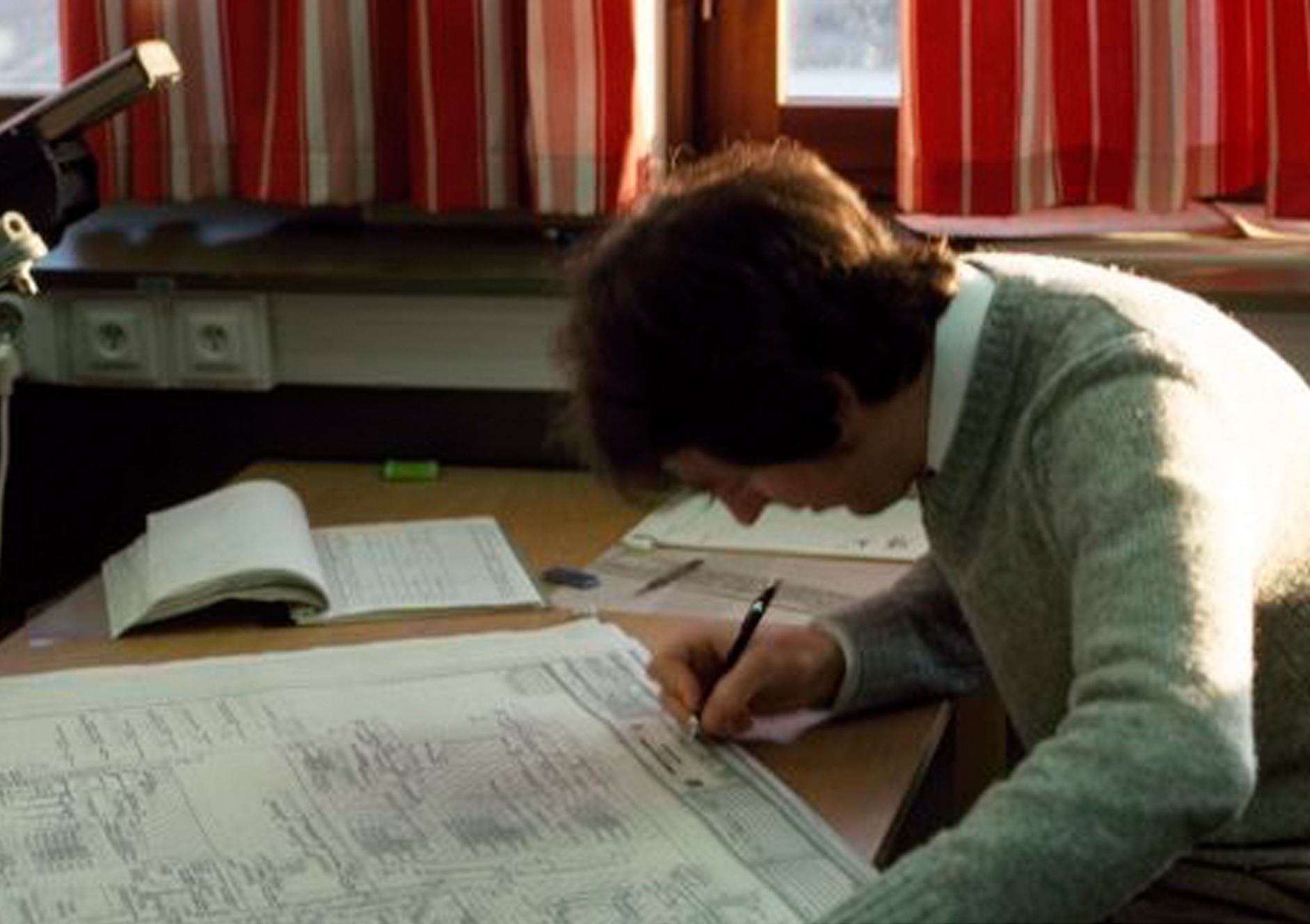
The main consultant for constructing Statfjord C was Norwegian Petroleum Consultants (NPC). This company had also worked on Statfjord B, but was now in partnership with Britain’s Foster Wheeler (FW).
A project service contractor (PSC) team was located in Asker outside Oslo. This had two main jobs. The first of these was to provide engineering design services, including work on the tender documents. Sending out such packages of drawings, material specifications and deadlines to be included in a tender was a big job. In addition came receiving, assessing and negotiating on bids and ultimately awarding contracts.
Second, the PSC was to make provision for purchasing equipment and services for the platform. Other tasks included making specialists available to the operator and cost controllers, keep accounts and award contracts. Totalling 340 people, the team comprised three Norwegians for every Briton.
Mobil also had its own staff of 50-60 personnel in Asker, including six from Statoil. This group was known as the project task force (PFT). Its job was to monitor work by the PSC and the other contractors, and to provide advice, conduct checks and issue approvals.
The project management job was simpler and less extensive than for Statfjord B. About 6 000 main and 5 000 detailed drawings were required for the C platform. Fifty per cent of these could be copied directly from the B drawings, 40 per cent had to be revised on the basis of existing documents, and only 10 per cent – a few hundred – of the main drawings had to be created from scratch.
Engineering design was divided among several contractors. NPC did about 60 per cent of the work, primarily on the topside modules and all electrical and installation design. Canada’s Triocean designed the drilling derrick and modules, and Moss Rosenberg Verft (MRV) did the cellar deck. Leirvik Sveis designed and built the living quarters.
Other contracts
The Statfjord group tried to achieve a wider distribution of the topside work on this occasion. It had the quarrel between Aker and MRV over the topside contract for Statfjord B fresh in its mind when putting the C platform out to tender.
But it was difficult for others to compete with MRV over the job, since it had developed a facility tailored for the B topside. Since Statfjord C would be very similar, the Kværner company was very strongly placed. Nobody else turned out to be interested, so the job of fabricating and hooking-up the steel topside went to MRV without competitive tendering.
If MRV was the only candidate for building the topside and its assembly and hook-up, competition was tougher for mechanical outfitting of the GBS shafts. Bids were submitted by NC itself as well as by Aker Contracting ¬– a newly established company which recruited personnel from all Aker group members – and the Kværner-Rosenberg Joint Venture (KRJV) between Kværner group subsidiaries MRV, Kværner Engineering and Kværner Brug.
An initial evaluation found that Aker had the lowest bid and NC the highest, thereby eliminating latter. But none of the bids were in the form Mobil wanted. A new round was held, and the KRJV maintained that it could make an improved offer after securing better terms for materials and services from sub-contractors. It reduced its bid by NOK 25 million.
Mobil was unsure whether this represented a genuine price reduction or an attempt to submit a new bid, and also gave Aker another chance. The two competitors submitted final bids with revised prices. Both had achieved substantial reductions – Aker by NOK 33 million and the KRJV by no less than NOK 72 million from its original bid. The latter accordingly won the job, but the real winners from the big price cut were naturally Mobil and its fellow Statfjord licensees.
Mechanical outfitting of the concrete shafts was performed by a joint venture between Kværner Brug in Oslo, Kværner Egersund and MRV’s Rosenberg Verft in Stavanger. These companies fabricated and installed 9 500 tonnes of decks and equipment in the shafts and cells. These structures were lifted into the GBS by the Ugland group’s Uglen crane ship.
Statoil called for an extraordinary meeting of the SUOC to discuss the assessment of bids for the module support frame (MSF). This was to be built in three sections – two ends and a centre piece. Five bids had been received from Kværner Egersund, Fredrikstad Mekaniske Verksted (FMV), a German yard and two in the UK.
The lowest prices were offered by Britain’s McDermott and Germany’s Howaldtswerke. Both Egersund and FMV were 20 per cent higher. Overall, this meant that the Norwegian yards were NOK 33 million more expensive.
Statoil nevertheless took the view that the Statfjord group should opt for the Norwegian fabricators, who had experience and would probably deliver on schedule. The issue was submitted to the Ministry of Petroleum and Energy, which refused to take a position. Statoil was forced to accept the lowest bids, and the work went to Germany and the UK.
Construction time for Statfjord C was extended by almost half a year compared with Statfjord B, from 30 to 35 months. That reduced the need for peak staffing, and day-to-day work became less hectic. Making the structure a virtual copy of the B platform meant that fewer drawings were needed, with less extra work for MRV, and allowed a number of smaller jobs to be contracted out to other fabricators when the company could not compete on price.
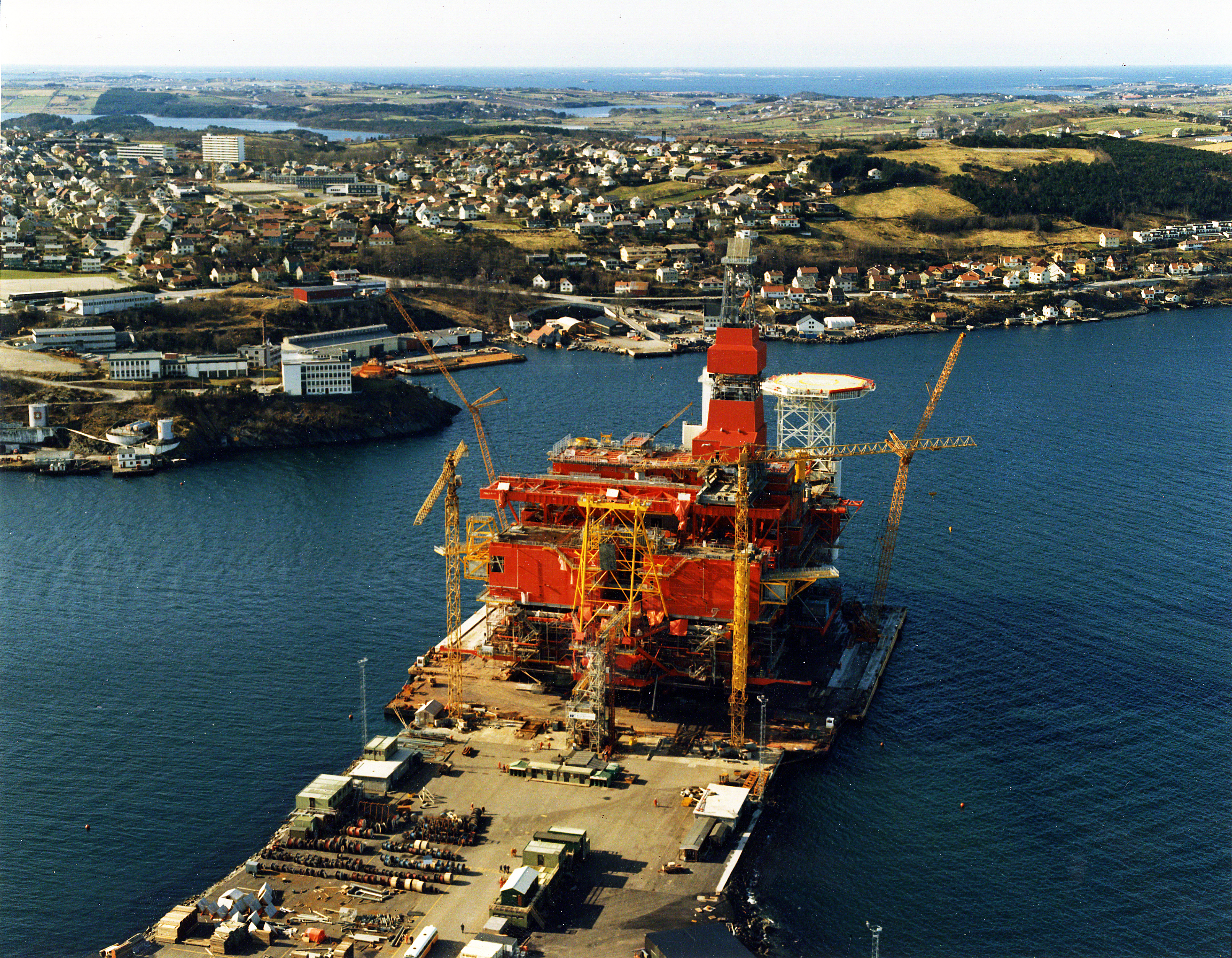
While the construction contracts were virtually the same as for Statfjord B, they contained a built-in performance element. This was intended to encourage the contractors to reach clearly defined sub-targets and increase productivity by 15 per cent on all work to be done on a cost plus basis.
Building a close copy of the B platform yielded benefits. Work proceeded without problems throughout 1982, and the project was ahead of schedule by the end of that year. Forecasts looked even better towards the summer of 1983. Outfitting of the GBS was no less than three months ahead of schedule, and it could be delivered almost three weeks before the original contractual date in February 1984.
Overview of supplier
- Project management: NPC and Foster Wheeler
- Engineering: NPC (module deck, electrical, instrumentation), Triocean (drilling derrick and modules) and Moss Rosenberg Verft (cellar deck)
- Construction concrete GBS: NC
- Mechanical outfitting of GBS: Moss Rosenberg Verft in cooperation with Kværner Brug and Kværner Egersund
- Topside construction and hook-up: Moss Rosenberg Verft
- Fabrication of MSF: Howaldswerke, McDermott and Stord Verft
- Living quarters: Leirvik Sveis
In addition to these main contractors, deliveries and equipment came from about 250 different companies worldwide.
Sources
Kostnadsanalysen norsk kontinentalsokkel: report from the management group appointed by royal decree of 16 March 1979, submitted to the Ministry of Petroleum and Energy on 29 April 1980.
Norsk Oljerevy. (1980). no 6. Mobil: Statfjord C fremdeles uøkonomisk.
Norsk Oljerevy. (1983). no 12. Statfjord C – 800 000 tonn stål og betong.